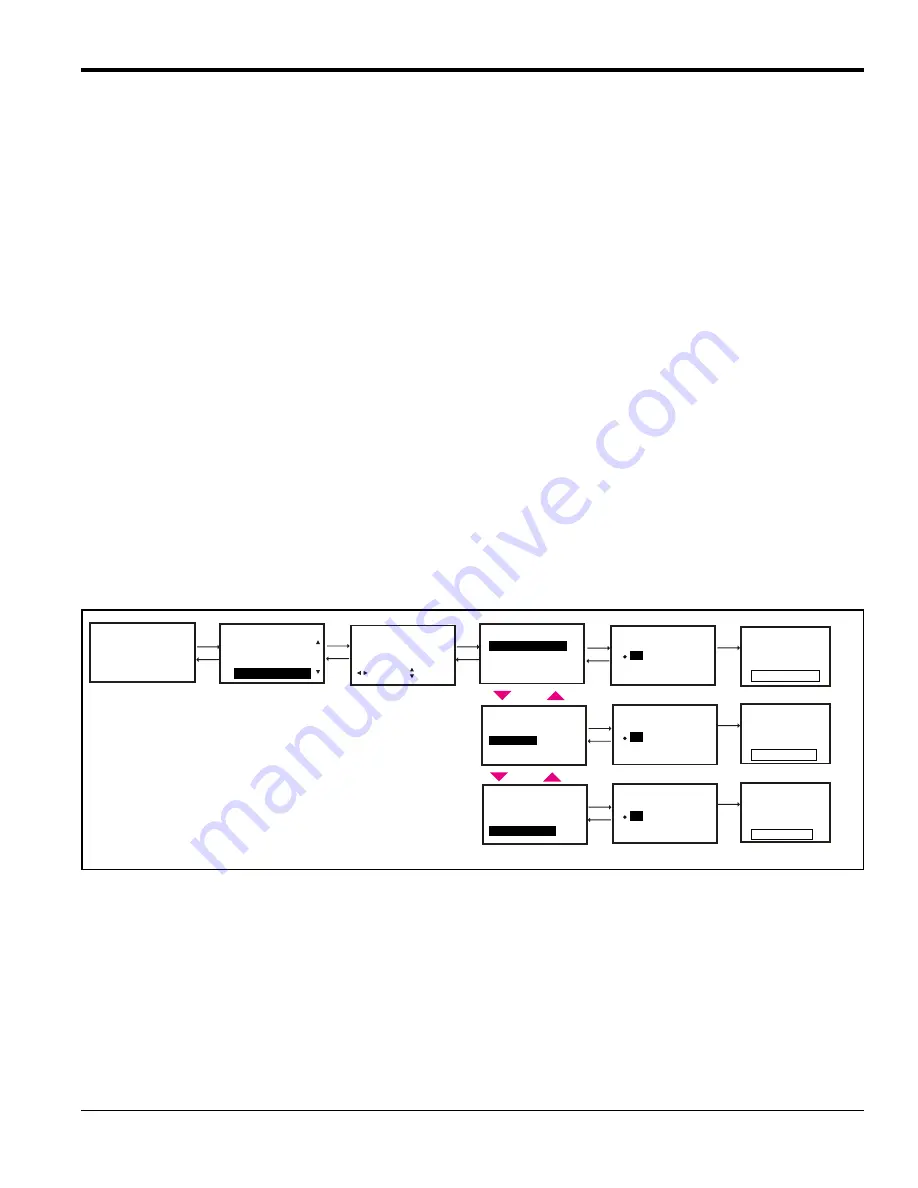
PanaFlow Z3 User’s Manual
45
Chapter 3. Programming
3.
Option I/O board
Note:
Consult the factory or BakerHughes Services before you upgrade software.
IMPORTANT:
The upgrade process may wipe out the configurations. It is important to save a site file before
beginning the upgrade process. Use USB flash drive 8GB or 16GB for upgrade. 32GB flash drive is not
supported.
3.0.1
Perform Software Upgrade
The XMT1000 software upgrade requires password entry. The Upgrade password is unique to the System serial
number of your meter. The meter will automatically be exited from Upgrade mode after 5 minutes of inactivity.
Ensure the meter keypad is in unlock mode. If the meter keypad is locked, use steps outlined in Section 3.2.1 to unlock
the keypad. Log-in into Operator access level and navigate to About Meter and note the System Serial Number. Open
the GENPASS_SW_UPGRADE application, enter the noted System Serial Number. The GENPASS_SW_UPGRADE
application will show the Upgrade Access password for your meter.
To perform Software Upgrade, do the following steps and refer Figure 39:
1.
Copy the Transmitter, Flow board or Option I/O board software into the USB flash drive and insert the USB flash
drive to the meter.
2.
In the meter HMI press
[
]
until the lock icon on the meter's Measurement View display is highlighted, and press
[ENTER]
.
3.
In the Main Menu select
[Software Upgrade]
, then press
[ENTER]
.
4.
Enter the password for your meter when prompted.
5.
Select the board you want to upgrade as outlined in the recommended sequence above.
6.
Confirm the initiation of upgrade by selecting
[Yes]
. Once confirmed the upgrade process will start. The display
indicates the steps in the process. The upgrade of each subsystem could take up to 10 minutes. At the end of the
upgrade the meter displays if the upgrade was successful or not. The meter would restart after upgrade of each
subsystem is complete. But it is recommended to power cycle the meter after successfully upgrading all sub
systems.
Figure 39: Software Upgrade
Velocity
0.000
m/s
Main Menu
Errors/Warnings
Software Upgrade
Enter Upgrade password
Software Upgrade
Flow Info
Transmittter Board
Option IO Board
Flow Board
Software Upgrade
Transmittter Board
Option IO Board
Flow Board
Software Upgrade
Transmittter Board
Option IO Board
Flow Board
No
Yes
Keypad Lockout
111111
[ ]
2
9
[ ]
ESC
MOVE
[ ]
[ ]
ENTER
MODF
9
2
9
2
9
9
2
Upgrade Transmitter SW
No
Yes
UpgradeFlow Board SW
9
2
System Upgrade Window
Upgrading Please wait..
Don’t touch any key!
Upgrading...
Upgrading...
Upgrading...
9
System Upgrade Window
Upgrading Please wait..
Don’t touch any key!
9
System Upgrade Window
Upgrading Please wait..
Don’t touch any key!
9
2
9
No
Yes
Upgrade Opt I/O Board SW
2
Summary of Contents for Panametrics PanaFlow Z3
Page 1: ...Flow 910 311 Rev C April 2019 Panametrics com PanaFlow Z3 User s Manual...
Page 2: ......
Page 4: ...ii no content intended for this page...
Page 8: ...Contents vi PanaFlow Z3 User s Manual...
Page 12: ...Preface x PanaFlow Z3 User s Manual no content intended for this page...
Page 21: ...PanaFlow Z3 User s Manual 9 Chapter 2 Installation Figure 8 Lifting the PanaFlow Z3 System...
Page 25: ...PanaFlow Z3 User s Manual 13 Chapter 2 Installation Figure 12 Remote Mount Wiring Diagram...
Page 26: ...Chapter 2 Installation 14 PanaFlow Z3 User s Manual no content intended for this page...
Page 58: ...Chapter 3 Programming 46 PanaFlow Z3 User s Manual no content intended for this page...
Page 86: ...Appendix A Specifications and Model Configurations 74 PanaFlow Z3 User s Manual...
Page 104: ...Appendix B Data Records 92 PanaFlow Z3 User s Manual no content intended for this page...
Page 108: ...Appendix D CE Mark Compliance 96 PanaFlow Z3 User s Manual no content intended for this page...
Page 110: ...Warranty 98 PanaFlow Z3 User s Manual no content intended for this page...
Page 116: ......
Page 117: ......