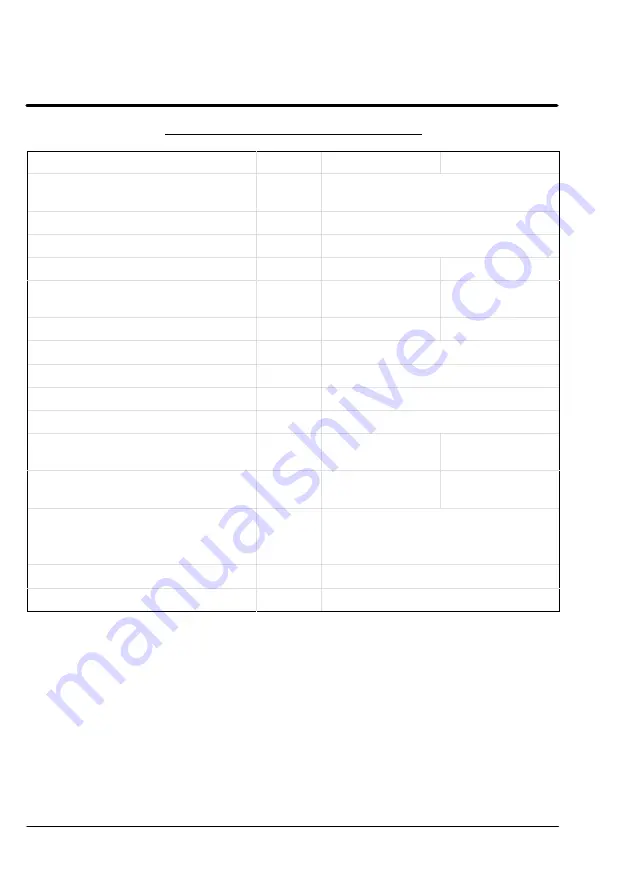
Section
2–2
MN1229
General Specifications
- 230VAC
Description
Unit
DBSC102-AAA
DBSC105-AAA
Input Voltage Range
(230VAC 1 Nominal)
VAC
220 - 250
Input Frequency
Hz
50/60
±
5%
Nominal Output Bus (Range)
VDC
320 (50-350)
Nominal Current (
±
10%)
A
RMS
2.5
5
1
Peak Phase Current (
±
10%); 2.5s
±
.5s
A
RMS
5
10
Nominal Output Power
KVA
1.01
2.17
Efficiency
%
>97
Minimum Load Inductance
H
400
Nominal Switching Frequency
KHz
8.5
Mounting
–
Panel
Overall Dimensions
in (mm)
2.65x6.81x6
(67.5x173x152.5)
3.6x6.8x6
(92.5x173x152.5)
Weight
lbs (Kg)
2.73 (1.24)
(without heatsink)
4.69 (2.13)
(with heatsink)
Operating Altitude
Feet
(Meters)
To 3300 feet (1000 meters).
Above 3300 ft, derate 11% per
3300ft (1000m).
Operating Temperature
°
C
+5 to 40
Rated Storage Temperature
°
C
–25 to +70
1
DBSC 105 with additional heatsink.
All values at ambient temperature of 25
°
C unless otherwise stated.
General Specifications - 230VAC
Description
Input Voltage Range
(230VAC 10 Nominal)
Input Frequency
Nominal Output Bus (Range)
Nominal Current (±10%)
Peak Phase Current (±10%); 2.5s ±
.5s
Nominal Output Power
Efficiency
Minimum Load Inductance
Nominal Switching Frequency
Mounting
Overall Dimensions
Weight
Operating Altitude
Operating Temperature
Rated Storage Temperature
Unit
VAC
Hz
VDC
ARMS
ARMS
KVA
0/0
itH
KHz
in (mm)
lbs (Kg)
Feet
(Meters)
oc
oc
DBSC102-AAA D B S C 1 0 5 - A A A
220 - 250
50/60 ±5%
320 (50-350)
2.5
5
51
10
1.01
2
.
1
7
>97
400
8.5
Panel
2.65x6.81x6 3 . 6 x 6 . 8 x 6
(67.5x173x152.5) (92.5x173x152.5)
2.73 (1.24) 4 . 6 9 (2.13)
(without heatsink) ( w i t h heatsink)
To 3300 feet (1000 meters).
Above 3300 ft, derate 11% per
3300ft (1000m).
+5 to 40
—25 to +70
1 DBSC 105 with additional heatsink.
All values at ambient temperature of 25°C unless otherwise stated.
2-2
M
N
1
2
2
9
Artisan Technology Group - Quality Instrumentation ... Guaranteed | (888) 88-SOURCE | www.artisantg.com