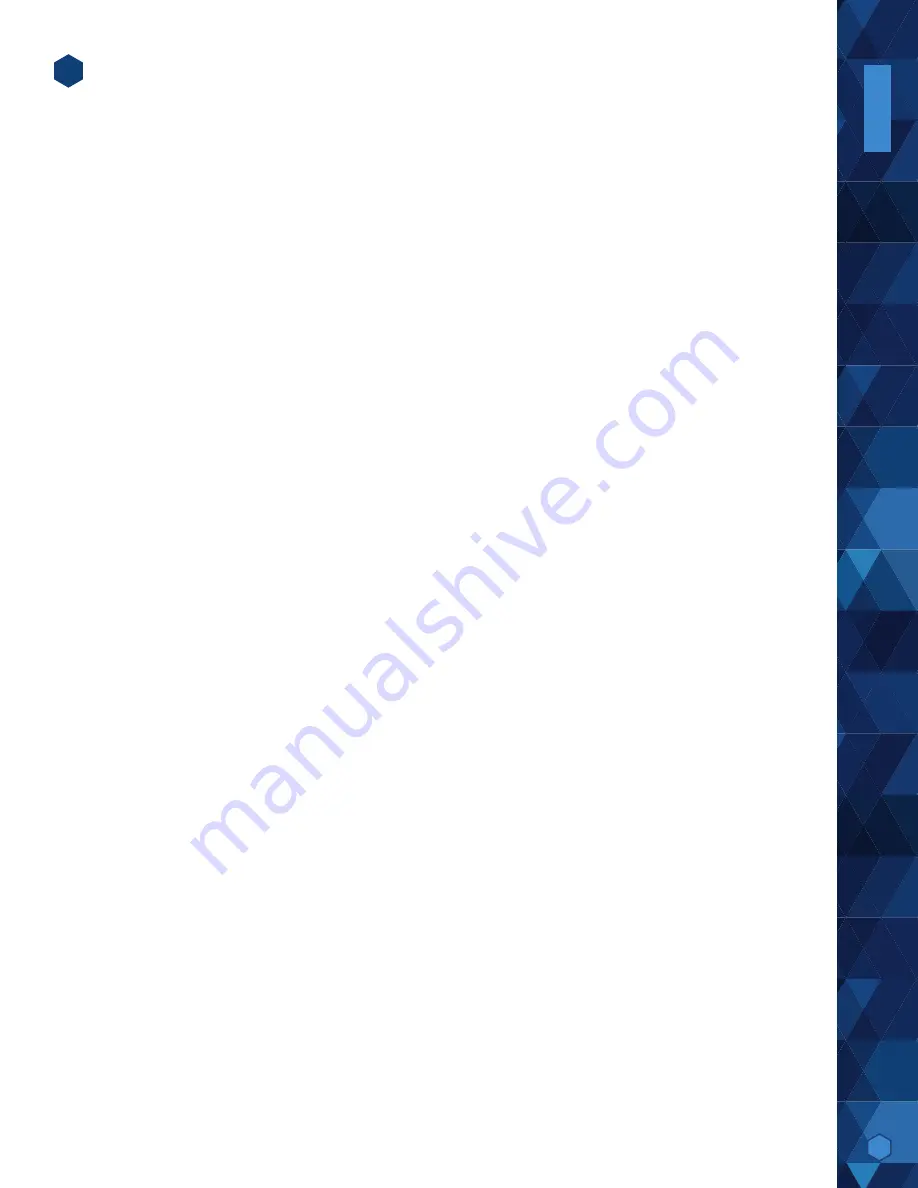
5
O
VER
VIEW
S
Y
S
TEM C
OMPONENT
S
PRIMAR
Y INSPECTION
INS
TALLA
TION
OPERA
TION
PRIMING
C
ONTR
OLLER
C
OMMISSIONING
MAINTENANCE
REV0303500011217
General Overview
MTC-500
Specifications
Note: The system is designed to meet environmental standards for safe operation. (Not for use with fluids that have a
flash point below 100°F (37.8°C), e.g. gasoline, alcohol, etc.)
Flow Rate ................................................................................
Outline Dimensions (Enclosure) ............................................
System Weight .......................................................................
Operating Temperature ..........................................................
Electrical .................................................................................
Pump .......................................................................................
Motor .......................................................................................
Fuel Conditioner .....................................................................
Inlet ..........................................................................................
Outlet(s) ..................................................................................
8 GPM/480 GPH (30.3 LPM/1814 LPH)
48” x 22.5” x 25” (122 x 57 x 63 cm) (H x W x D)
≈ 140 lbs (63.5 kg)
41 - 104°F (5 - 40°C)
115V/60Hz/15A or 230V/50Hz/15A
Self Priming Rotary Vane Pump
1 HP single phase, thermally protected
LG-X 1500
1” NPT male port
3/4” NPT male port
O
VER
VIEW