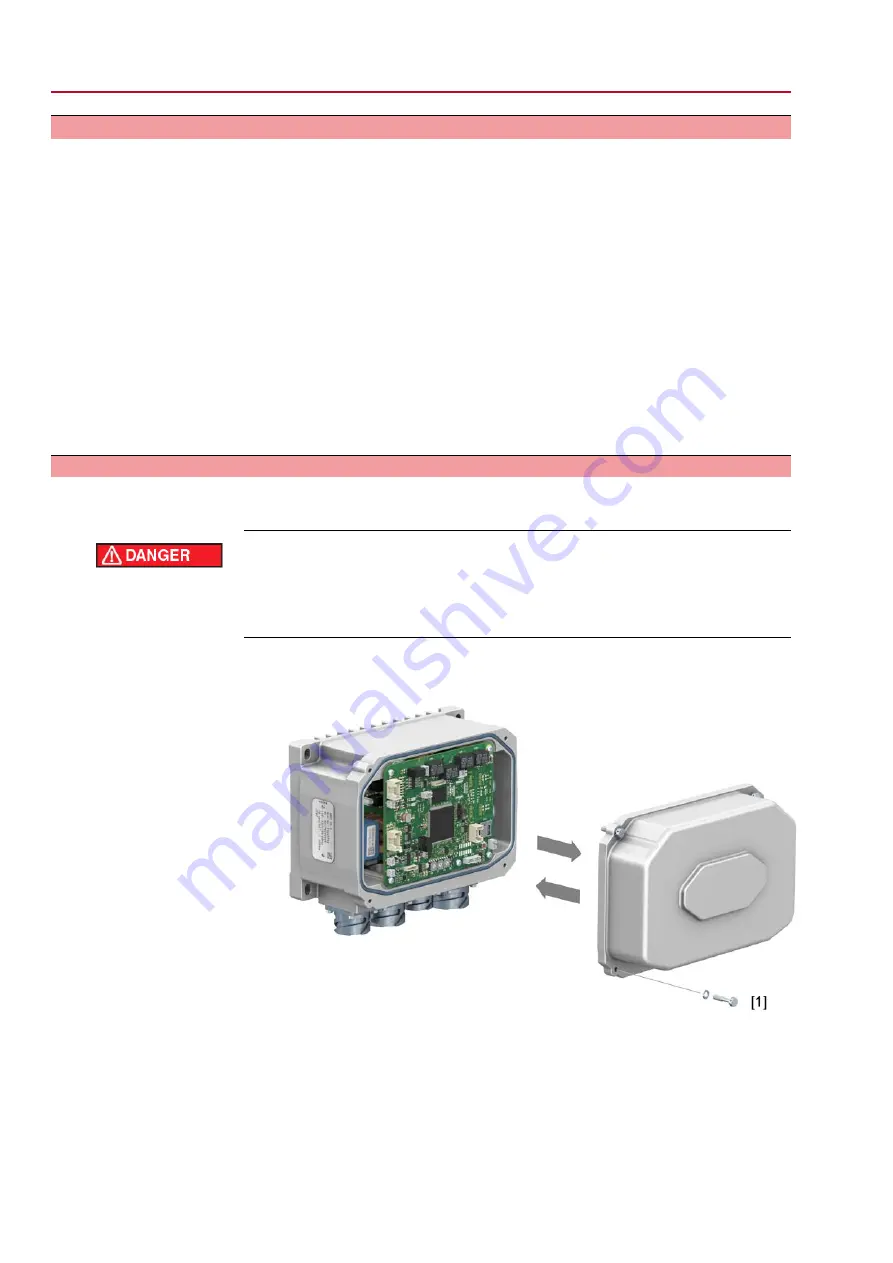
8.
Basic settings for the actuator controls
To prevent valve damage and failures during commissioning, the basic settings of
actuator controls must be verified prior to electrical actuator operation (motor
operation) and adapted in compliance with the requirements of both valve and
application.
Basic settings of the actuator controls include:
●
Setting hardware (switches) or software mode
●
Setting the type of seating
●
Setting the torque switching
●
Setting the operating time
To perform basic settings, proceed as follows:
1.
via switches (directly at the device);
For switch setting, open actuator controls cover.
2.
via AUMA CDT software (with computer/notebook, tablet);
⇨
(Software versions can be downloaded from
www.auma.com)
8.1.
Actuator controls: open/close
For changing switch settings, open actuator controls cover.
open
Electric shock due to presence of hazardous voltage!
Failure to observe this warning results in death or serious injury.
→
Disconnect device from the mains before opening.
→
Wait for 60 seconds after power cut-off prior to opening the housing.
1.
Loosen 4 screws and remove cover [1] to actuator controls.
Figure 26:
2.
Clean sealing faces of housing and cover.
3.
Apply a thin film of non-acidic grease (e.g. petroleum jelly) to the sealing faces.
4.
Check whether seal is in good condition, replace seal if damaged.
5.
Apply a thin film of non-acidic grease (e.g. petroleum jelly) to the seal and insert
correctly.
6.
Place cover [1].
7.
Fasten screws evenly crosswise.
28
SG 04.2 – SG 10.2
Basic settings for the actuator controls
with actuator controls MEC 03.1