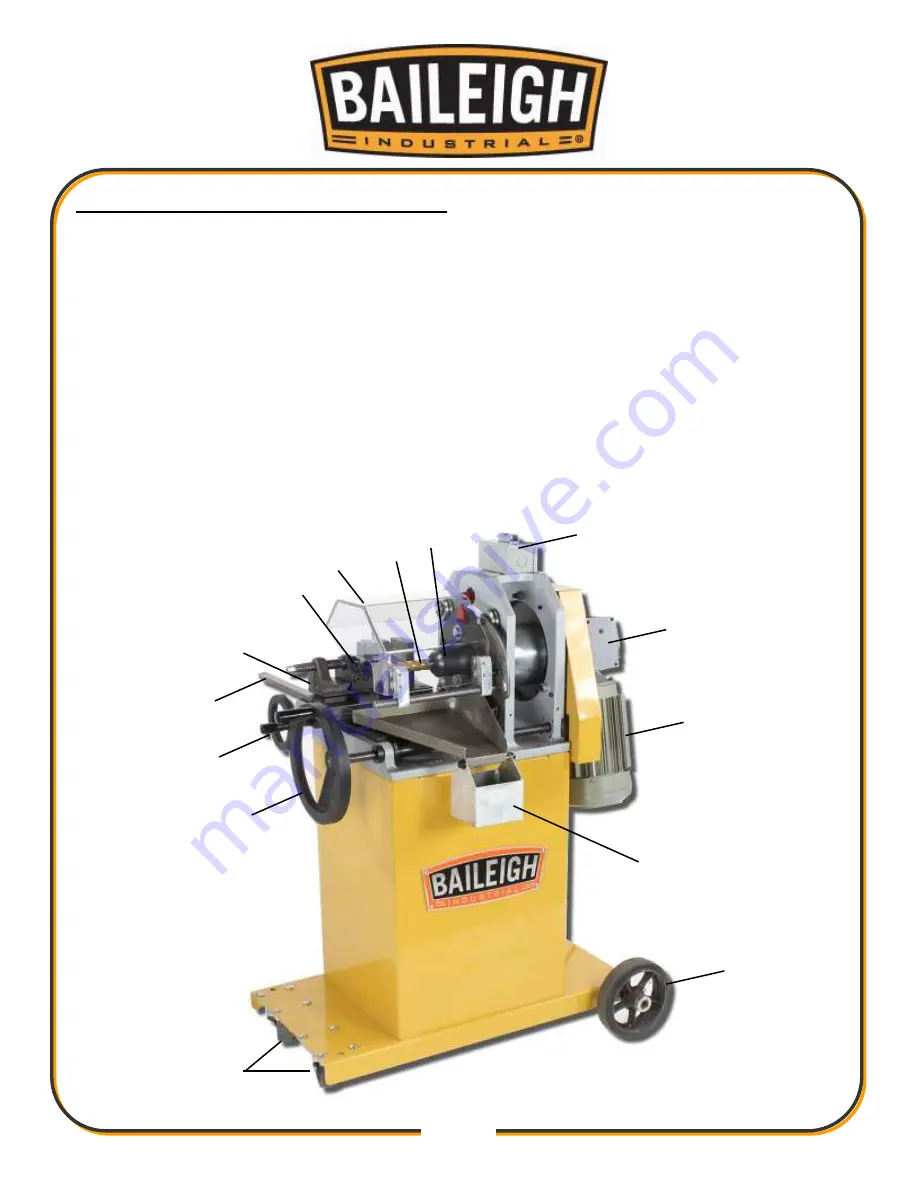
15
15
GETTING TO KNOW YOUR MACHINE
You have made a practical choice in purchasing a Model TN-800 Eccentric Cut Notching
Machine. It has been carefully built of high quality materials and designed to give many
years of efficient service. The simplicity of design and minimum effort required to operate
the machine contributes towards meeting schedules and producing greater profits.
The TN-800 is an electric powered end-mill notching machine specially designed to notch a
variety of materials using only one end mill. The Patented Eccentric Cut feature, allows the
user to feed an end mill cutter through an adjustable eccentric path. Creating a perfect weld
joint when mating two or more pieces of tubing together.
The TN-800 Notching Machine you have purchased is built of solid steel and high quality
components, ensuring maximum rigidity and long life.
A
B
C
D
E
F
G
H
I
J
K
L
M
N
Summary of Contents for TN-800
Page 28: ...26 26 ELECTRICAL SCHEMATIC...
Page 30: ...28 28 PARTS DIAGRAM Base Assembly...
Page 31: ...29 29 Spindle Assembly...
Page 32: ...30 30 Forward Riser Assembly...
Page 33: ...31 31 Motor and Gearbox Assembly...
Page 34: ...32 32 Rear Riser Assembly...
Page 35: ...33 33 Crank Shaft Assembly...
Page 36: ...34 34 Vise Assembly...
Page 37: ...35 35 Slide Base Assembly...
Page 42: ...40 40 NOTES...
Page 43: ...41 41 NOTES...