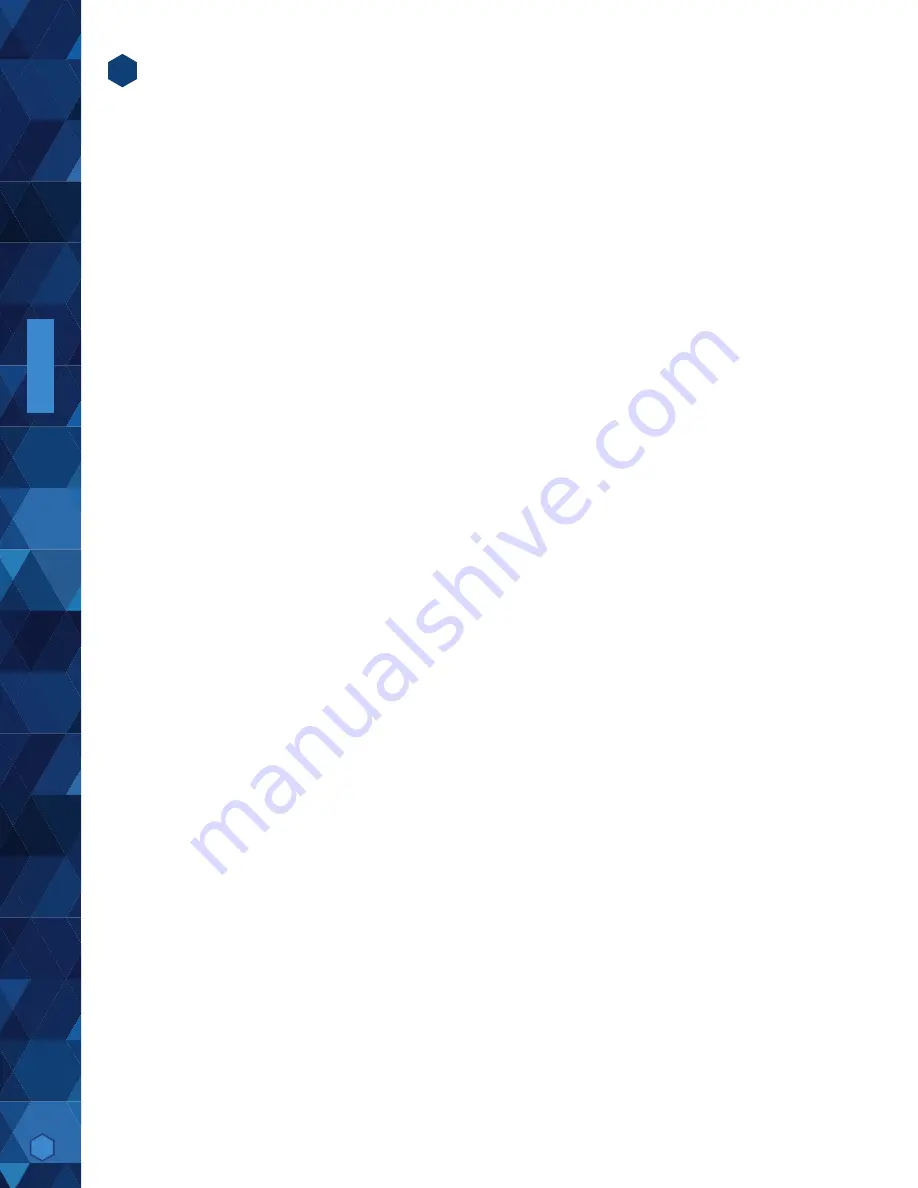
8
S
Y
S
TEM C
OMPONENT
S
PRIMAR
Y INSPECTION
INS
TALLA
TION
OPERA
TION
PRIMING
C
ONTR
OLLER
C
OMMISSIONING
MAINTENANCE
REV0303500011217
O
VER
VIEW
OPERA
TION
System Operation
Operating Procedure
Hoses:
The intake/suction hose is a clear, see-through reinforced vacuum hose. The return hose is black or blue/black, non-
marking, high quality, discharge fuel hose. Both hoses are equipped with quick disconnects or Cam & Groove couplings.
1. Attach quick disconnect end of clear suction hose to the quick disconnect Inlet Port of the MTC.
2. We highly recommend attaching a straight wand or pipe (cut at an angle at the end that goes into the tank and is at
minimum the same inner diameter as the suction hose) to the suction hose to reach the lowest part of the tank bottom.
3. Attach quick disconnect end of blue/black discharge hose to quick disconnect Discharge Port 1 of MTC.
4. Place the end of the discharge hose in an appropriate-size container (Phase One only). Try to not agitate the fuel in the
tank and stir up and disperse water and sediment throughout the fuel –this will make it more difficult to remove later on.
5.
For Phases Two and Three, place the end of the discharge hose back in the tank as far away as possible from the
suction hose. Ensure that the hose is secured and will not vibrate out of the container when the system is operating.
6. Verify that both drain valves are closed and the system is set up in a stable and safe position.
Note: Never restrict the flow on the suction side of an MTC; e.g. by using a smaller ID hose or pipe or attaching the suction
hose to a fitting on the tank that has a smaller ID than the hose. This will lead to excessive pump load, noise and ultimately
damage the pump.
Phase 1:
AXI recommends 3 phases to successfully polish a fuel tank. This will ensure all water is removed from the fuel, particulate
is removed, and the fuel is in an optimal condition. The goal of Phase One is to remove any free water and sludge on the
bottom of the tank without mixing the water into an emulsified state within the fuel.
Start the pump motor and be ready to
immediately stop it. The vane pump will start pumping as long as the system is primed and the suction lift is not excessive.
The flow of fuel can be observed in the see-through suction hose. Watch for a steady flow of fuel into the container.
1.
Once the fluid begins to fill the discharge container, immediately switch off the motor and inspect the discharged fluid.
Resume pumping and continue the above procedure until water and sludge have been removed from tank bottom and
primarily fuel is discharged from the return hose.
2.
To remove as much of the free water and sludge as possible, the suction hose with a straight wand or pipe attached
should be placed at the deepest part of the tank. If possible, move the suction hose/pipe to different areas of the tank
to more efficiently vacuum the sludge off the bottom. After removing the bulk water and sludge from the tank, switch off
the pump. Then, drain all water and debris from the hose and the water separator into an appropriate bucket placed
under the drain valve.
Phase 2:
After removing the bulk of the sludge and water from the tank into a separate container for disposal and draining the
separator, the return hose is now inserted into the tank. The goal of Phase Two is to remove any additional free water within
the tank and also remove any large contaminants and sludge. This phase will clean the fuel and should be a precursor to
using the more expensive spin-on filters. It should be noted that meeting required cleanliness codes is typically not possible
with pre-filtering alone. Phase Two is used to extend the life of the spin-on filters, and remove the worst of the contaminants,
before polishing with fine filters to meet the required cleanliness.