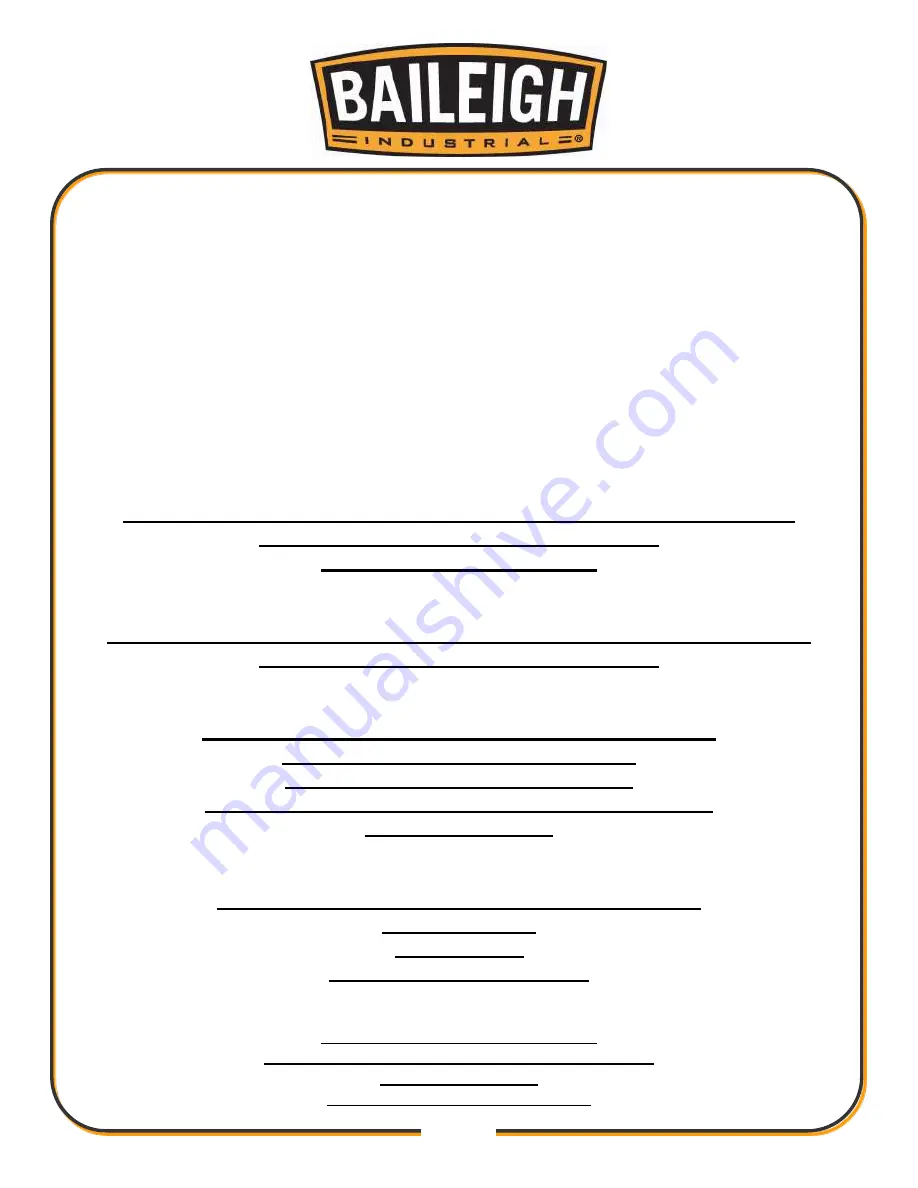
53
53
BAILEIGH
INDUSTRIAL,
INC.
1625
D
UFEK
D
RIVE
M
ANITOWOC
,
WI
54220
P
HONE
:
920.
684.
4990
F
AX
:
920.
684.
3944
BAILEIGH
INDUSTRIAL,
INC.
1455
S.
C
AMPUS
A
VENUE
O
NTARIO
,
CA
91761
P
HONE
:
920.
684.
4990
F
AX
:
920.
684.
3944
BAILEIGH
INDUSTRIAL
LTD.
U
NIT
1
F
ULLWOOD
C
LOSE
A
LDERMANS
G
REEN
I
NDUSTRIAL
E
STATE
C
OVENTRY
,
CV2
2SS
U
NITED
K
INGDOM
P
HONE
:
+44
(0)24
7661
9267
F
AX
:
+44
(0)24
7661
9276
BAILEIGH
INDUSTRIAL
G
MB
H
H
OFENER
S
TRAßE
64
70736
F
ELLBACH
D
EUTCHSLAND
WWW
.
BAILEIGHINDUSTRIAL
.
DE
BAILEIGH INDUSTRIAL Pty. Ltd.
P.O Box 1573, 126 Melrose Drive Tullamarine,
VIC 3043 Australia
www.baileighindustrial.com.au
Summary of Contents for IP-2511-HD
Page 39: ...36 36 ELECTRICAL SCHEMATIC...
Page 40: ...37 37...
Page 41: ...38 38...
Page 42: ...39 39...
Page 43: ...40 40 Electrical Cabinet Layout...
Page 44: ...41 41 CUTTERHEAD PARTS DIAGRAM...
Page 46: ...43 43 TABLE PARTS DIAGRAM...
Page 48: ...45 45 TABLE ROLLER PARTS DIAGRAM...
Page 50: ...47 47 INFEED PARTS DIAGRAM...
Page 52: ...49 49 STAND PARTS DIAGRAM...
Page 54: ...51 51 NOTES...
Page 55: ...52 52 NOTES...