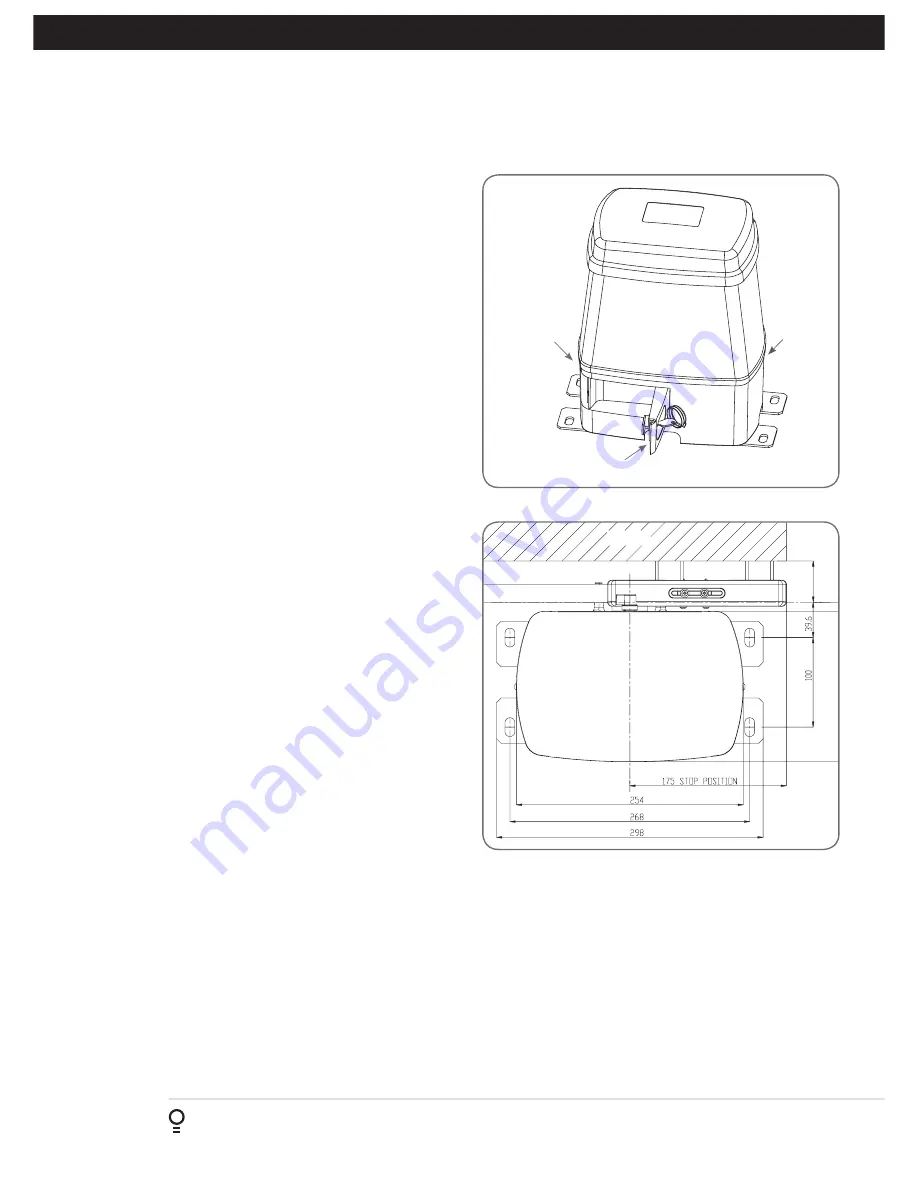
6
NeoSlider
TM
- Sliding Gate Opener NES-24V3
Owner Installation Instructions
The Automatic Technology
NeoSlider™
sliding gate opener is
designed to operate most residential sliding gates. The gates
must be in good working condition and should operate freely
by hand.
4.1 Initial Checking
Before commencing installation of the NeoSlider™, check the
following:
a. The gate moves freely and easily by hand for the full opening
and closing travel.
b. The mounting point must be solidy constructed, e.g
concrete, brick or steel, and must be capable of withstanding
the full force applied to the gate.
c. Select a suitable location for mounting the drive unit. This
position is usually established by fully opening the gate and
mounting the drive unit within a suitable distance of the
gate edge.
d. A weather-proof 240v 10 amp power outlet must be located
within one (1) metre of the NeoSlider™ mounting point.
e. If Safety Beams are to be installed, provision for underground
cabling should be made from one side of the gateway to
the other.
4.2 Mounting the Drive Unit
The NeoSlider™ mounting holes are slotted for fine adjustment
of pinion gear and gate rack alignment. Follow the procedure
below to ensure final adjustments can be made later.
We recommend that four 8mm (
5
/
16
”) or 10mm (
3
/
8
”) loxins and
bolts are used to secure the Drive Unit into position. These
loxins usually require a 16mm (
5
/
8
”) masonry drill bit (if drilling
concrete).
a. Prior to mounting the NeoSlider™, determine the distance
from the gate to the outer edge of the rack (i.e. the rack
width) and to the datum line
(see Fig. 4.2 and Fig. 5.1)
.
If using an Automatic Technology plastic rack, the width is
40mm. If using a different brand of rack, please ensure it is
Module 4 and then confirm the width, as this will vary.
b. Mark a line parallel to the face of the gate for the mounting
holes. The distance from the gate is determined by
the formula (38mm + Rack Width). Therefore, if using
an Automatic Technology rack, the distance is 78mm.
Otherwise, if using a non-Automatic Technology rack, add
your rack width (and spacers if required) to the 38mm (see
Fig. 4.2).
c. Another 100mm back, mark another line parallel to that
described in point 2 for fixing.
(see Fig. 4.2)
.
d. Open the gate to the desired open position. Mark a line at
a right angle to the gate 120-150mm from the open edge
of the gate for the mounting holes.
e. Then mark another line 268mm parallel to this line
(see Fig. 4.2)
.
f. Place the Drive Unit in position where the lines intersect to
check the mounting position. If satisfied with the position,
remove the Drive Unit.
g. Drill the four mounting holes where the lines intersect.
4. Drive Unit Installation
Fig 4.1
Cover
release
screw
Disengage lever
Cover
release
screw
Fig 4.2
h. Hammer the loxins into position, place the NeoSlider™
and fix with the four bolts. Remember when tightening
the bolts to allow fine adjustement of the NeoSlider™
later on.
4.3 Installing antenna
Mount the antenna at or above the height of the gate or
fence (whichever is higher) for optimal reception. Do not
cut the coaxial cable.