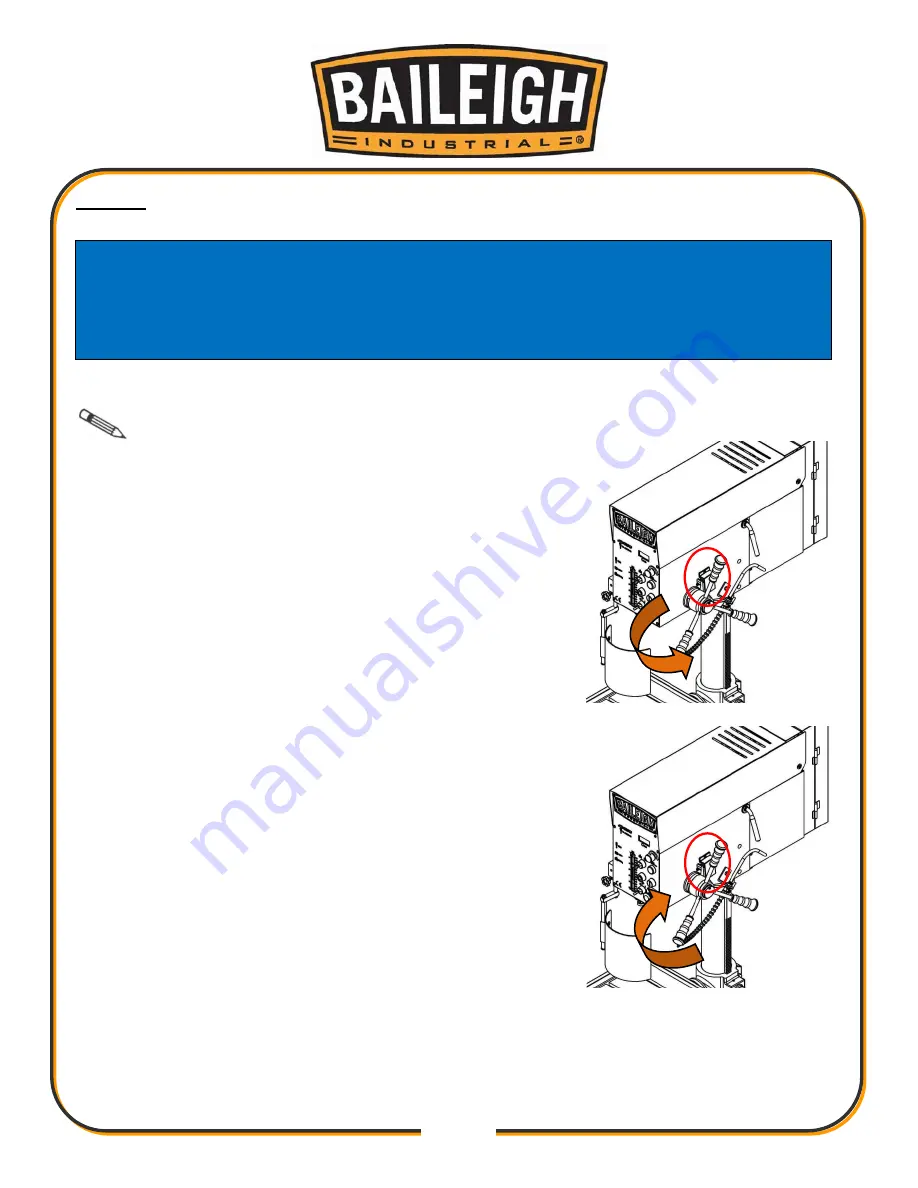
29
29
Tapping
In general, speeds for tapping require low speeds.
Important: Chamfer the holes before tapping. A
tapping rate of eight times per minute or less is
recommended.
1. Set the drill press up similar to a drilling operation. Setting
depth and securing material.
2. Install the desired tap for the operation.
3. Turn the selector switch on the electrical cabinet to tapping
mode.
4. Start the machine by pushing button.
5. Turn on the coolant selector switch.
6. Begin tapping. Use the down-feed handles to enter the
tapping bit into the piece part. Release hold of the handles.
The bit will automatically reverse upon reaching the depth
stop.
7. If needed, push back on the feed handle to reverse the tap
before the travel reaches the travel stop point.
NOTICE: This is a conventional drill, not a special purpose machine, therefore frequent
tapping jobs will wear the motor and gears.
Temperature of motor will be increased quickly
when tapping due to low motor RPM and frequently motor direction be changed. Therefore,
rapid and continuous tapping shall be avoided. Maximum of eight times per minutes of
tapping is recommended. The machine shall be stopped for cooling if the motor is too hot.
Summary of Contents for DP-1400VS
Page 13: ...10 10...
Page 17: ...14 14 GETTING TO KNOW YOUR MACHINE N C E M G J O A B K I H L F P Q R S D...
Page 38: ...35 35 BASE AND TABLE PARTS DIAGRAM...
Page 39: ...36 36 HEAD CONTROL PARTS DIAGRAM...
Page 43: ...40 40 ELECTRICAL DIAGRAM...
Page 46: ...43 43 NOTES...
Page 47: ...44 44 NOTES...