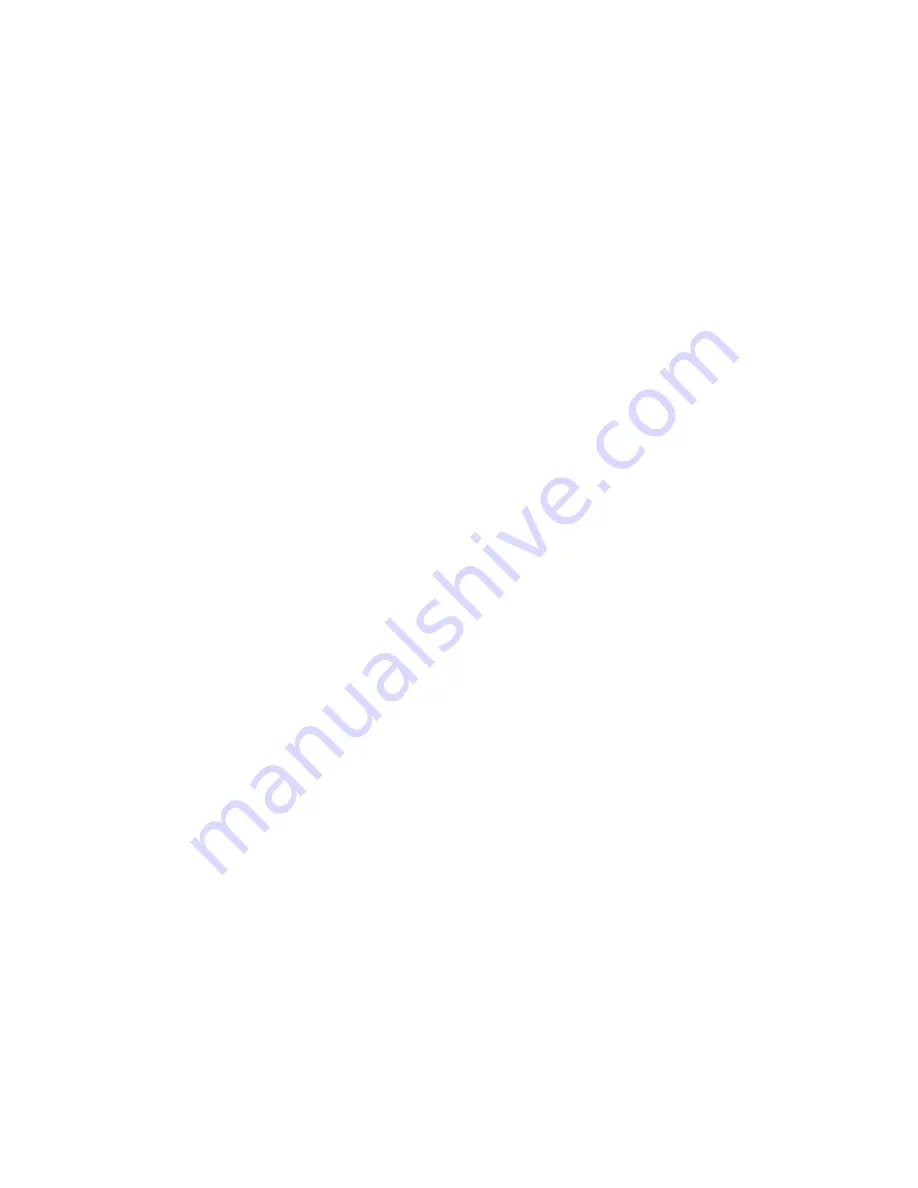
10
If you tried auto-tune and the parameters we provide but feel the performance is not ideal,
the following sections discusses the definition of these parameters and how to change
them.
LCK. Parameter lock. This function is used to prevent user from changing the
critical parameters on accident. Users have to use the code 166 to access the
parameter setting menu.
P. Proportional band. It is in 0.1 degree units. This parameter control the output of
the controller based on the difference between the measured and set temperature.
Larger the P number means the weaker the action (lower gain). e. g. If P=100, the
proportional band is 10 degree (100 x 0.1=10). When the sensor temperature is
10 degrees below the proportional band (10 degrees below the setting), the
controller will have 100% output. When the temperature is 5 degree below the set
point, the output is 50%. When the temperature is equal to the setting, the
controller will have 0% output (assuming integral and derivative functions are
turned off). This constant also affects both integral and derivative action. Smaller
P values will make the both integral and derivative action stronger. Please note
the value of the P is temperature unit sensitive. If you found an optimized P value
when operating the controller in Celsius, you need to multiply the P by 1.8 when
changing the temperature unit to Fahrenheit.
I. Integral time. The unit is in seconds. This parameter controls the output of the
controller based on the difference between the measured and set temperature
integrated with time. Integral action is used to eliminate temperature offset. Larger
number means slower action. e. g. assuming the difference between the
measured and set temperature is 2 degree and remains unchanged, the output
will increase continuously with time until it reaches 100%. When temperature
fluctuate regularly (system oscillating), increase the integral time. Decrease it if
the controller is taking too long to eliminate the temperature offset. When I=0, the
system becomes a PD controller.
d. Derivative time. The unit is in seconds. Derivative action contributes the output
power based on the rate of temperature change. Derivative action can be used to
minimize the temperature overshoot by responding to its rate of change. The
larger the number is, the faster the action will be. e.g. when the door of an
incubator is opened, the temperature will drop at very high rate. The derivative
action changes the controller output based on the rate of change rather than the
net amount of change. This will allow the controller to act sooner. It will turn the
heater to full power before the temperature drops too much
T, cycle rate. The unit is second. This unit determines how long for the controller
to calculate each action. This parameter should remain at 2 second for almost all
applications.