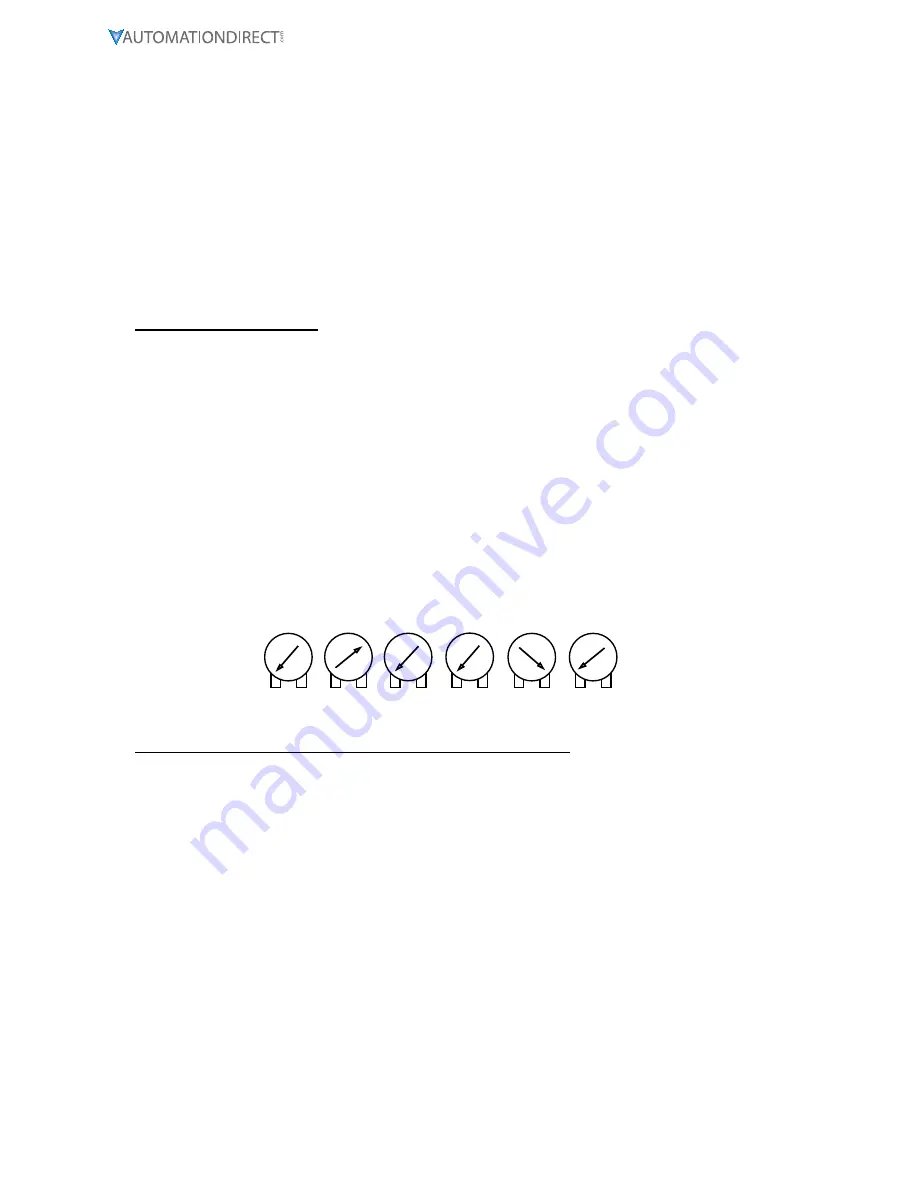
Page 11
IronHorse GSDA-DP-D DC Drives Accessory User Manual – 1st Ed. Rev. A – 11/11/2019
supply lead can be connected to this terminal for its power source.
•
P1-8 (S1) – This is the signal input terminal for the motor’s digital pickup or encoder (closed-loop
only). This signal is internally pulled-up to +5VDC via a 2.2K ohm resistor.
•
P1-9 (S2) – This input can be programmed to perform a number of advanced functions. In follower
mode, this input is the signal input terminal for the master’s digital pickup or encoder. In master modes
(rate and time), this input can be configured to function as an emergency stop, inhibit, or jog command.
This signal is internally pulled-up to +5VDC via a 2.2K ohm resistor.
•
P1-10 (1NO) – This is the normally-open contact of the user assignable relay output.
•
P1-11 (1C) – This is the common contact of the user assignable relay.
•
P1-12 (1NC) – This is the normally-closed contact of the user assignable relay output.
Basic Operating Information
Initial Drive Adjustments
Regardless of whether the GSDA-DP-D is being used in a closed-loop or open-loop operation, it is
helpful to know how to set the typical initial adjustments on the drive being controlled.
IMPORTANT: If the drive that the GSDA-DP-D is controlling has a Max Speed or Gain setting, that will
interact with the setup. Therefore, it is best to start with the drive’s Max Speed or Gain control set to about
a 2/3 of its highest setting, as shown on the drawing below. If the Max Speed/Gain on the drive is set too
low, the GSDA-DP-D may not ever be able to attain the desired speed setting, and if it is set too high, it
may be difficult or impossible to achieve stability. In the worst case, the system may hunt or oscillate.
Also, if the drive has Current Limit settings, during P-I-D tuning (only), the Current Limit should, if at all
possible, be set such that the drive is not in Current Limit. Further, when in in closed-loop operation, the
drive should never require I.R. Comp, so set that control to minimum (and leave it there). Similarly, the
GSDA-DP-D has both Accel and Decel, so those drive settings should be set to minimum (and left there).
MIN MAX
C.L.
IR
ACEL DECL
Initial Trimmer Settings
Note: Set C.L. appropriately after P-I-D Tuning!
Closed-Loop Control Algorithm Discussion and P-I-D Tuning
If the unit is configured for closed-loop operation, a true P-I-D speed control algorithm is employed,
which allows precise and quick response to set speed or load changes. The three parameters, 26, 27 and
28 (Proportional, Integral, Derivative, respectively) are adjustable as shown in the software parameters
table. P-I-D can be tuned to get precise speed response and regulation.
When adjusting P-I-D, begin by using the factory defaults the control is preset to: P (Parameter 26) to
150, I (Parameter 27) to 20, D (Parameter 28) to 10. If further adjustment of P-I-D is needed, follow these
steps:
To adjust P: (Parameter 26):
Run the motor from zero speed to the set speed. If the start up response of
the motor is too slow, increase P in increments of 20 until the desired start up response time is obtained. If
the start up response time is too fast, decrease P in increments of 10 until the desired response is reached.
P is used to adjust the start up response time only. The start up response time is approximately 0 to 60%
of the set speed. I can be used if adjustment of the upper response time (60 to 100% of the set speed) is
needed.
To adjust I: (Parameter 27):
Run the motor from zero speed to the set speed. If the upper response
time (60 to 100% of the set speed) has any hesitation or has too slow of a response, then increase I in
increments of 5 until the hesitation is eliminated and/or the desired upper response time is obtained. If
the upper response time is too fast or has too much overshoot, decrease I in increments of 3 until the