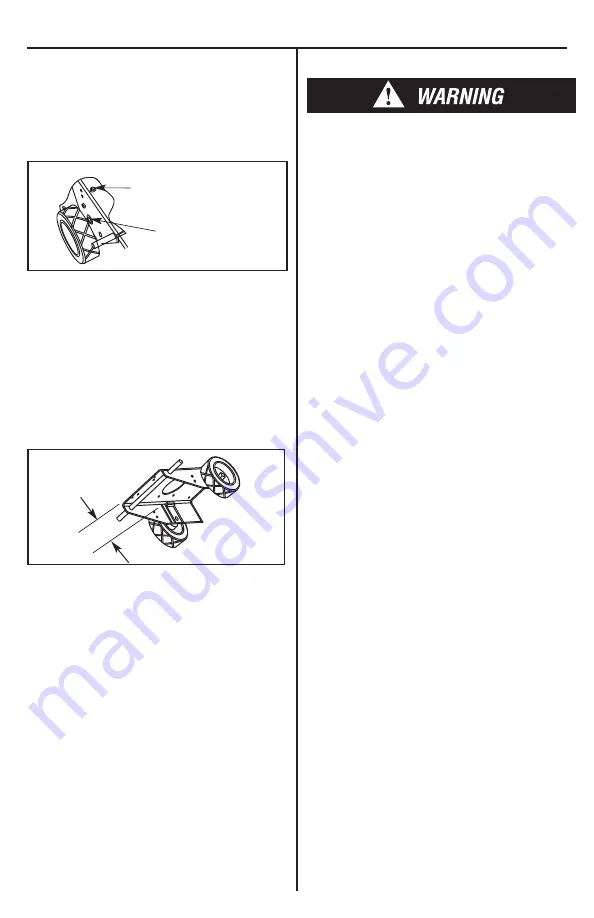
ULTRAGRIND PG. 7
4. Transport wheel can be turned so wheel is
in the up position & installed into bracket
for storage; make sure the locking pin is
securely engaged. The transport wheel may
also be stored separate from the machine.
d. Wheel adjustment
Turn clockwise to lower
Turn counter-clockwise
to raise
Loosen 1/2-13 bolt
Wheel adjustment must be made to both wheels
on level floor.
1. Loosen 1/2-13 x 1 1/4” bolt
2. Loosen 1/2-13 jam nut just above axle bracket
3. Adjust machine height by turning the
1/2-13 x 5” bolt counter clockwise to raise
machine or clockwise to lower machine
4. Tighten 1/2-13 jam nut
5. Tighten 1/2-13 x 1 1/4” bolt
e. Rear Wheel setting
GAP
Gap factory setting is 2”. Set gap as shown in
diagram.
f. installing the fuel Cylinder
1. Take UltraGrind to well ventilated area
2. Check cylinder for overfill
3. Place cylinder on the machine in tank
holding area and secure the safety strap
4. Connect fuel cylinder to the machine,
tighten hand tight. Do not use a wrench or
pliers or cross thread
5. Open the service valve slowly, be alert for the
odor of propane which may indicate a leak
6. To remove the cylinder, reverse the procedure
G. Before operating the UltraGrind
• Check oil level
• Check carburetor air filter
• Check diamonds and diamond plates
• Adjust handle height
• Install fuel cylinder in a well ventilated area
H. Before you start the engine
do not allow machine to come into contact with
loose tiles or other obstructions on the floor.
the abrasives will be turning at approximately
650 Rpm. if objects are hit, they could become
dangerous projectiles!
• Extend the handle and tilt machine back until
handle rests on floor.
• Install diamonds and remove transport wheel.
• Bring machine back to operating position.
• Fill water tank if wet grinding.
i. preparing to start the engine
1. First - check fuel cylinder for overfill and
install cylinder onto machine.
2. Place machine on level surface and check
for correct oil level.
3. Attach lanyard kill switch clip to the operator.
The lanyard kill switch is a safety switch used
if the operator would fall or lose control of
the machine; the lanyard will pull away from
the switch and kill the engine. The lanyard
must be securely fastened to the operator
with the attached clip fastener. If the lanyard
should become disengaged from the switch,
it can simply be reattached to the switch
and engine can be restarted. The lanyard
kill switch, when activated, will ground the
ignition coils, resulting in no spark to the
spark plugs, stopping the engine. If the
lanyard should become disengaged from the
switch and the machine is no longer going to
be used, the tank valve must be closed and
the ignition key turned to the off position.
J. transporting the machine
1. The tank should be securely fastened.
2. The tank valve must be closed.
staRtinG tHe enGine
1. Open propane (LPG) tank valve (counter
clockwise).
2. Turn the key to start position and move
throttle towards fast position.
3. If engine does not start, release the key,
then try again.
4. Equipment is supplied with a centrifugal
clutch. When engine RPM is lower than 1800
RPM clutch will disengage; drivers will stop.