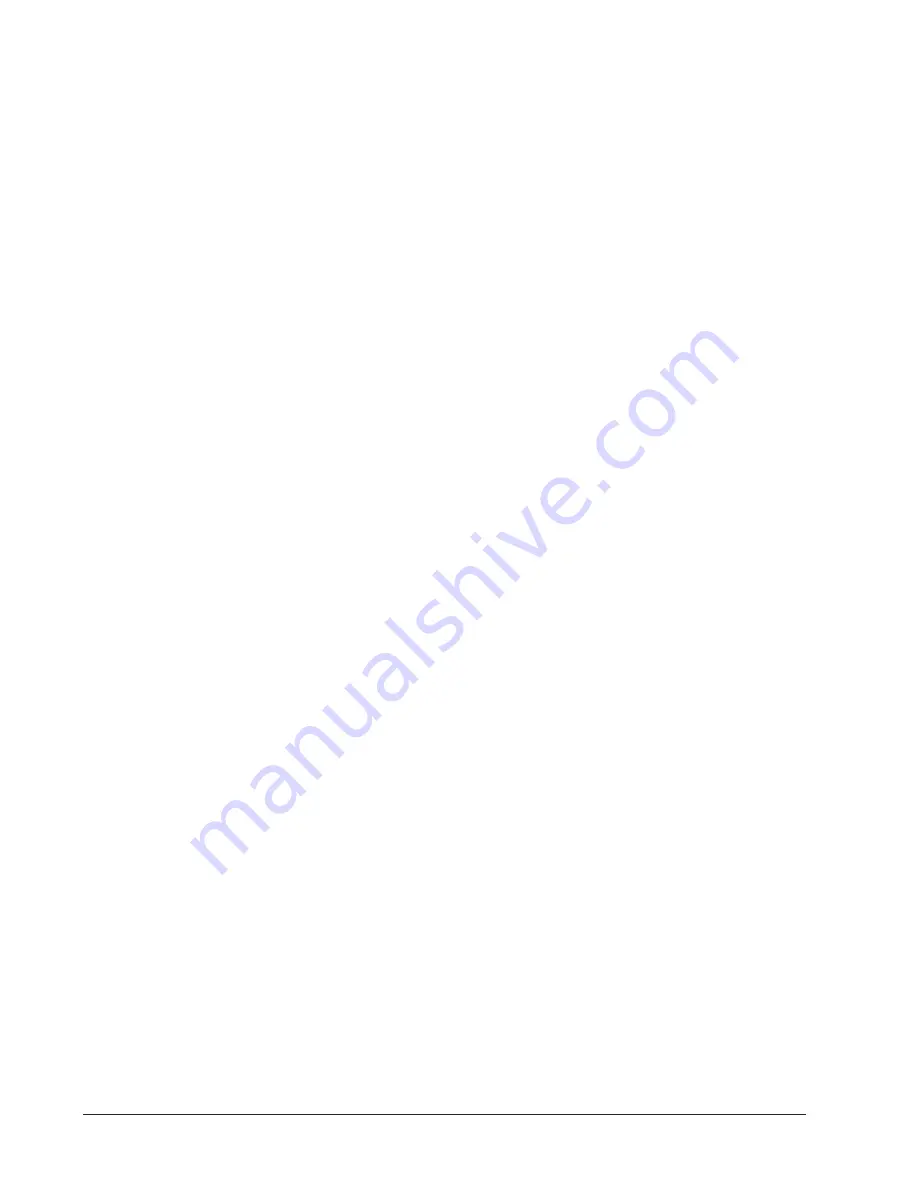
2-6
MN703
For moderate changes in the maximum speed, there will be a slight effect on the minimum speed
setting when the minimum is set to zero. There may be significant variation in the minimum speed
setting if the minimum speed is at a higher than zero setting.
Acceleration Trimpot (ACCEL)
The ACCEL Trimpot is provided to allow for a smooth start over an adjustable time period each time
the AC power is applied or the Main Speed Potentiometer is adjusted to a higher speed. The ACCEL
Trimpot is factory set to 2 seconds, which is the amount of time it will take for the motor to accelerate
from zero speed to full speed. To increase the acceleration time, rotate the ACCEL Trimpot clockwise.
To decrease the acceleration time, rotate the ACCEL Trimpot counterclockwise. The ACCEL Trimpot
range is 0.2 – 10 seconds.
Deceleration Trimpot (DECEL)
The DECEL Trimpot controls the amount of rampdown time when the Main Speed Potentiometer is
adjusted to a lower speed. The DECEL Trimpot is factory set to 2 seconds, which is the amount of
time it will take for the motor to decelerate from full speed to zero speed. To increase the deceleration
time, rotate the DECEL Trimpot clockwise. To decrease the deceleration time, rotate the DECEL Trimpot
counterclockwise. The DECEL Trimpot range is 0.2 – 10 seconds.
Current Limit Trimpot (CL)
The CL Trimpot is used to limit the maximum current (torque) to the motor. The CL also protects the
control from excessive current during startup. The CL Trimpot is factory set to 150% of the full load
current rating of the motor. To increase the current limit, rotate the CL Trimpot clockwise (do not
exceed 200% of the full load current rating of the motor (maximum clockwise position)). To decrease
the current limit, rotate the CL Trimpot counterclockwise. On cyclical loads, it may be normal for the
CL LED to momentarily flash.
(Visible only if the cover is removed.) The CL Trimpot range is 0% – 200% of the full load current
rating of the motor. Some application may require a lower value so as not to damage process material
or drive train components.
Note: For the Current Limit to operate properly, the correct Plug-In Horsepower Resistor® must be
installed for the particular motor and input voltage being used. Calibration of the CL Trimpot is
normally not required when the proper Plug-In Horsepower Resistor® is installed.
Caution: do not leave motor shaft locked for more than 2 – 3 seconds or motor damage may result.
To Recalibrate the CL Trimpot:
1. Disconnect the AC power and connect a DC ammeter in series with either motor armature lead.
If only an AC ammeter is available, connect it in series with either AC line input lead.
2. Set the Main Speed Potentiometer to approximately 30% – 50% clockwise position.
3. Set the CL Trimpot fully counterclockwise. The CL LED will illuminate red.
4. Load the motor shaft in accordance with application requirements.
Apply power and rotate the CL Trimpot clockwise until the desired current reading is observed on the
DC ammeter. Factory Current Limit setting is 150% of the full load current rating of the motor. If using
an AC ammeter connected in the AC line input, the factory Current Limit setting will read 75% of the
full load current rating of the motor. Do not exceed 200% of the full load current rating of the motor
(maximum clockwise position).
IR Compensation Trimpot (IR)
The IR Trimpot sets the amount of compensating voltage required to keep the motor speed constant
under varying loads. If the load does not vary substantially, the IR Trimpot may be set to a minimum
level (approximately 1/4 of full clockwise rotation). The IR Trimpot is factory set to provide 3 Volts of
compensation for controls with 90 Volt DC output and 6 Volts of compensation for controls with 180
Volt DC Output. To increase the amount of compensating voltage, rotate the IR Trimpot clockwise. To
decrease the amount of compensating voltage, rotate the IR Trimpot counterclockwise.
To Recalibrate the IR Trimpot:
1. Set the IR Trimpot to approximately 25% rotation.
2. Run the motor unloaded at approximately 1/3 speed and record the RPMs.
Summary of Contents for BC140
Page 1: ...6 15 Installation Operating Manual MN703 BC140 BC140 FBR DC CONTROL...
Page 4: ...ii MN703...
Page 17: ......
Page 18: ......