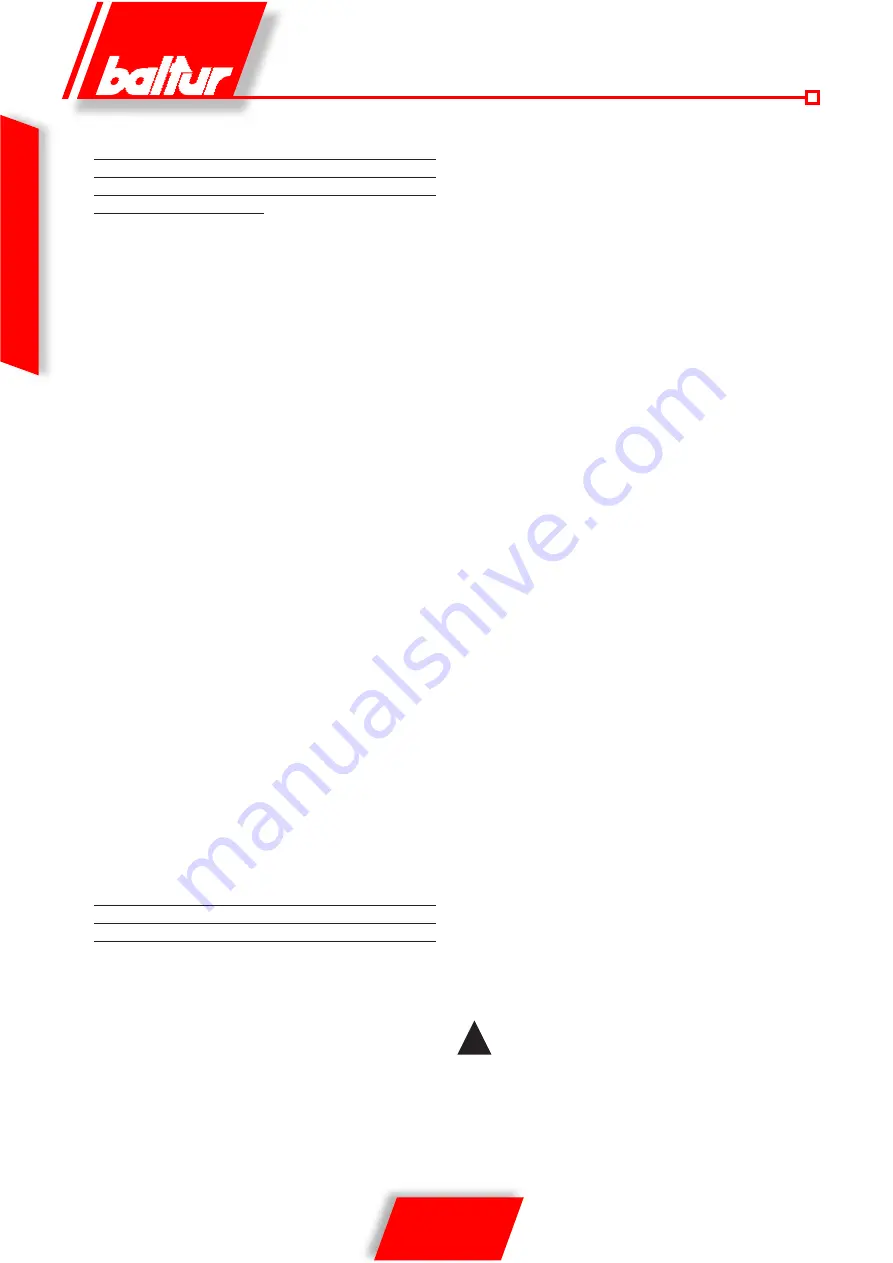
12 / 22
0006081436_201611
E
N
G
L
I
S
H
optimal value of 10 % or 0
2
= 3% for maximum supply.
It is essential to check, with a suitable instrument, that
the percentage of carbon monoxide (CO) present in
the fumes does not exceed the limit set by regulations
at the time of installation.
11) After setting the burner to the minimum thermal
output, put the modulation connector switch to
the MAX position. The air adjustment servomotor
is put at "maximum" and consequently also
the gas supply reaches the maximum thermal
output. Afterwards a check is carried out on the
quantity of gas supplied, by reading the meter.
With the burner on at the maximum supply
available, the gas output is found by calculating
the difference between two readings exactly
one minute apart. The difference between the
two readings should be multiplied by sixty in
order to obtain the flow per hour (60 minutes).
Multiplying the flow per hour (m
3
/h) by the
calorific power of the gas, the power supplied in
kcal/h is obtained which must corrispond or be
very close to that required by the boiler (lower
calorific power for methane = 8550 kcal/h).
You must not keep the burner running if the capacity
is greater than the maximum permitted amount for
the boiler, or there is a risk it could be damaged. It is
therefore best to stop the burner immediately after
the two meter readings.
12)To vary the maximum supply of gas output, use the air output
regulator because the gas output automatically adjusts to the
air supply. It is therefore necessary to use the cam which ad
-
justs the maximum opening position of the air damper (see ad
-
justment instructions 0002933651). The opening angle of the
air damper has to be reduced to reduce the gas supply and
viceversa. To vary the air/gas ratio see the instructions for the
pneumatic gas valve installed.
13) Subsequently check combustion with the special instruments.
For a correct air/gas ratio you must find a carbon dioxide (CO
2
)
value for the methane that is at least 8 % or O
2
=6% at minimum
burner supply up to an optimal value of 10 % or O
2
= 3% for
maximum supply.
It is essential to check, with a suitable instrument, that the per
-
centage of carbon monoxide (CO) present in the fumes does
not exceed the limit set by regulations at the time of installation.
14)After setting operation to the maximum thermal output, it is nec
-
essary to put the air adjustment servomotor to the minimum
flow position, putting the modulation connector to the MIN posi
-
tion. With the burner operating at minimum power, in the event
it is necessary to vary the combustion conditions, follow the
adjustment instructions for the pneumatic gas valve installed.
It is very important to carry out an instrument assisted check
on combustion and modify, where necessary, the initial visual
setting, this must also be effected in a series of intermediate
positions of the modulation range set for the air damper.
15)Now check the proper automatic operation of modulation.
16) The air pressure switch has the purpose of switching the equip
-
ment into the safety (lock-out) state if the air pressure is not
what it should be. The pressure switch must therefore be set to
close the contact (closed during operation) when air pressure
in the burner is sufficient. Please note that if the contact meant
to be closed during operation does not close (insufficient air
pressure), the equipment carries out its cycle but the ignition
transformer is not switched on and the fuel valves do not open.
As a result, the burner stops in a blocked state. To verify that
the air pressure switch is operating correctly, while the burner
is ignited on first flame only, increase the adjustment value until
the switch triggers an instant “blocked” stoppage of the burner.
Release the burner by pushing the appropriate button and read
-
just the pressure switch until preventilation air pressure can be
detected. The pressure switch connection circuit is self control
-
ling. Therefore, the contact which is meant to be closed in a non
operating state (fan stopped and thus no air pressure in burner),
should in fact be in this state, otherwise the command/control
equipment will not be switched on (burner remains inoperative).
17) The pressure switches for checking gas pressure (minimum
and maximum), if installed, prevent the burner from operating
when the gas pressure is not between the expected values. The
specific function of the pressure switches clearly reveals that
the pressure switch for controlling minimum pressure must use
the contact which is closed when the pressure switch detects a
pressure value above the value it is set to, while the pressure
switch for controlling maximum pressure must use the contact
that is closed when the pressure switch detects lower pressure
than the value it is set to. Minimum and maximum gas pressure
switches must be set when the burner is tested. Setting de
-
pends on pressure detected from time to time. Tripping of any of
the gas pressure switches (in the sense of opening the circuit)
will therefore prevent the equipment and therefore the burner
from working. While the burner is operating (flame lit) the trip
-
ping of the gas pressure switches (circuit opening) causes the
burner to stop immediately. When testing the burner, it is very
important to check that the pressure switches are working prop
-
erly. By using the adjustment devices, it can be verified whether
the pressure switch that stops the burner actually operates (i.e.
opens the circuit).
18) Check the triggering of the flame detector (ionisation elec
-
trode). Open the connector in the ionization electrode lead and
switch on the burner. The equipment must run through its cycle
completely and, three seconds after the ignition flame has
formed, “lock-out”. This check must also be carried out when
the burner is already on. By opening the connector, the equip
-
ment must immediately go into its “lock-out” action.
19) Check the proper working of the boiler thermostats or pressure
switches (when triggered they must stop the burner).
!
Check that ignition is correct because if the mixer is shifted
forward, the outgoing air speed may be too high to permit
ignition. In such a case, it is necessary to move the mixer
backwards degree by degree until reaching the position in
which the ignition is regular and accept this new position
as definitive. We remind you that is preferable, in the case
of the small flame, to limit the quantity of air to the least
possible needed for safe ignition, even in the most difficult
circumstances.
Summary of Contents for TBG 35 PN
Page 2: ......
Page 24: ...22 22 0006081436_201611 I T A L I A N O...
Page 46: ...22 22 0006081436_201611 E N G L I S H...
Page 47: ......