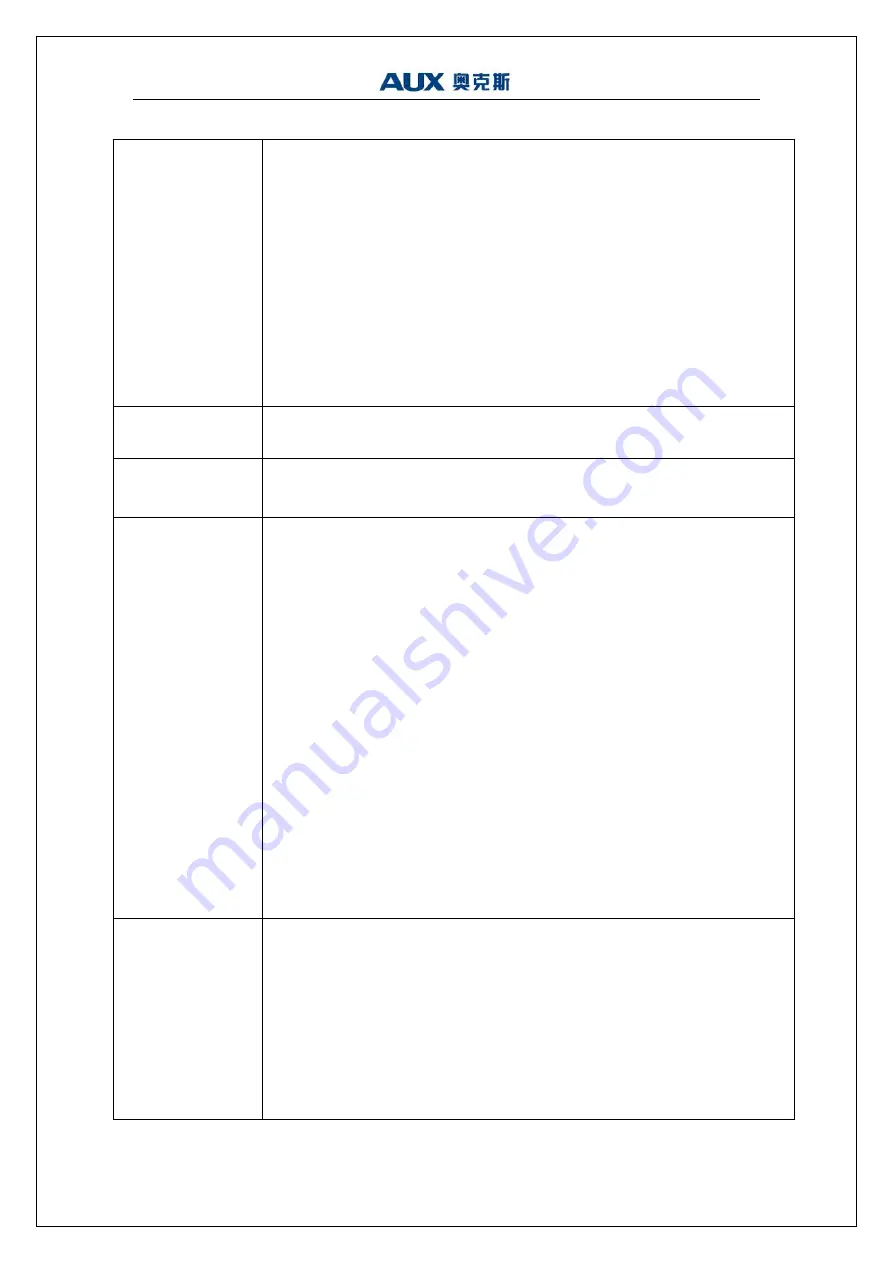
34
(6) E4- Indoor Unit motor error of wall mounted air conditioner (DC motor)
Explanation of
error
Cause:
The Indoor Unit motor of some highly energy efficient models
is DC motor using a green plug through which the Indoor Unit main
PCB can drive the motor and sense the current rotational speed
feedback. When the Indoor Unit main PCB cannot receive the
rotational speed feedback signal of the motor, it will indicate “DC
motor error”. Disappearance of the rotational speed feedback signal
may be caused by:
1 The fan is stuck and cannot work; 2 The speed feedback element
inside the motor is destroyed; 3 There’s something wrong with the
speed feedback signal receiving circuit of the Indoor Unit main PCB.
Inspection path:
Is DC motor stuck by foreign matter→motor
destroyed → Motor terminal connectors→Indoor Unit main PCB
Tools required
for inspection
Multimeter, a DC motor in normal w0orking condition
Frequent
problematic part
Mechanical jam of Indoor Unit motor, Indoor Unit DC motor, Indoor
Unit main PCB
Inspection
procedure and
key points
1. Check whether the motor accelerates to extremely high speed before
the error occurs. If it can work for a period, the reason of mechanical
jam can be excluded.
2. Plug and unplug the terminal of the DC motor again to exclude any
motor error due to connector loosening, and pull the terminal slightly
for inspection if necessary.
3. Replace the motor in the faulted air conditioner with other DC motor
to plug in the Indoor Unit main PCB (do not fix it with the fan for the
time being), if the main PCB still indicates “DC motor error”, then
replace the Indoor Unit main PCB; if the error disappears, replace the
DC motor.
4. Multimeter can be used to distinguish whether it is main PCB
problem or motor problem by: connect the motor with the main PCB
and pay attention to the second (yellow) and fourth (black) wire from
the outermost side among four lines of the terminal of the DC motor.
After the air conditioner powers on in the cooling mode for a while, the
voltage between the yellow and black wires should rise gradually and
the motor should accelerates slowly, if the DC motor still won’t rotate,
then the DC motor is destroyed.
Special attention
Five lead wires division:
Count from the outermost side of the four
wires of the DC motor terminal, the first blue wire is the speed
feedback wire with a voltage of 0.5-5V when the motor rotates; the
second yellow wire is the motor driving wire with a voltage of
2.0-7.5V when the motor rotates; the second white wire is 15V power
cord with a voltage of 15V in normal condition; the fourth black wire
is 0V DC earth wire which is the benchmark of all the voltage tests; the
fifth (red) wire is 310V wire which is strong with a voltage of 310V in
normal condition, so be careful of electric shock.
Summary of Contents for ASW-H09B5B4/FAR3DI-C3
Page 1: ...AUX Imp Exp Company Limited F Freedom Inverter Split Type Air Conditioner ...
Page 2: ...This manual is for professional maintenance personnel only ...
Page 7: ...4 2 2 Outdoor Unit 1 3P 1 8P 新 2P 2 3P ...
Page 17: ...14 5 Electrical Part 5 1 Wiring Diagram Indoor Unit 09K 12K 18K 24K Outdoor Unit 09K 12K ...
Page 18: ...15 18K 24K ...
Page 19: ...16 Part II Installation and Maintenance 6 Main Tools for Installation and Maintenance ...
Page 71: ...68 Remote Control Can Not Work Trouble shooting procedure ...
Page 72: ...69 9 Exploded Views and Parts List 9 1 Indoor Unit ...
Page 74: ...71 9 2 Outdoor Unit ...
Page 77: ...74 3 Remove air louver 4 Remove air filter 5 Remove Medium frame wiring cover ...
Page 78: ...75 6 Remove medium frame 7 Remove Control the lid 8 Remove Electric box ...
Page 79: ...76 9 Remove press plate 10 Remove component 11 Remove pipe clamp ...
Page 80: ...77 12 Remove evaporator 13 Remove the blade 14 Remove Motor press plate ...
Page 81: ...78 15 Remove Motor 10 2 Outdoor Unit Part Procedure Diagram 1 Outdoor unit ...
Page 82: ...79 2 Remove top cover 3 Remove control box cover ...
Page 83: ...80 4 Remove panel grille 5 Remove front panel ...
Page 84: ...81 6 Remove E part cover 7 Remove right side panel ...
Page 85: ...82 8 Remove axial flow blade 9 Remove outer motor ...
Page 86: ...83 10 Remove electric box assy 11 Remove motor support ...
Page 87: ...84 12 Remove reactor 13 Remove partition board ...
Page 88: ...85 14 Remove left side support plate 15 Remove pipeline assembly ...
Page 89: ...86 16 Remove stop valve assembly 17 Remove valve plate ...