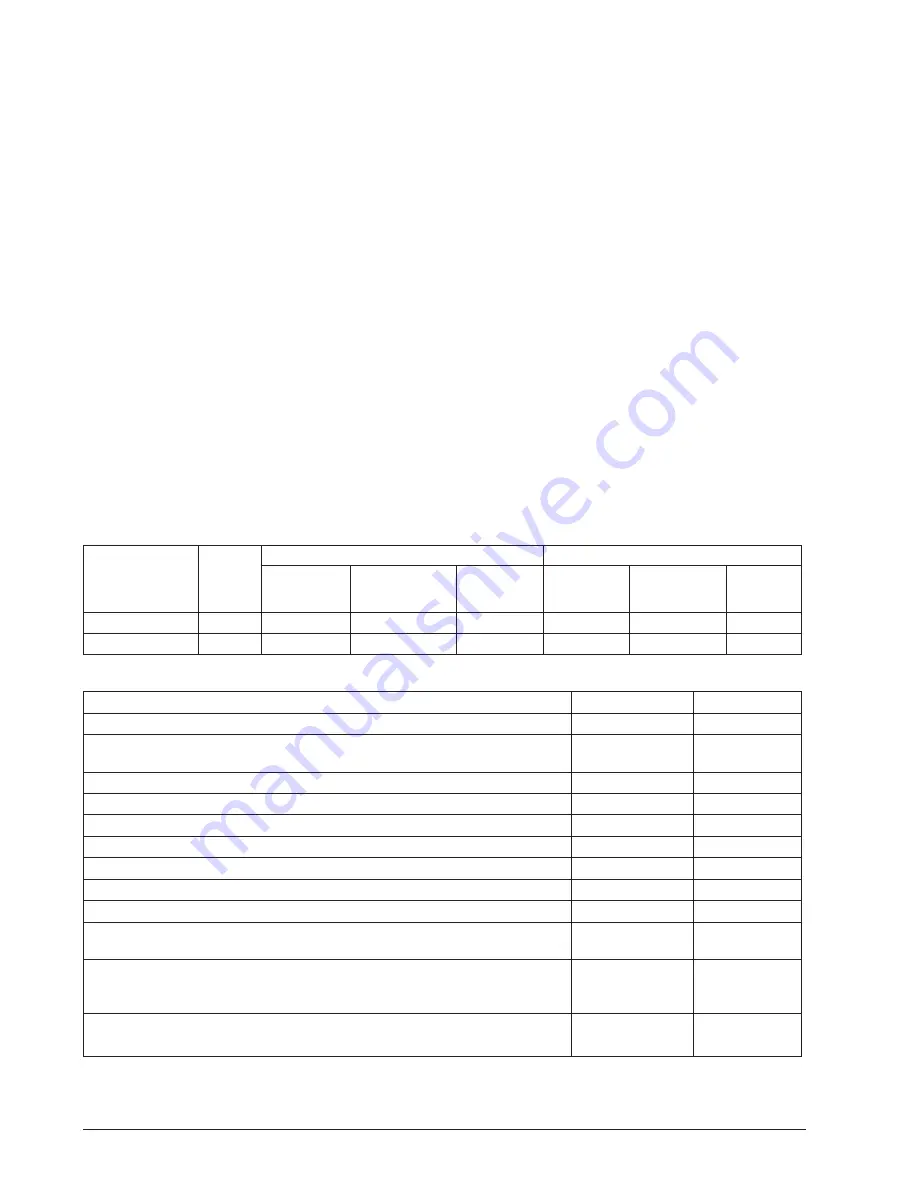
1-2
MN703
SAFETY NOTICE
Continued
WARNING: Do not use start/stop, inhibit or enable functions as a safety disconnect. Use only an AC line disconnect
for that purpose. Failure to observe this warning could result in severe bodily injury or loss of life.
Caution: Disconnect motor leads (A1 and A2) from control before you perform a Dielectric Withstand test on the motor.
Failure to disconnect motor from the control will result in extensive damage to the control. The control is tested
at the factory for high voltage / leakage resistance as part of Underwriter Laboratory requirements.
Caution: Do not connect AC power to the Motor terminals A1 and A2. Connecting AC power to these terminals
may damage the control.
Caution: Baldor recommends not to use Grounded Leg Delta transformer power leads that may create ground
loops. Instead, we recommend using a four wire Wye.
Caution: Suitable for use on a circuit capable of delivering not more than 5,000 RMS symmetrical short circuit
amperes listed here at rated voltage.
Caution: Adjusting the current limit above 150% of the motor nameplate rating can cause overheating and
demagnetization of the PM motor.
Caution: Do not leave the motor in a locked rotor condition for more than a few seconds since motor damage may occur.
Caution: Shunt wound motors may be damaged if field windings remain energized for an extended period of
time without armature rotation.
Receiving
Each control is thoroughly tested at the factory and carefully packaged for shipment.
When you receive your control, there are several things you should do immediately.
1. Observe the condition of the shipping container and report any damage immediately to the
commercial carrier that delivered your control.
2. Verify that the part number you received is the same as the part number listed on your purchase order.
3. Do not unpack until ready for use.
Table Electrical Ratings
AC Voltage
(± 15%, 50/60 Hz)
(VAC)
Motor
Voltage
(VDC)
Maximum Rating without Auxiliary Heat Sink
Maximum Rating with Auxiliary Heat Sink
AC Current
(RMS Amps)
DC Load Current
(Avg. Amps)
Power
(HP, (kW))
AC Current
(RMS Amps)
DC Load
Current (Avg.
Amps)
Power
HP (kW)
115
90 – 130
12.0
6.0
0.75, (0.6)
16.0
12.0
1 (.75)
230
180
12.0
6.0
1.5, (1.1)
16.0
12.0
2 (1.5)
Table 1-2 General Performance Specifications
1
Description
Specification
Factory Setting
Speed Range (Ratio)
50:1
—
Armature Feedback Load Regulation (0 - Full Load, 50:1 Speed Range)
(% Base Speed)
1
2
—
Line Voltage Regulation (at Full Load, ± 10% Line Variation) (% Base Speed)
0.5
2
—
Control Linearity (% Speed vs. Dial Rotation)
2
—
Acceleration (ACCEL) Trimpot Range (Seconds)
0.2 - 10
2
Deceleration (DECEL) Trimpot Range (Seconds)
0.2 - 10
2
Maximum Speed (MAX) Trimpot Range (% Base Speed)
50 - 110
2
100
Minimum Speed (MIN) Trimpot Range (% Base Speed)
0 - 30
2
0
CL/Torque Range (% Full Load)
0 - 200
150
IR Compensation (IR) Trimpot Range (at Specified Full Load at 90/180 Volts
Output) (Volts DC)
0 - 24 / 0 - 48
3 / 6
Operating Temperature Range without Optional Auxiliary Heat Sink
(Catalog
No. BC143) (°C / °F)
0 - 40 / 32 - 104
—
Operating Temperature Range with Optional Auxiliary Heat Sink
(Catalog No. BC143) (°C / °F)
0 - 50 / 32 - 122
—
1. CE Compliance requires BC24-LF RFI Filter. (See Optional Accessories, Table 1-2).
2. Performance is for 90 Volt PM motors with 115 VAC line input and 180 Volt DC PM motors with 230 VAC line input.
Summary of Contents for BC140
Page 1: ...6 15 Installation Operating Manual MN703 BC140 BC140 FBR DC CONTROL...
Page 4: ...ii MN703...
Page 17: ......
Page 18: ......