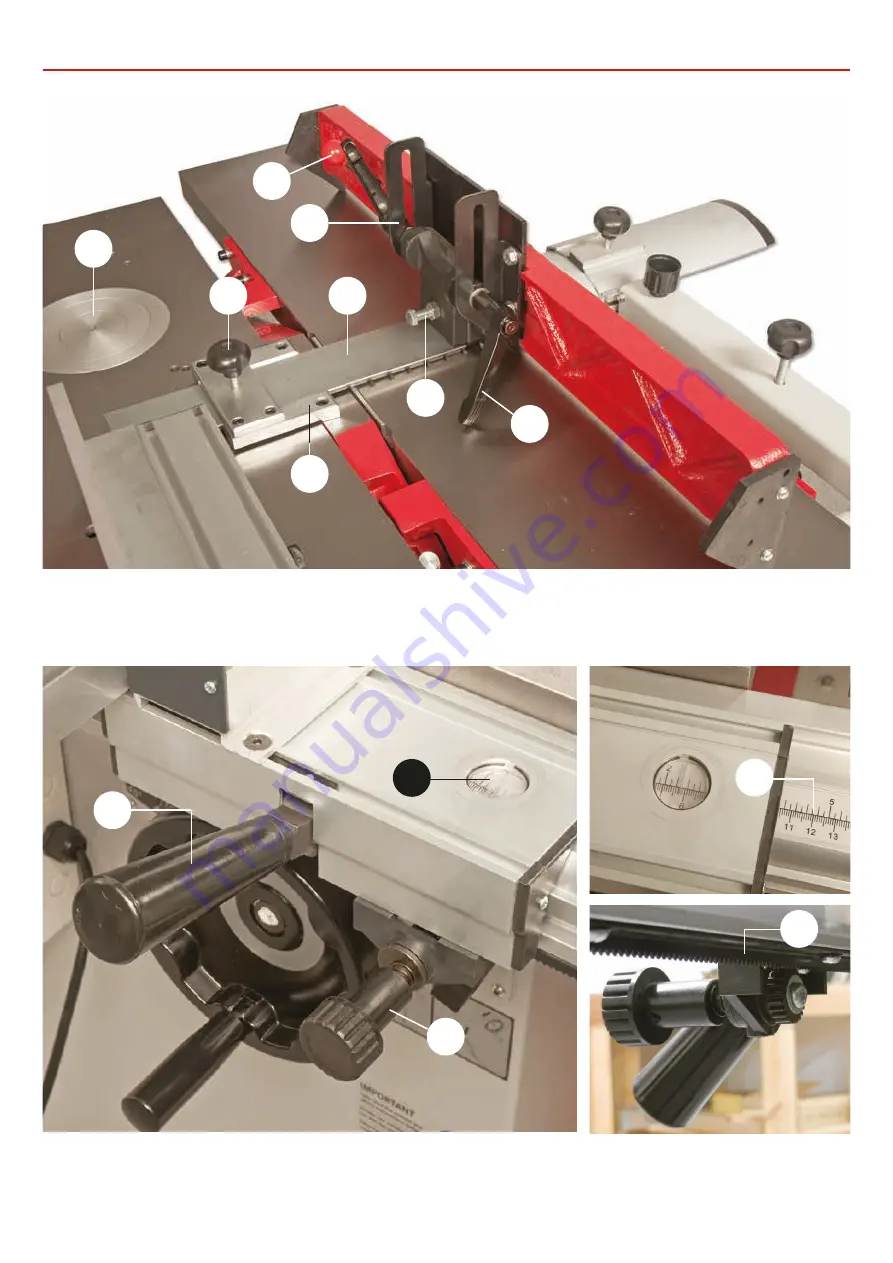
Illustration and Parts Description
24
Fence securing clamp (A), Fence mounting bracket (B), Planer fence base (C),
Elongated fence support bracket (D), Fence locking handle (E),
Fence positioning knob lever (F), Fence adjusting bolt (G), Spindle moulder circular rings (H)
Rip fence locking handle (A), Rip fence micro adjuster (B),
Magnifying glass (C), Fence rail scale (D), Fence rail rack (E)
C
B
A
E
D
F
G
C
D
E
B
A
H
Summary of Contents for AC250CM
Page 17: ...Machine Foot Print 17 2020mm 1920mm Sliding Table Sliding Table ...
Page 18: ...Illustration and Parts Description 18 Spindle Moulder Set Up Panel Saw Set Up ...
Page 19: ...Illustration and Parts Description 19 Planer Set Up Thicknesser Set Up ...
Page 36: ...Exploded Diagrams Lists 36 Planer Thicknessser Assembly ...
Page 37: ...Exploded Diagrams Lists 37 ...
Page 38: ...Exploded Diagrams Lists 38 ...
Page 42: ...Exploded Diagrams Lists 42 Panel Saw Spindle Moulder Assembly ...
Page 44: ...Exploded Diagrams Lists 44 Panel Saw Assembly 1 ...
Page 46: ...Exploded Diagrams Lists 46 Panel Saw Assembly 2 ...
Page 49: ...Exploded Diagrams Lists 49 Continues Over Spindle Moulder Assembly ...
Page 54: ...Wiring Diagram 54 ...