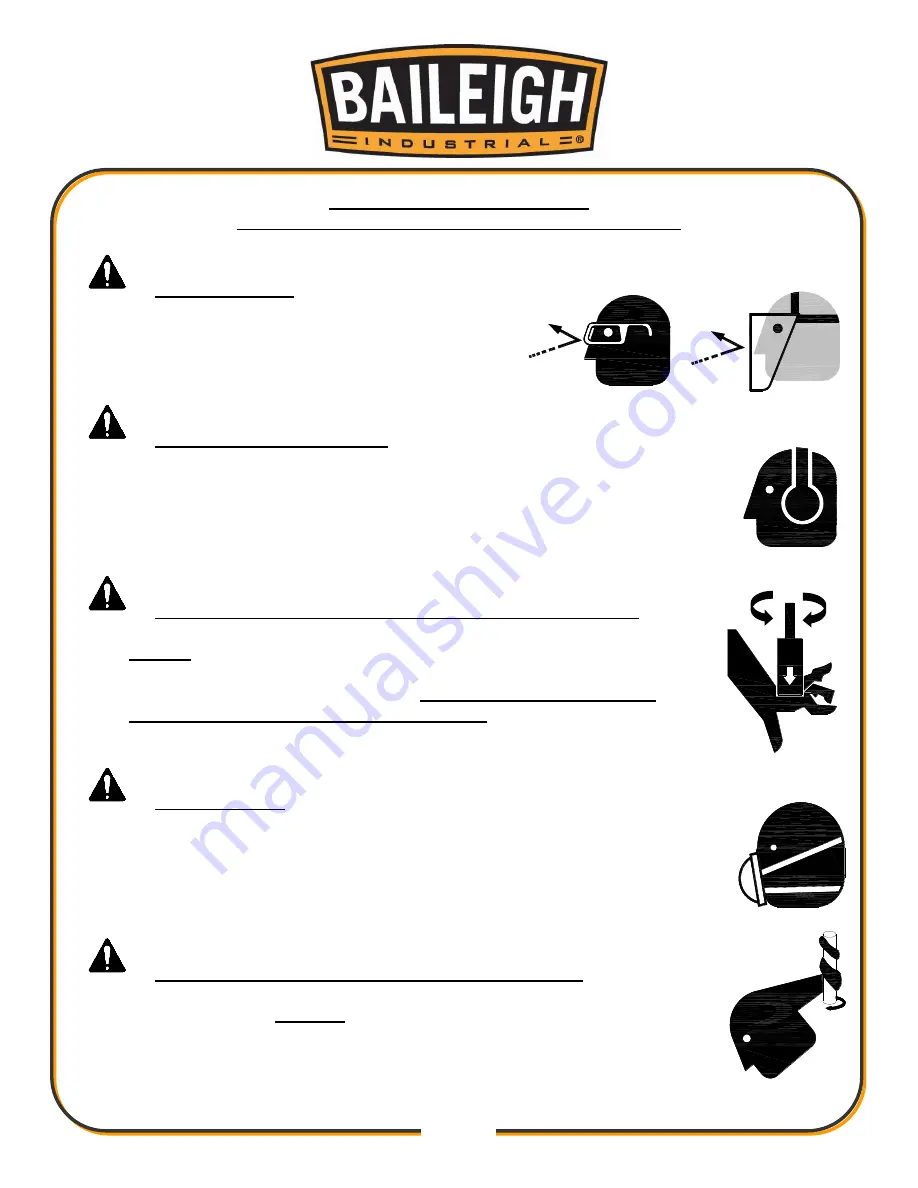
5
5
SAVE THESE INSTRUCTIONS.
Refer to them often and use them to instruct others.
PROTECT EYES
Wear safety glasses or suitable eye protection
when working on or around machinery.
PROTECT AGAINST NOISE
Prolonged exposure to loud noise can cause impairment or loss of
hearing. Wear suitable hearing protective devices such as earmuffs or
earplugs to protect against objectionable or uncomfortable loud noises.
BEWARE OF PIERCING POINTS AND CUTTING HAZARD
NEVER
place hands, fingers, or any part of your body on or near
rotating tooling. This tooling can be extremely dangerous if you do
not follow proper safety procedures.
Keep hand at least 6 inches
(150mm) from the tooling while operating.
DUST HAZARD
Wear appropriate dust mask. Dust created while using machinery can
cause cancer, birth defects, and long-term respiratory damage. Be aware
of the dust hazards associated with all types of materials.
ENTANGLEMENT HAZARD
– ROTATING SPINDLE
Contain long hair,
DO NOT
wear jewelry or loose-fitting clothing.
Summary of Contents for DP-1375VS-110
Page 18: ...16 16 OVERALL DIMENSIONS 71 37 1813 26 50 673 38 30 973...
Page 19: ...17 17 GETTING TO KNOW YOUR MACHINE F L Q M J H E N I O D P A A R C S K G B...
Page 33: ...31 31 HEAD and CHUCK GUARD PARTS DIAGRAM...
Page 37: ...35 35 UPPER HEAD PARTS DIAGRAM...
Page 40: ...38 38 COLUMN TABLE BASE PARTS DIAGRAM...
Page 43: ...41 41 ELECTRICAL COMPONENTS KM1 KM2 F3 F4 KR RX F1 F2...
Page 45: ...43 43 ELECTRICAL SCHEMATIC...