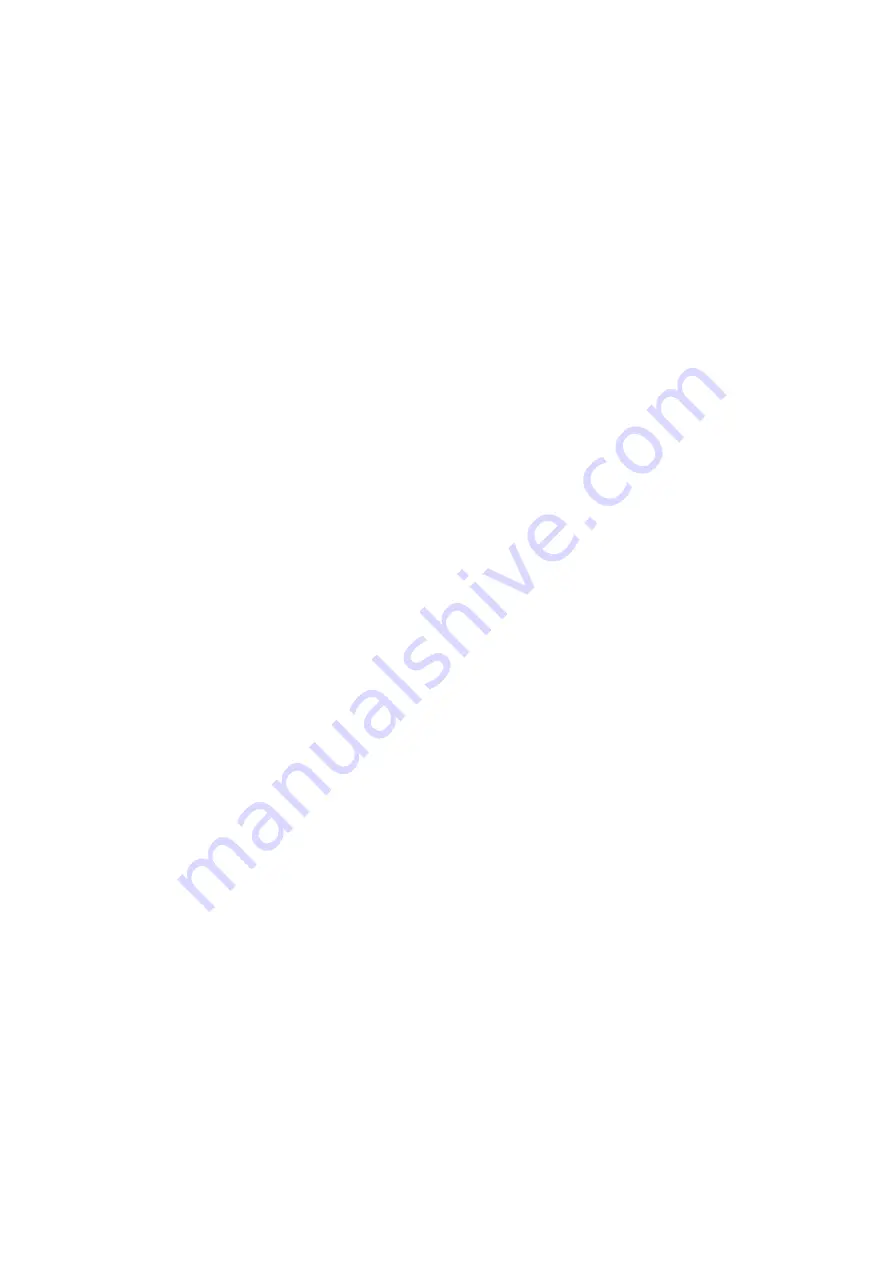
5
UMD-SRB01
Version 4
Operation
A sensor is fitted to an idler wheel or tension weight pulley acting from a wire
rope attached to the lift car. The sensor will detect movement in either direction.
A controller box will be fitted nearby and connected to the sensor, main lift
control panel, over speed governor & Rope brakes.
Once the system has been installed and set up and the rope brakes have been
reset.
The controller will receive an external signal to say that the lift doors are open,
which will activate the system to “Monitor for movement”.
If movement is detected above the predetermined limit of 100 mm to
900 mm,
(actual pre set limit is 150 mm but can be modified to suit customer
requirements)
the controller will actuate a safety relay causing all safety systems
to be deployed. Once deployed, the controller will deliberately not allow the lift to
run or revert to a normal state until the brakes have been manually reset.
If no movement was detected and the controller receives a signal to say doors
are closed it will deactivate and allow normal operation of the lift and primary
safety circuit.
During its operation the control box will also continue to check the integrity
of the connection to the sensor assembly. It will also monitor the status of
the brakes.
It will perform a simple self diagnostic test to ensure all sensors are working, if a
fault develops a fault signal will be sent to the main lift control panel to request
it to bring the lift to halt at the next floor and open the doors (Please note the
controller can only send the signal and not control stopping of the lift). When the
doors open the brakes will be deployed.
If during the Monitoring phase the connection to the sensor is lost, the brakes
will be deployed.
Due to the battery backup, if mains power fails with the doors open, the system
will continue to operate and safely monitor for movement. If mains power fails
when the doors are closed the system will automatically monitor for movement
but will allow greater movement before applying the brakes.
The system is directly connected to the lift over speed governor. So if over speed
is signalled the rope brakes will be deployed immediately.
The control panel is fitted with an emergency stop button; this will allow
immediate deployment of the rope brakes with manual control.
Maintenance, other than checking cleanliness of idler pulley assembly, is
not required for the actual components of the system, but it will be strongly
recommended that the operation is regularly checked and tested by competent
persons (lift engineer) to comply with the regulations.
Specification