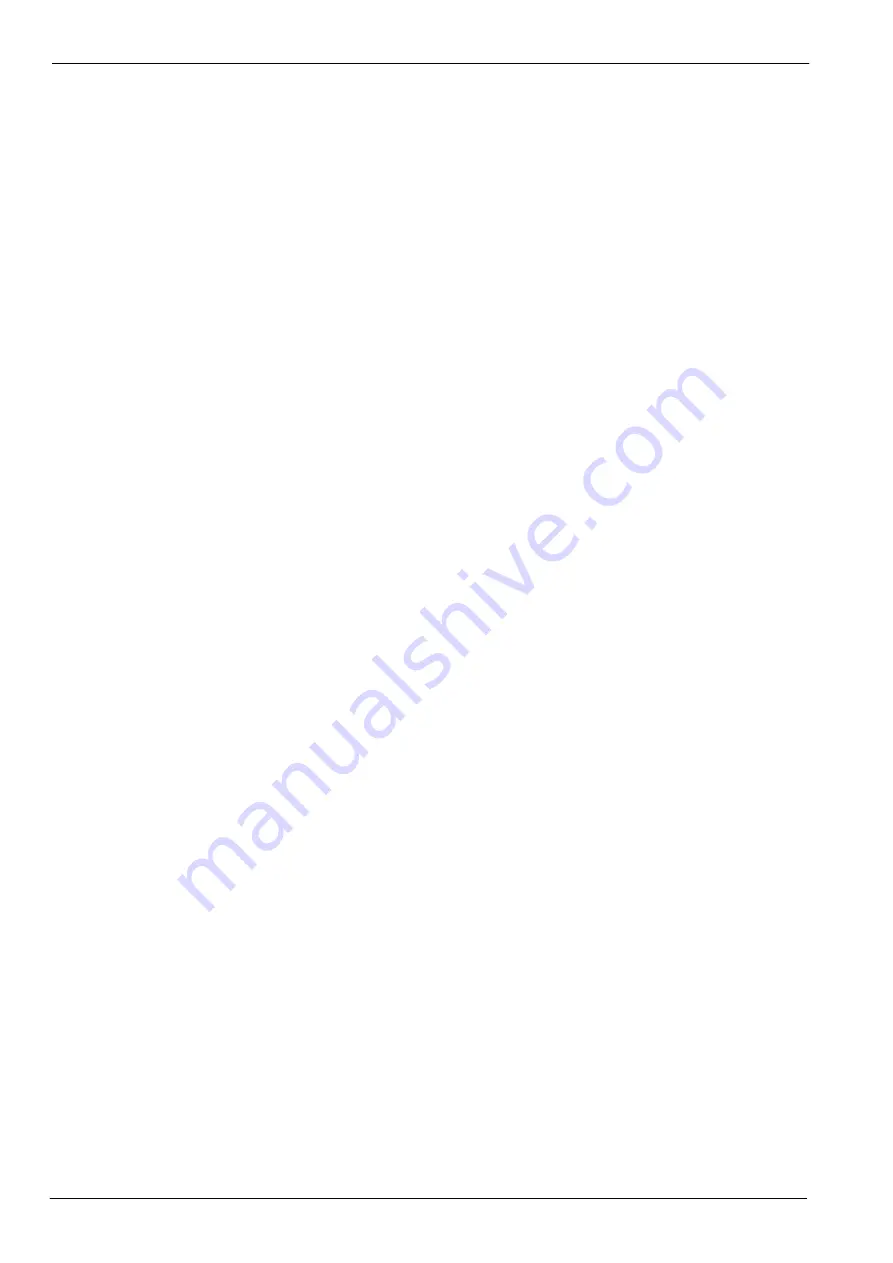
3-4 Setup
MN1917
3.2
Commissioning and Tuning
If you checked the Launch Commissioning Wizard option, the Commissioning Wizard will start automatically.
Each type of motor and drive combination has slightly different performance characteristics. Before the Flex+Drive
II
can be used to control the motor accurately, the Flex+Drive
II
must be “tuned”. This is the process where the
Flex+Drive
II
powers the motor in a series of tests. By monitoring the feedback from the motor’s resolver or encoder
and performing a number of calculations, the Flex+Drive
II
can make small adjustments to the way it controls the
motor. This information is stored in the Flex+Drive
II
EEPROM, which means commissioning is not necessary after
each power cycle.
The Commissioning Wizard and Autotune provide a simple way to tune the Flex+Drive
II
and create the necessary
configuration information for your drive/motor combination.
3.2.1
Using the Commissioning Wizard
When you have completed a screen, click
Next >
to display the next screen. If you need to change something on a
previous screen, click the
< Back
button. The Commissioning Wizard remembers information that you have entered
so you will not need to re-enter everything if you go back to previous screens. For the demonstration unit, use the
settings listed below:
Welcome
Check the
I am starting a new application...
option.
Select metric or imperial measurement as required by the customer.
Motor type
Rotary Brushless Motor is already selected, so no action is necessary on this screen.
Select Motor
Use the
Select motor by Catalog number
option.
For new demonstration units, enter BSM 50N 133 A E.
For upgraded units, enter the motor catalog number that was noted during the upgrade procedure (section A.2.1).
Confirm Motor and Drive
No action necessary on this screen, apart from highlighting that WorkBench v5 has sourced all the detailed motor
parameters from its internal database.
Feedback
For new demonstration units, no action is necessary on this screen; the encoder resolution has been selected from
the motor database.
For upgraded units, select 4096 in both drop down boxes.
Drive Setup complete
No action necessary on this screen.
Operating mode
If not already selected, choose the Position / Pulse Follower option.
Current Control
No action necessary on this screen.
Speed Control
In the Application Max Speed box, enter 3500.
Position Control
A number of parameters must be changed on this screen. In later demonstrations, parameter files will be used to
alter these settings (and others) when necessary.
Max Position Error:
For new demonstration units, enter 1000. For upgraded demonstration units, enter 4096.
Idle Position Tolerance: For new demonstration units, enter 10. For upgraded demonstration units, enter 40.
Idle Velocity:
For new demonstration units, enter 250. For upgraded demonstration units, enter 1000.
Positioning SPEED:
For new demonstration units, enter 200000. For upgraded demonstration units, enter 819200.
Accel Time to SPEED: For new and upgraded demonstration units, enter 250.
Analog input
On the control panel, set the Analog In 0 potentiometer to the marked 0V position.
Click
Tune Offset
. This will calibrate the 0V (zero input) point for analog input 0.
Operation Setup complete
The Commissioning Wizard is now complete. Click
Next >
to continue.
Summary of Contents for Flex+DriveII
Page 1: ...Flex DriveII Demonstration Unit SERVO DRIVE Operating Manual 03 02 MN1917...
Page 2: ......
Page 6: ...1 2 General Information MN1917...
Page 8: ...2 2 Introduction MN1917...
Page 22: ...4 8 Basic Demonstrations MN1917...
Page 34: ...6 2 Specifications MN1917...
Page 40: ...Index MN1917...
Page 41: ......