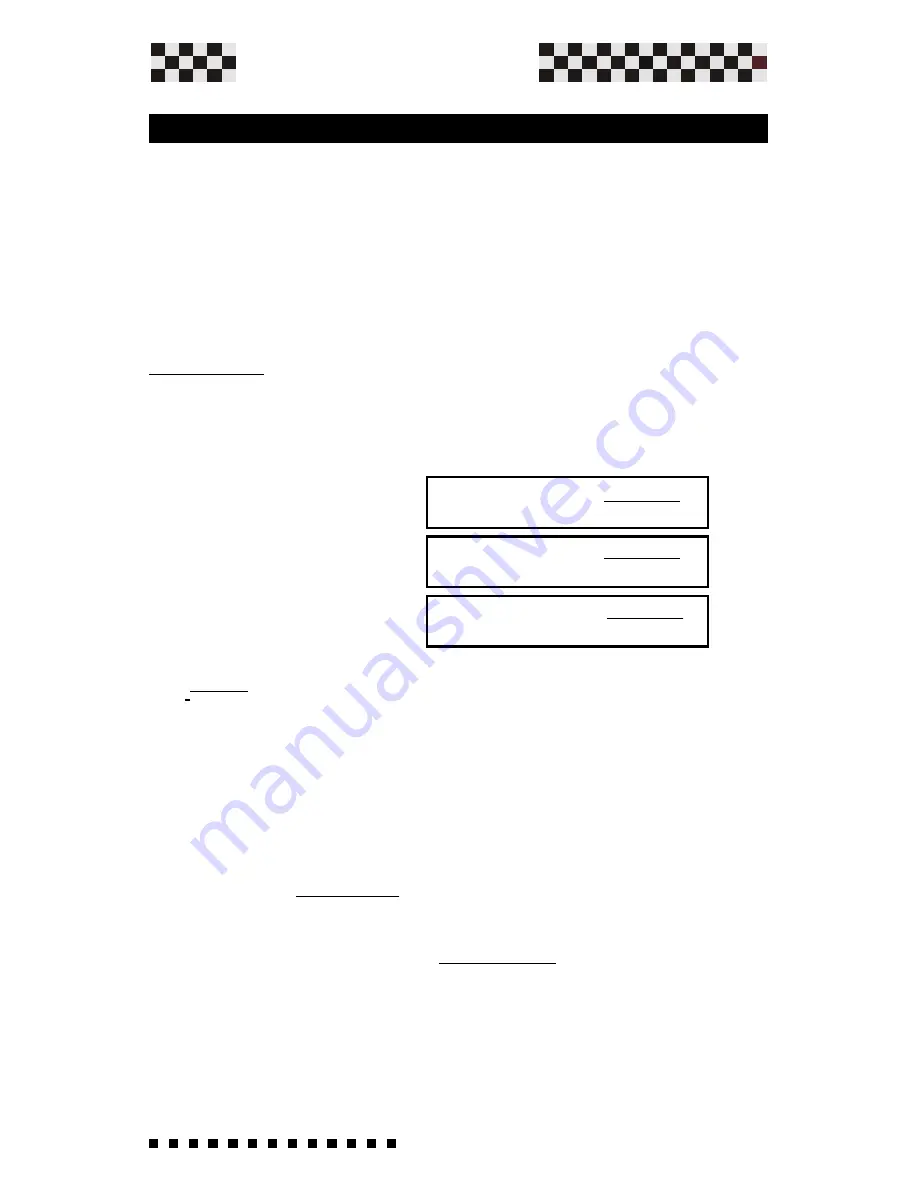
51
Service Manual
Plus
MICROSPEED
RA(k ohm) = 166 x Vref
E - 1,4 Vref
RA(k ohm) = 159 x Vref
E - 3,3 Vref
RA(k ohm) = 158 x Vref
E - 5 Vref
Adjustments
5.4 Speed adjustment with Armature feedback
Armature feedback mode may be used as speed feedback
when a tachogenerator is not fitted to the motor.
Speed control is then less precise(the regulation range is 1/
20, and below this value the torque is reduced).
This funciton will be enabled by solder bridge
S7 Closed, S12
open,
and mounting in the socket
RA
and
RCA
resistors.
RA resistor
It will be mounted on the personalization zone to
adapt the system to the voltage motor costant.
To calculate it use this equation:
RA(kohm) = 166 x 10 = 36 Kohm
60 - 1,4 x10
E = 3000 x 20 = 60
1000
WHERE:
E = n x Ke
1000
Ke= Servomotor BEMF at 1000 rpm
Vref= Max voltage reference.
n= max speed express in rpm.
Use the nearest commercial value, 33 Kohm.
Example:
Servom
otor with
Ke
=20
n
=3000 RPM
Vref
=10 For MCS
Plus 60.
MCS PLUS 60
MCS PLUS 140
MCS PLUS 200
CONTINUE