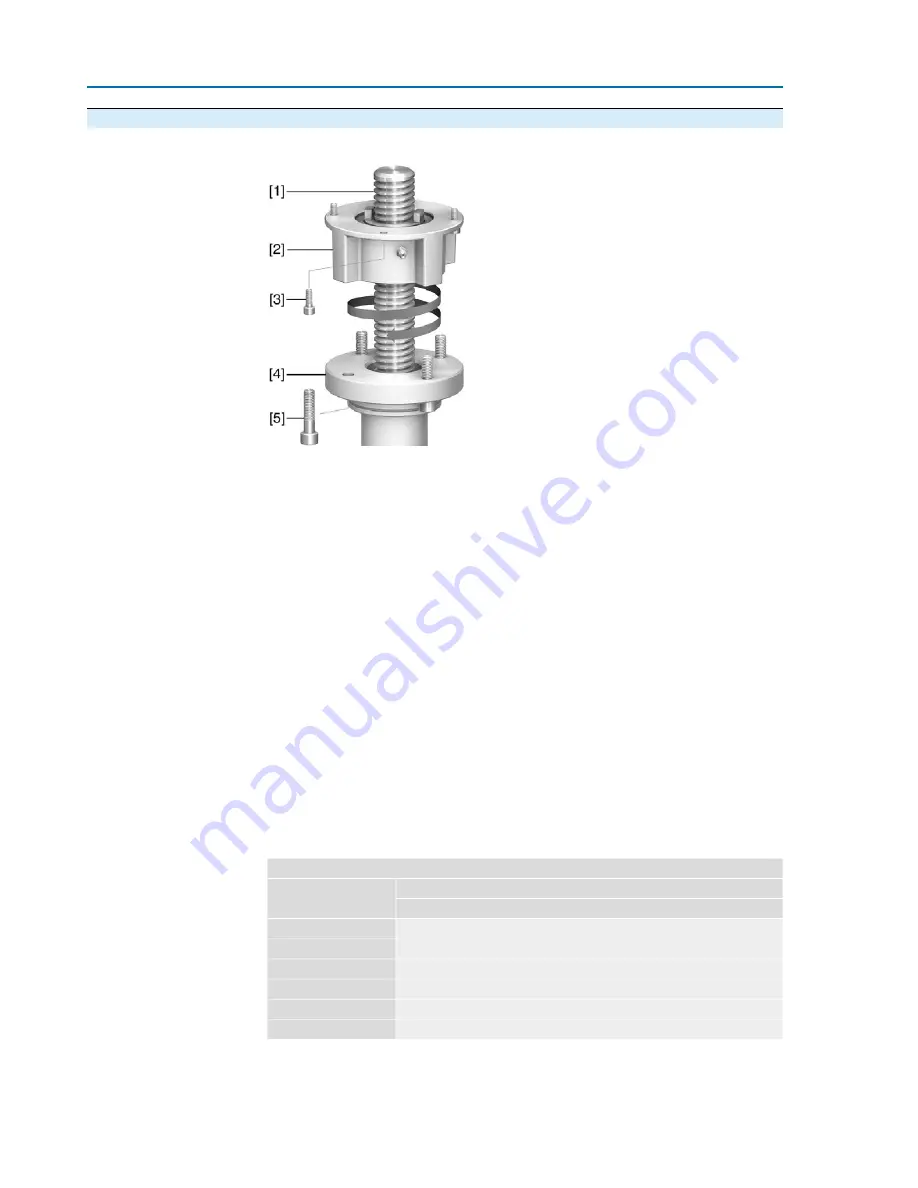
4.3.1.2. Multi-turn actuator (with output drive type A): mount to valve
Figure 10: Assembly of output drive type A
[1]
Valve stem
[2]
Output drive type A
[3]
Screws to actuator
[4]
Valve flange
[5]
Screws to output drive
1.
If the output drive type A is already mounted to the multi-turn actuator: Loosen
screws [3] and remove output drive type A [2].
2.
Check if the flange of output drive type A matches the valve flange [4].
3.
Apply a small quantity of grease to the valve stem [1].
4.
Place output drive type A on valve stem and turn until it is flush on the valve
flange.
5.
Turn output drive type A until alignment of the fixing holes.
6.
Screw in fastening screws [5], however do not completely tighten.
7.
Fit multi-turn actuator on the valve stem so that the stem nut dogs engage into
the output drive sleeve.
➥
The flanges are flush with each other if properly engaged.
8.
Adjust multi-turn actuator until alignment of the fixing holes.
9.
Fasten multi-turn actuator with screws [3].
10. Fasten screws [3] crosswise with a torque according to table.
Table 5:
Tightening torques for screws
Tightening torque [Nm]
Threads
Strength class 10.9
15
M6
37
M8
75
M10
128
M12
314
M16
615
M20
11. Turn multi-turn actuator with handwheel in direction OPEN until valve flange
and output drive A are firmly placed together.
12. Tighten fastening screws [5] between valve and output drive type A crosswise
applying a torque according to table.
14
SAI 07.2 – SAI 16.2 / SARI 07.2 – SARI 16.2
Assembly
for use in nuclear power plants