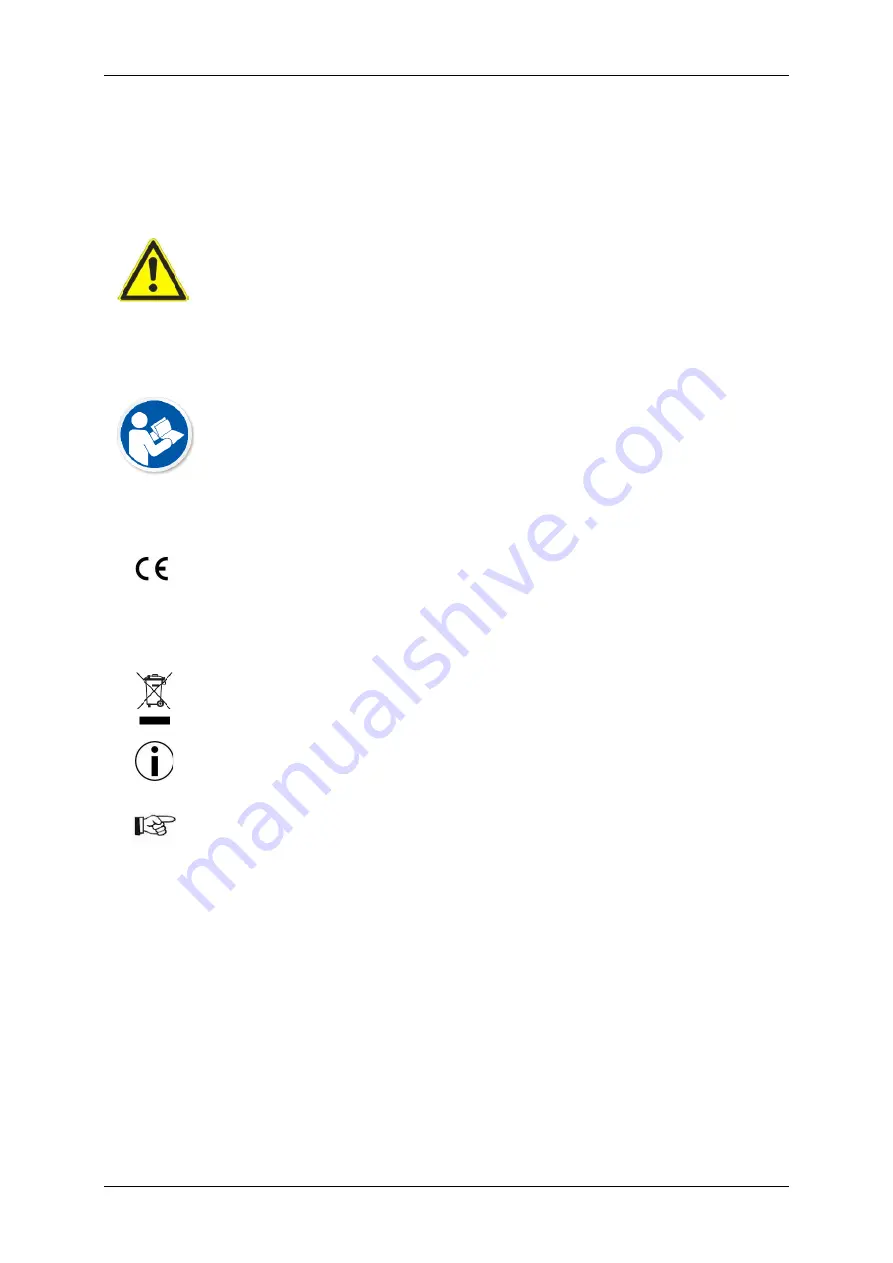
MCS Manual Rev. 1.4
5
Symbols and Notes
The following general safety rules must be taken into account during installation, operation and
maintenance. Failure to do so may cause damage to the operator, the sensor or the
environment.
Warning
•
Do not use the sensor in adverse environmental conditions, such as in
rooms with a high concentration of flammable gases, vapors or dust.
•
Make sure that all cables are routed without risk of tripping.
•
Only connect the power cord to the mains voltage after finishing the
installation of the camera.
Read the manual
•
Read the operating instructions before using the sensor.
•
Make sure that the operating personnel have read the operating
instructions and understood the contents!
•
Observe the safety instructions.
•
Observe the locally applicable safety and accident prevention regulations.
•
In case of any uncertainty contact the manufacturer.
CE marking, see Declaration of Conformity
RoHS
RoHS mark, the system complies with RoHS Directive 2002/95 / EG
WEEE mark, the system is registered according to the WEEE directive under the
WEEE-Reg.-No. DE 13042735
Safety information
General remark
Summary of Contents for MCS 1280 Series
Page 1: ...er MCS Manual Rev 1 4 User Manual for MCS cx1280 MCS cx2040 MCS cx4090...
Page 2: ......
Page 20: ...18 MCS Manual Rev 1 4 Mechanical Drawings Housing Types 1 4 2 5 3 6...
Page 21: ...MCS Manual Rev 1 4 19 Dimensions Housing Type 1 and 2 All dimensions in mm...
Page 23: ...MCS Manual Rev 1 4 21 Housing Type 3 All dimensions in mm...
Page 60: ...58 MCS Manual Rev 1 4...
Page 63: ...MCS Manual Rev 1 4 61 Mechanical Dimension All dimensions in mm Mount for DIN rail assembly...
Page 65: ...MCS Manual Rev 1 4 63 I O and Encoder with Differential HTL Mode for RS422 Option...
Page 66: ...64 MCS Manual Rev 1 4 I O and Encoder with Single Ended HTL or TTL Mode for RS422 Option...
Page 89: ...MCS Manual Rev 1 4 87...
Page 93: ...Automation Technology GmbH All rights reserved Subject to change without prior notification...