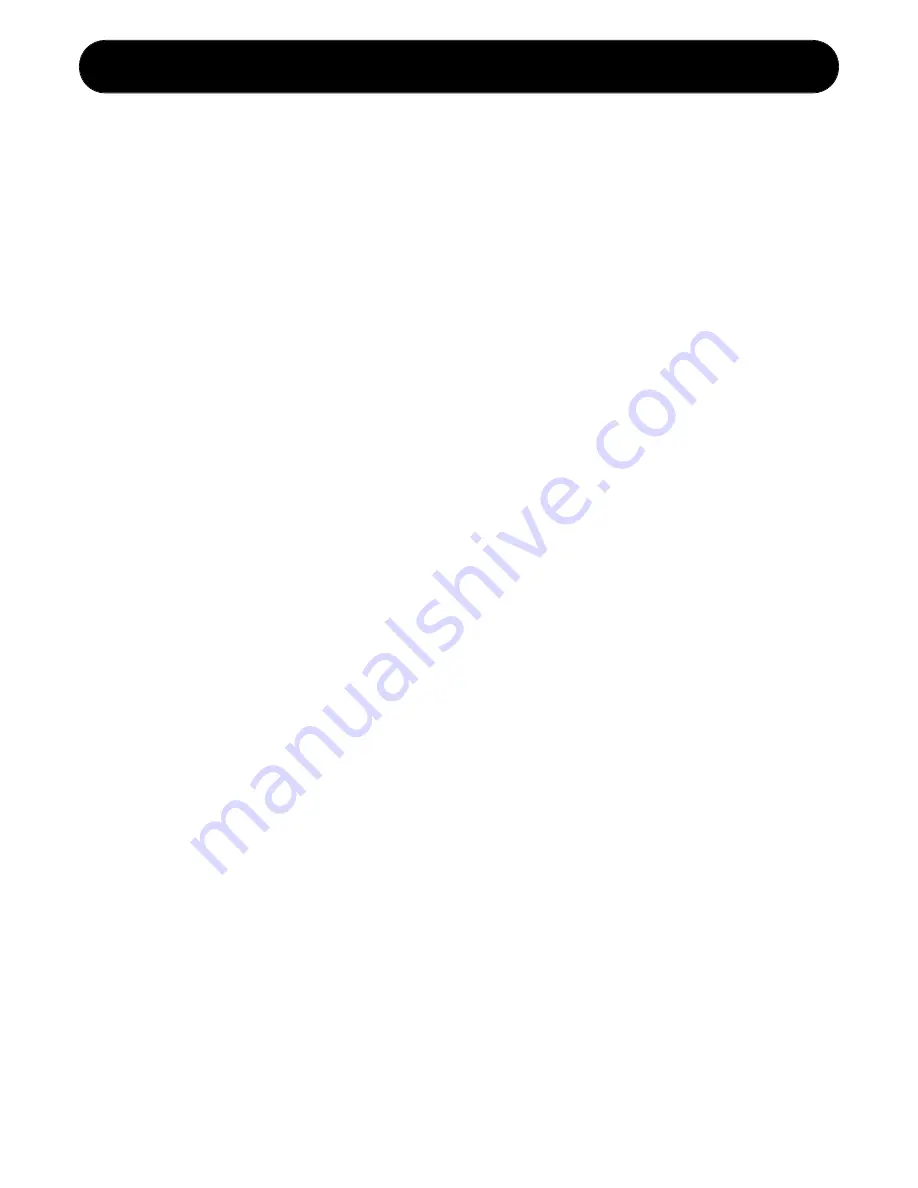
Basic Safety for Machine Tools...
KNOW YOUR MACHINE TOOL
Read and understand the owner's manual and labels affixed to the tool. Learn its application and limitations as well
as specific potential hazards peculiar to the tool.
KEEP GUARDS IN PLACE
Keep all guards in place. They are there for your protection and do not interfere with the correct operation of your
machine.
REMOVE ADJUSTING KEYS AND WRENCHES
Form the habit of checking to see that keys and adjusting wrenches are removed from the machine
before turning it on.
KEEP WORK AREA CLEAN
Cluttered areas and benches invite accidents. Floors must not be slippery due to liquids or dust. Make sure you
clean up any waste materials on completion of work.
AVOID DANGEROUS ENVIRONMENTS
Do not use power tools in damp or wet locations or expose them to rain. Keep work area well lit. Provide adequate
space surrounding the work area.
KEEP CHILDREN AWAY FROM WORK AREA UNLESS UNDER CLOSE SUPERVISION
All visitors should be kept a safe distance from work area. Children are naturally curious; therefore ensure they are
closely supervised when they are near the work area.
MAKE WORKSHOP TAMPER PROOF
Many machines have lockable switches that can be secured with a small padlock or have a removable key. Please
make use of them to prevent unauthorised operation of your machines.
DO NOT FORCE TOOL
It will do the job better and safer at the rate for which it was designed. Develop a patient approach to the work, you
will get better results in the finished product.
WEAR PROPER CLOTHING
Do not wear loose clothing, gloves, neckties or jewellery that can catch in moving parts of machinery. Non-slip
footwear with steel toecaps is recommended. Wear protective hair covering to contain long hair. Roll up long sleeves
to above the elbow.
SECURE WORK
Where applicable use clamps or a vice to hold work. This leaves both hands free to operate the tool correctly and
thus produces better results.
DIRECTION OF FEED
Feed work into a blade or cutter against the direction of rotation of the blade or cutter only. This will reduce the
danger of kick back which is a serious hazard. Similarly, when using a lathe, feed the cutting edge of the tool against
the direction of rotation!
USE SAFETY GOGGLES AND FACE PROTECTION
Wear safety goggles (complying to relevant standards) at all times. Normal spectacles only have impact resistant
lenses and are NOT sufficient. Also use face or dust masks if the cutting operation is dusty (connection of machine
to a dust extractor is preferred). Always wear ear defenders for cutting, sawing, planing or routing operations. Your
hearing can be permanently damaged if exposed to high noise levels for long periods of time.
DO NOT OVERREACH
Keep proper footing and balance at all times.
MAINTAIN TOOL WITH CARE
Keep tools sharp and clean at all times for the best and safest performance. Follow the manufacturer's
instructions for lubricating and sharpening and also for changing accessories.
DISCONNECT POWER FROM THE TOOL
Before servicing or when changing accessories always disconnect the power supply to avoid accidental
starting.
AVOID ACCIDENTAL START UP
Although most machines are now equipped with NVR switches, develop the habit of making sure the
switch is in the "OFF" position before connecting the machine to the power supply.
05
Summary of Contents for SIEG Super X2 Mill
Page 21: ...Troubleshooting 20 ...
Page 22: ...Troubleshooting 21 ...
Page 23: ...Parts Breakdown Part 1 22 ...
Page 24: ...Parts Breakdown Part 2 23 ...
Page 25: ...Parts Breakdown Part 3 24 ...
Page 26: ...Parts List 25 ...
Page 27: ...Parts List 26 ...
Page 28: ...Parts List 27 ...
Page 29: ...Parts List 28 ...
Page 30: ...Parts List 29 ...
Page 31: ...Notes 30 ...