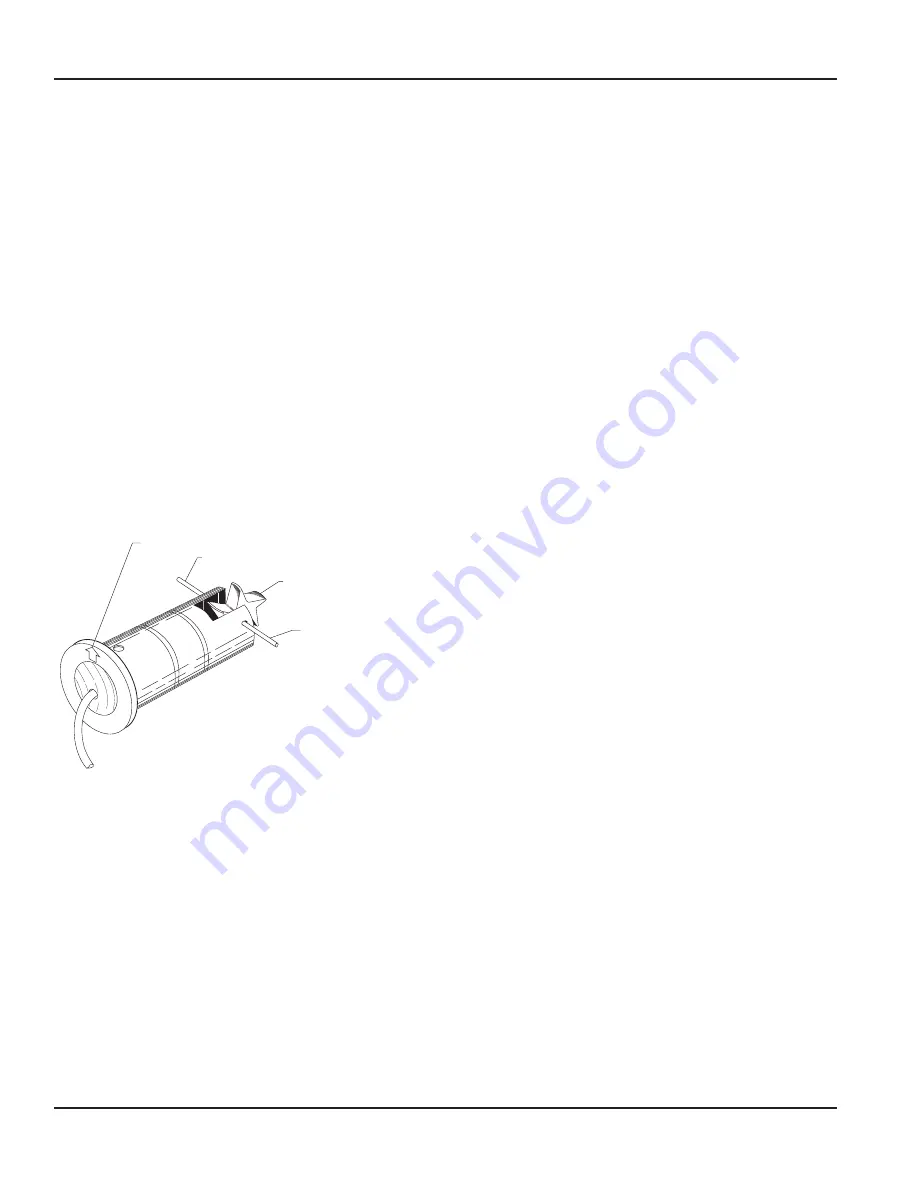
Series 200 Flow Sensors
IMPELLER ASSEMBLY AND SHAFT
REPLACEMENT
If you are replacing an existing Badger Meter sensor and
have already calibrated your flow monitor/transmitter,
no calibration changes are necessary. For installation of
a new flow monitor or for relocation of a sensor in a new
pipe size, please refer to the calibration instructions in
flow monitor manual.
1. Depressurize pipe from which sensor is to be
removed. If the sensor is one of the Series 225/IR225
or 226/IR226, consult the installation section on hot
tap sensors.
NEVER disturb the securing lock nuts with pipe under
pressure without hot tap insertion tool Model HTT
installed.
2. Remove the three lock nuts that secure the
positioning collar to the threaded rods of metal
sensor.
NOTE:
Before removing lock nuts, record the dimension
from top of 2 inch NPT adapter to the bottom of the
positioning collar. This dimension will be required later to
reinstall.
NOTE DIRECTION OF ARROW
USE PLIERS HERE
NOTE DIRECTION OF
IMPELLER
USE METAL PIN TO
REMOVE CERAMIC SHAFT
Figure 4: Impeller Assembly and Shaft Replacement
3. Remove the sensor from the hex adapter or the tee.
4. Note the impeller blade orientation relative to flow
arrows and the alignment hole in metal sensors beside
one of the sighting holes. In order to maintain proper
calibration, the impeller will have to be reinstalled in
the same manner with the impeller blades pointing
toward the small alignment hole, and into the flow
direction as indicated by the flow arrows.
5. To remove the old impeller blade assembly, push the
old shaft out of the sleeve with the new shaft (or small
diameter rod) just far enough to grab the end with a
pair of pliers and pull the shaft completely out. The
impeller assembly will now be free and will drop out.
6. Inspect the shaft and bearings for wear, and replace
as necessary.
7. Refer to figure 4. To reinstall, position the impeller in
the cavity oriented as in step 4 so that the impeller
blades point into the flow direction and toward
the small alignment hole located beside one of the
sighting holes on metal sensors.
8. Carefully push the shaft through the sleeve and
impeller taking care not to damage the bearings.
Make sure that the shaft is inserted far enough so
that it clears the sleeve on each side of the impeller
housing.
NOTE:
If shaft is not carefully installed, the bearing can be
deformed preventing free rotation.
9. Inspect the O-rings for damage and replace as
necessary. Clean the O-rings and the sleeve and
relubricate with silicone grease from the packet
provided or some other acceptable lubricant.
10. Install the sensor into the 2 inch NPT adapter or tee
so that alignment hole is facing upstream and flow
arrows point in the direction of the actual flow. Since
the positioning collar was not loosened during this
operation, the studs should all line up perfectly when
the sighting holes are parallel to pipe. If this has been
accidentally loosened, please refer to the installation
instructions for the alignment of the flow sensor unit.
11. Install and tighten the nuts.
12. For metal sensors, double check that the distance
from the top of the 2 inch NPT adapter to the bottom
of the positioning collar equals the dimension as
measured in step 2, and holes in sleeve sight exactly
down the pipe, the arrows point in direction of flow
and alignment holes located beside one sighting
hole is pointing towards the source. If not, refer to
installation
section in this manual.
13. This completes the replacement procedure. The
system may now be repressurized and tested.
TROUBLESHOOTING
1. If the voltage at the sensor input is less than 7 VDC
in a no flow situation, disconnect the sensor from
the barrier strip and measure the voltage at the
sensor input terminals of the barrier strip again. It
should be between 8 VDC and 20 VDC. If the voltage
at the sensor input is still below 7 VDC or 3 VDC,
the problem may be with the monitor (hardware or
programming).
Page 12
August 2012