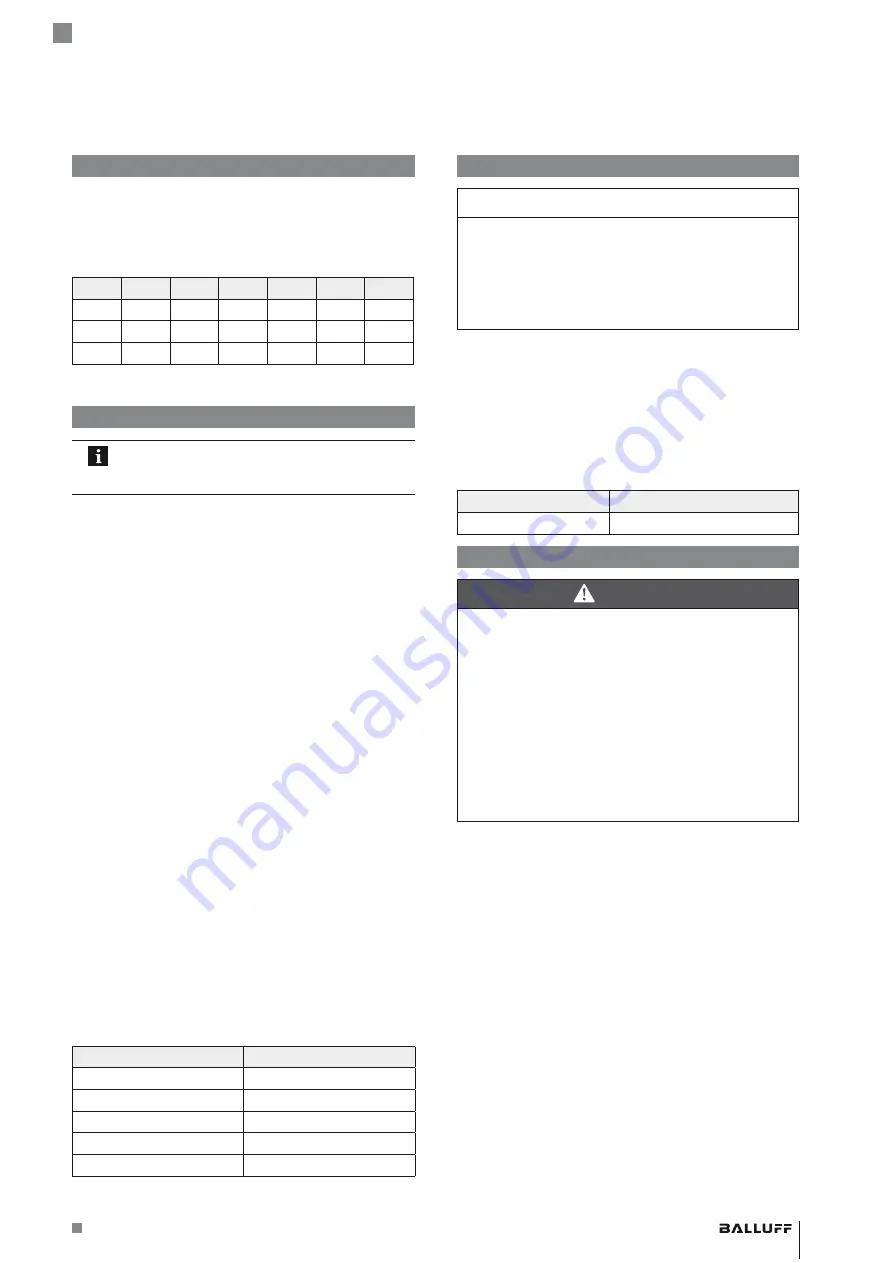
www.balluff.com
2
Configuration
Station address: Values 0…127 allowed
Value 0…125 = station address
Value 126 = address 126 or the address set by
Set_Slave_Address
Value 127 = reset BTL to its default condition
S1.1
S1.2
S1.3
S1.4
S1.5
S1.6
S1.7
2
0
2
1
2
2
2
3
2
4
2
5
2
6
LSB
MSB
1
2
4
8
16
32
64
Bus termination S1.9 and S1.10 = ON
Shielding and cable routing
Defined ground!
The transducer and the control cabinet must be
at the same ground potential.
Shielding
To ensure electromagnetic compatibility (EMC), observe
the following:
– Connect transducer and controller using a shielded
cable.
Shielding: Braided copper shield with minimum 85%.
– Shield is internally connected to connector housing.
Magnetic fields
The position measuring system is a magnetostrictive
system. It is important to maintain adequate distance
between the transducer cylinder and strong, external
magnetic fields.
Cable routing
The Profibus bus line must be routed according to
Technical Guideline 2.111, Installation Guidelines for
PROFIBUS-DP/FMS
.
When ducting the cable between the transducer, controller,
and power supply, it is important to avoid going near high
voltage cables due to interferences. Inductive stray noise
from AC harmonics (e.g. from phase angle controls) are
especially critical and the cable shield offers very little
protection against this.
The signal is transmitted to the controller via the
PROFIBUS DP interface.
Cable twisted in pairs, shielded.
Maximum length of the entire field bus cable: 1200 m
The bus must be terminated at both ends in accordance
with EN 50170.
The transfer rate depends on the length of the cable:
Cable length
1)
Baud rate [kBit/s]
1)
< 100 m
12000
< 200 m
1500
< 400 m
500
< 1000 m
187,5
< 1200 m
93,7/19,2/9,6
1) Values in accordance with EN 50170
No. 931999 EN ∙ J16; Subject to modification.
english
Installation
NOTICE!
Interference in function
Improper installation can compromise the function of the
transducer and result in increased wear.
►
The mounting surface of the transducer must make
full contact with the supporting surface.
►
The bore must be perfectly sealed (flat seal).
Only use the proper nut for the mounting thread. Firmly
tighten the transducer with a maximum torque of 100 Nm.
For horizontal assembly with nominal lengths > 500 mm,
support the rod and tighten it at the end if necessary.
If installed in a hydraulic cylinder, the magnet should not
make contact with the outer rod. Minimum bore diameter
in the support piston:
Rod diameter
Bore diameter
10.2 mm
At least 13 mm
Startup
DANGER
Uncontrolled system movement
When starting up, if the position measuring system is
part of a closed loop system whose parameters have not
yet been set, the system may perform uncontrolled
movements. This could result in personal injury and
equipment damage.
►
Persons must keep away from the system's
hazardous zones.
►
Startup must be performed only by trained technical
personnel.
►
Observe the safety instructions of the equipment or
system manufacturer.
1.
Check connections for tightness and correct polarity.
Replace damaged connections.
2.
Turn on the system.
3.
Check measured values and adjustable parameters
(especially after replacing the transducer or after repair
by the manufacturer). Recalibrate the transducer, if
necessary.
Operating notes
– Check the function of the transducer and all associated
components on a regular basis.
– Take the position measuring system out of operation
whenever there is a malfunction.
– Secure the system against unauthorized use.
BTL5-T1 _ _ -M _ _ _ _ -A/B-SA211/SA311-S103
Micropulse Transducer - Rod Style