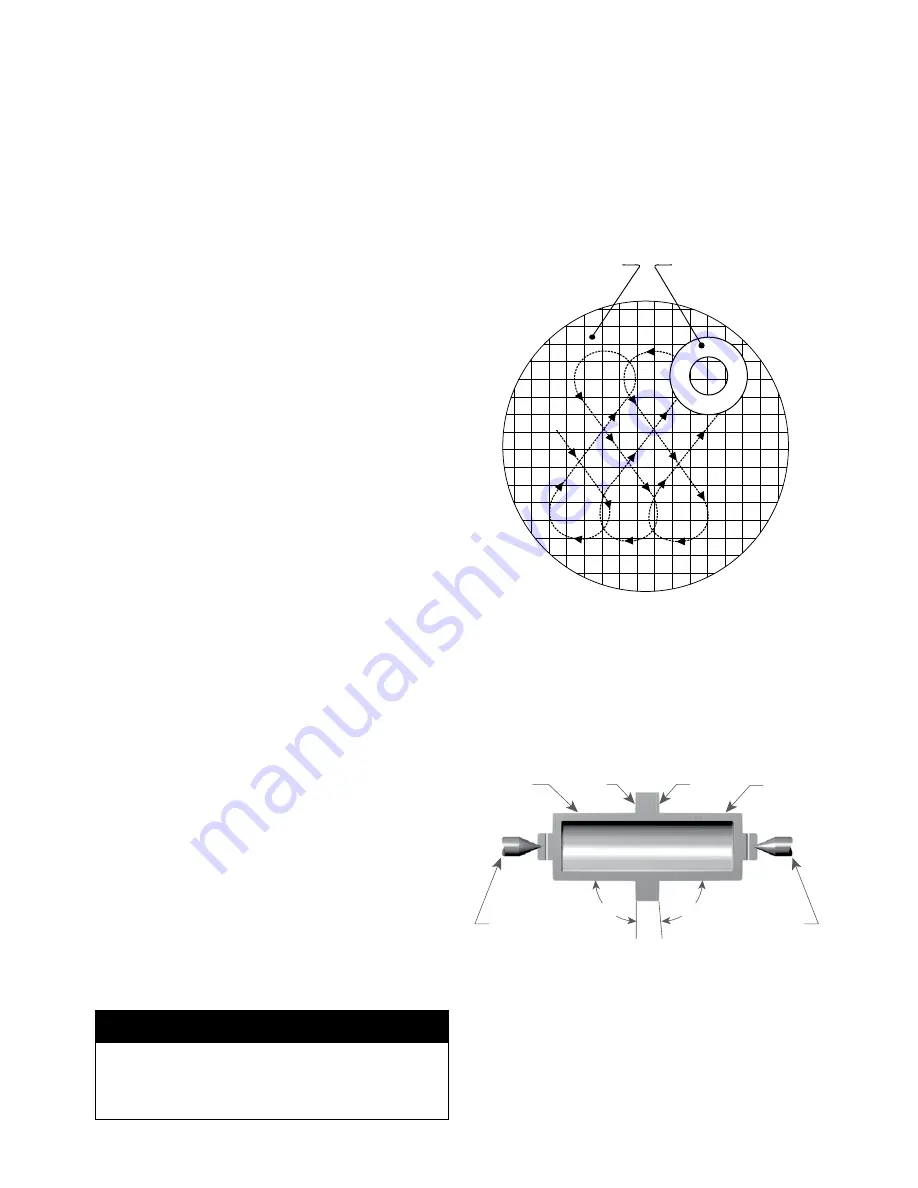
E. Lapping Disc Seats
Use a ring lap or lapping plate to lap the disc in a
circular motion, applying uniform pressure and slowly
rotating the disc or lap.
• Apply 1000 lapping compound (see Table 18 in
Lapping Tools Section XXIII.C. Lap disc to a
polish finish.
• Remove lapping compound completely from
Disc and Disc Holder.
F. Precautions and Hints for
Lapping Seats
To ensure a quality lapping process, observe the
following precautions and guidelines:
Keep work materials clean. Always use a fresh lap.
If signs of wear (out of flatness) are evident, recondition
the lap.
Apply a very thin layer of lapping compound to the lap to
prevent rounding off the edges of the seat.
Keep the lap squarely on the flat surface, and avoid
rocking the lap, which causes rounding of the seat.
When lapping, keep a firm grip on the lapped part to
prevent dropping it and damaging the seat.
Lap in a circular motion while applying a uniform
pressure. Slowly rotate the lap to evenly distribute the
lapping compound. Wipe off the old compound and
replace it with new compound frequently. Apply more
pressure to speed the cutting action of the compound.
To check the seating surfaces, remove all compound
from the seat and the lap. Then, shine the seat with the
same lap using the lapping method as described above.
Low sections on the seating surface show up as shadow
in contrast to the shiny portion. If shadows are present,
further lapping is necessary. Only laps known to be
flat can be used. It should take only a few minutes to
remove the shadows.
When lapping is complete, any lines appearing as cross-
scratches can be removed by rotating the lap on its axis
(which has been wiped clean of compound) on the seat.
Thoroughly clean the lapped seat using lint free cloth
and a cleansing fluid.
ATTENTION!
Before assembly, grind the contact surfaces of the
nozzle and O-Ring retainer to provide metal-to-metal
seat tightness in the event of O-Ring failure.
G. Reconditioning of Laps
Ring laps are reconditioned by lapping them on a flat
lapping plate in a figure-eight motion (Figure 30). To
ensure the best results, recondition the ring laps after
each use. Use an optical flat to check the quality of
the lap.
Nozzle laps must be re-machined to recondition the
lapping surfaces. Place the nozzle lap in a lathe between
centers (Figure 31). The surfaces marked
A and B must be running concentric.
Lapping Plate
Ring Lap
Figure 30: Lapping Pattern
Lathe Center
Lathe Center
A
C
D
B
85°
90°
Figure 31: Nozzle Lap in a Lathe
XIV. Maintenance Instructions (Contd.)
Consolidated 2900 Series POSRV Maintenance Manual
|
39
© 2018 Baker Hughes, a GE company. All Rights Reserved.