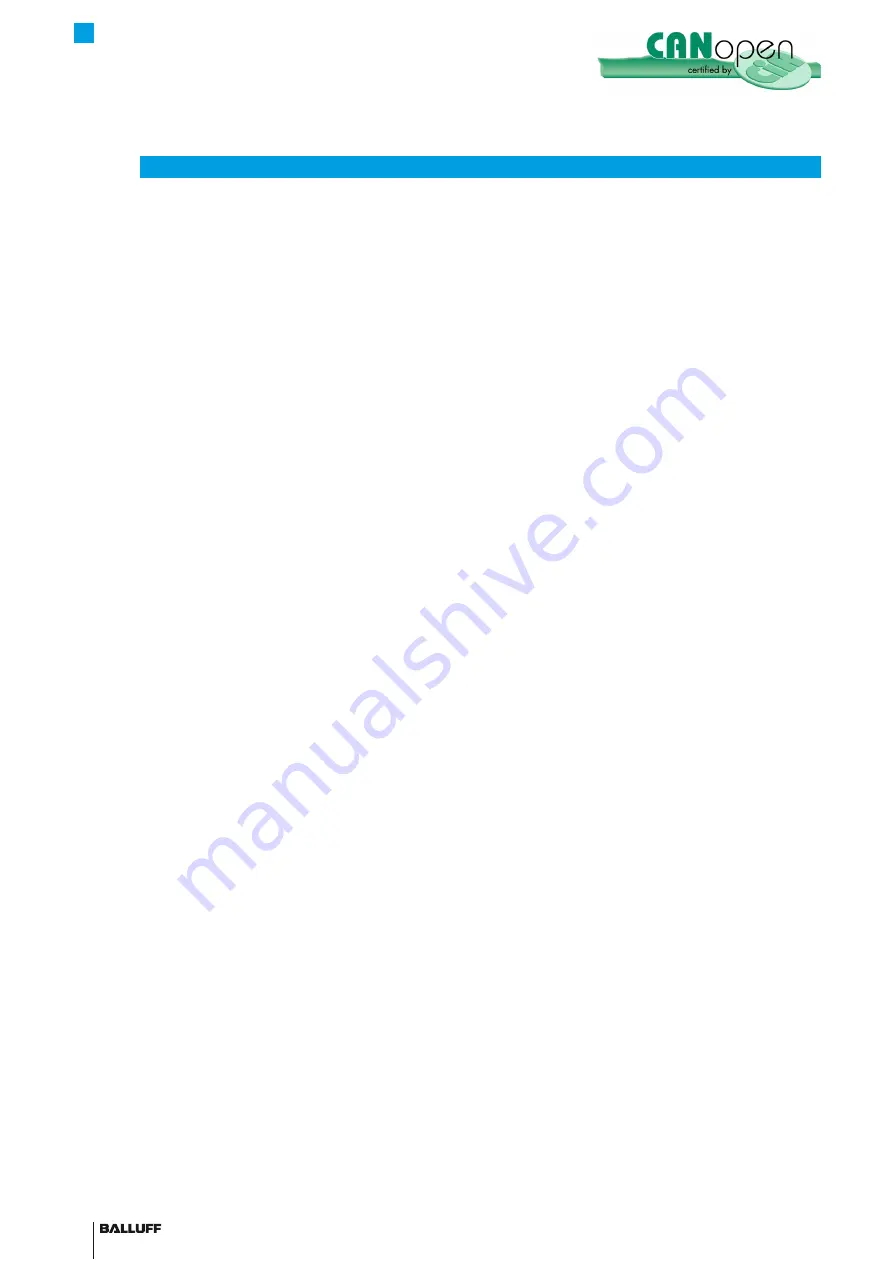
6
english
Node identification
3.1
The BTL5-H1_... micropulse transducer is operated on the
CAN bus and constitutes a node in the bus system. It
functions in CAN networks for CANopen, CAL, and layer 2.
Unique identification of the BTL measuring systems is
done using the LSS and LMT data, which is permanently
stored in the unit, e.g.:
Manufacturer:
BALLUFF
Device name:
BTL0500
Serial number:
05042212345678
Settings using the LMT/LSS service:
Bus parameters
–
Transmission speed (baud rate)
–
Node number (node ID)
–
Operating parameters
3.2
Micropulse transducer model types BTL5-H1... are
supplied with encoder profile DS 406. The settable
parameters in the CAN communication profile and
operating parameters can be changed using the SDO
service (via the master).
Setting via the SDO service:
CAN communication profile
–
Mapping and transmitting or turning off the PDOs
–
Setting guard time,
–
life time factor, and heart beat
BTL5-H1... operating parameters
–
Number of magnets
–
Resolution of position and velocity
–
Setting switching points/cams with hysteresis and
–
polarity
Working range
–
Zero point
–
Cycle time of the PDO
–
The CAN communication module integrated in the BTL
converts the data generated in the BTL into CAN
messages and sends them on the CAN bus.
The following communication objects are used for sending
messages on the CAN bus:
Process data objects (PDOs)
–
The BTL data for position, velocity, and cam status are
sent with up to 16 PDOs. The data is freely
configurable in the 8 bytes of each PDO.
Service data object (SDO)
–
The SDO is used to send the parameters for
configuring the transducer.
In addition, the SDO can be used to access information
in the object directory (OD) (e.g. error messages from
the error register).
System description of BTL5-H1... on CAN bus
3
Emergency object
–
Emergency objects are used to report errors. The BTL
also uses the high priority of the emergency object for
sending the cam status (see Chapter 5.1).
Synchronization object (SYNC)
–
SYNC is used to synchronize the communication on
the bus.
System start
3.3
After a power-on (or after a reset), the CAN communication
module is started according to the status diagram in
Fig. 3-1 on page 7.
Initialization
3.3.1
state
The CAN communication module is initialized in this state.
Loading of device-specific parameters is initiated by the
CAN communication module. The CAN communication
module takes over the device-specific configuration
parameters. After this, the data is ready for transmitting.
After initialization is concluded, the CAN communication
module automatically goes into the
pre-operational
state.
Simultaneously, data transmission from the BTL module to
the CAN communication module is enabled.
Pre-operational
3.3.2
state
In this state, the measuring system can be configured
using a master application/control via the CAN bus.
Communication is done over a 'peer to peer'
communication channel which is established using a
service data object (SDO). The ID numbers which the SDO
needs are determined based on the node number
according to the ID allocation procedure used in the
CANopen standard.
The ID numbers for the SYNC, emergency, and process
data objects (PDOs) are also assigned according to the ID
allocation procedure used in the CANopen standard. If the
system is being used in a CANopen network, ID
assignment is handled by a distributor (DBT master).
When configuring using a master application, make sure
that only correct parameters are entered in the object
directory, since the CAN communication module is not
capable of performing any consistency and value range
checks.
Configuration of the node number (node ID) and the baud
rate can be carried out in the
pre-operational
state. After a
change is made, the system starts with the new
parameters and the default settings in the object directory,
and then returns to the
pre-operational
state.
BTL5-H1...
Configuration and CAN linking - DS 406
Summary of Contents for BTL5-H1 M Series
Page 1: ...deutsch BTL5 H1 Konfigurationshandbuch...
Page 2: ...www balluff com...
Page 32: ...english BTL5 H1 Configuration Manual...
Page 33: ...www balluff com...