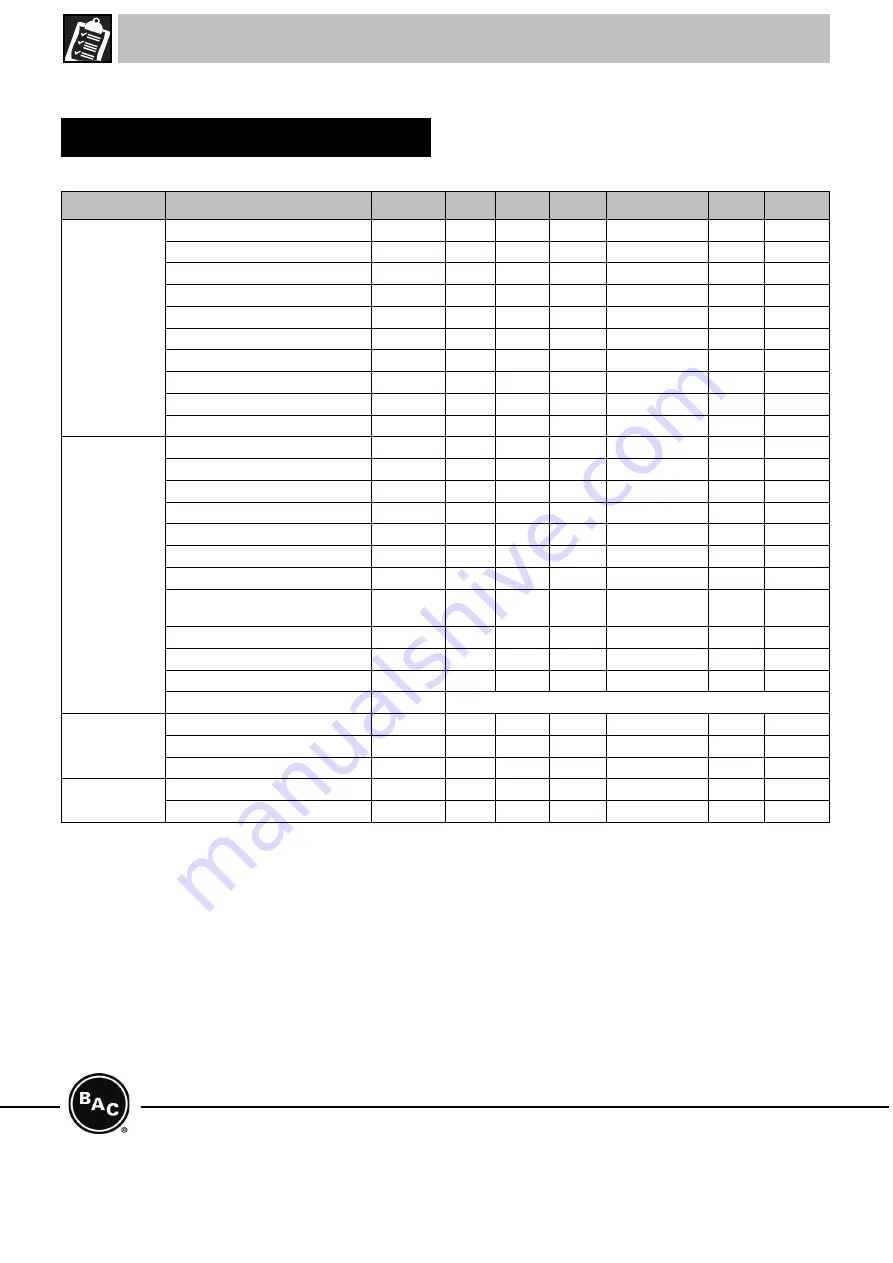
RECOMMENDED MAINTENANCE AND MONITORING PROGRAMME
www.BaltimoreAircoil.com
[email protected]
Baltimore Aircoil Company SA
(Pty) Ltd.
Portland Road, Phillipi
Cape Town, South Africa
©
Baltimore Aircoil Company SA (Pty) Ltd
Model: ...........................................................................................
Serial number: .................................................................................
* only for motors with grease fittings
** depends on applied code of practice
Notes:
1. Water Treatment and auxiliary equipment integrated in the cooling system may require additions to the table above. Contact suppliers for
recommended actions and their required frequency.
2. Recommended service intervals are for typical installations. Different environmental conditions may dictate more frequent servicing.
3. For units with Belt Drive, tension on new belts must be readjusted after the first 24 hours of operation and monthly thereafter.
Schedule
Type of Action
Action
Start-Up
Weekly Monthly Quarterly Every Six Months Annually Shutdown
Checks and
Adjustments
Cold Water Basin and Strainers
X
X
Operating level and make-up
X
X
Blow down
X
X
Sump heater package
X
X
Belt tension
X
X
Drive alignment
X
X
Locking Collar
X
X
Rotation of fan(s) and pump(s)
X
Motor voltage and current
X
X
Unusual noise and/or vibration
X
X
Inspections and
Monitoring
General condition
X
X
Heat transfer section
X
X
Finned discharge coil (optional)
X
X
Drift eliminators
X
X
Water distribution
X
X
Fan Shaft
X
X
Fan Motor
X
X
Electric Water Level Control Package
(optional)
X
X
TAB test (dip slides)
X
X
Circulating water quality
X
X
System overview
X
X
Record keeping
as per event
Lubrication
Fan shaft bearings
X
X
Motor bearings *
X
X
Adjustable motor base
X
X
Cleaning
procedures
Mechanical cleaning
X
X
Disinfection **
(X)
(X)
(X)
Table 4: Recommended Maintenance & Monitoring Schedule