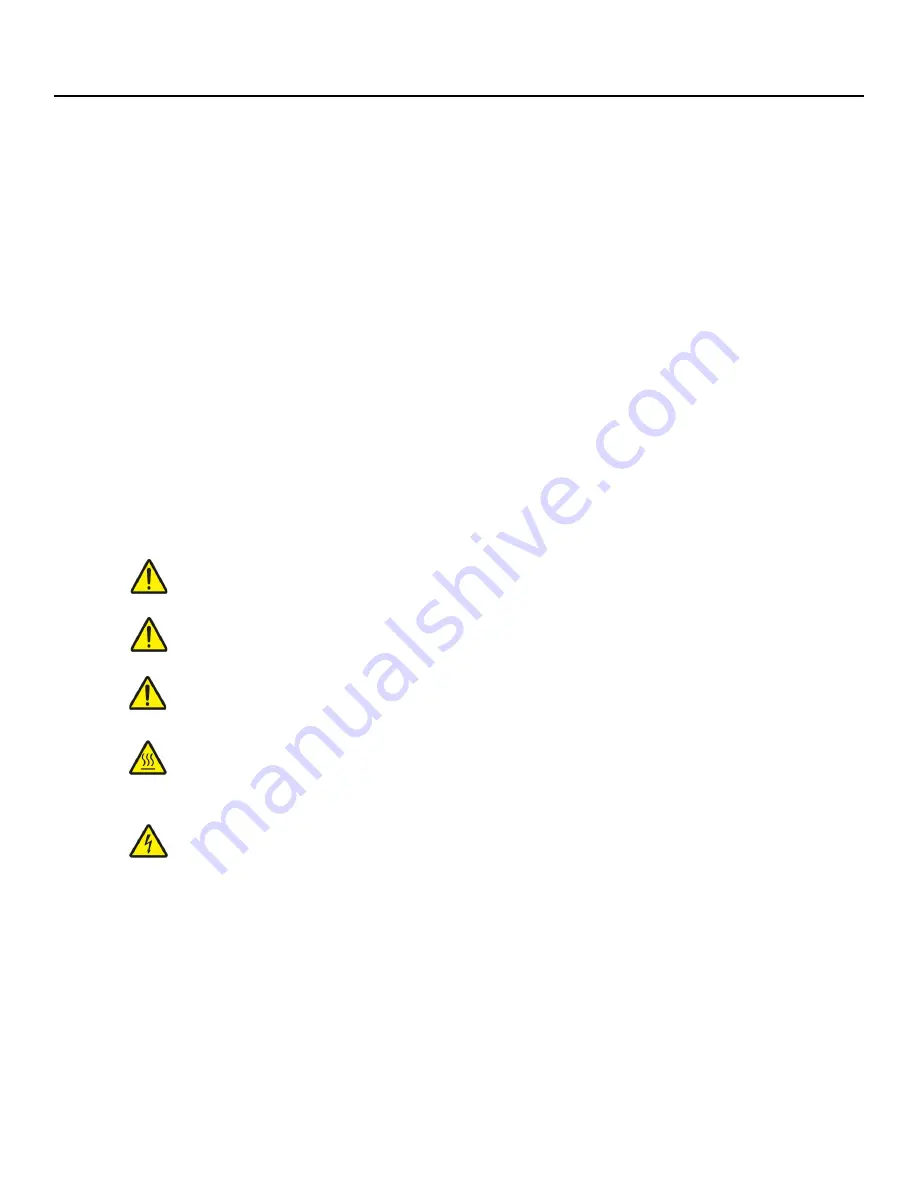
MAN - Pyrolytic Oven - REV: Original | B. Safety
3
B. Safety
B.1 For Owners, Operators, and Maintenance
All ATS equipment is designed to be operated with the highest level of safety. This manual uses note, caution, and
warning symbols throughout to draw your attention to important operational and safety information.
Read and understand all instructions and safety precautions listed in this manual before installing or operating
your unit. If you have any questions regarding operation of the unit or instructions in this manual, contact the ATS
Service Department at +1-724-283-1212.
Read and follow these important instructions. Failure to observe these instructions can result in permanent damage
to the unit, significant property damage, personal injury or death.
B.2 Safety Instructions
Your Pyrolytic Oven has been designed with function, reliability, and safety in mind. It is the user’s responsibility
to install it in conformance with local electrical codes. For safe operation, please pay attention to the alert boxes
throughout the manual.
WARNING: Warnings alert you to a possibility of personal injury.
CAUTION: Cautions alert you to a possibility of damage to the equipment.
NOTE: Notes alert you to pertinent facts and conditions.
HOT SURFACE: This symbol alerts you to a possibility of personal injury if you come in contact
with a surface during use or for a period of time after use.
ELECTRICAL SHOCK:
This symbol alerts you to a possibility of personal injury due to live
electrical components which may be exposed inside of the cover or unit.
B.3 Warnings
The following statements are WARNING statements. Unlike CAUTION statements, WARNING statements alert the
operator to conditions that may injure personnel. Operators must be aware of these conditions in order to prevent
injuries that may occur while operating this equipment.
Summary of Contents for Pyro-Clean
Page 43: ...MAN Pyrolytic Oven REV Original Appendix B Wiring Diagrams 38 Appendix B Wiring Diagrams...
Page 44: ...MAN Pyrolytic Oven REV Original Appendix B Wiring Diagrams 39...
Page 45: ...MAN Pyrolytic Oven REV Original Appendix B Wiring Diagrams 40...
Page 46: ...MAN Pyrolytic Oven REV Original Appendix B Wiring Diagrams 41...
Page 47: ...MAN Pyrolytic Oven REV Original Appendix B Wiring Diagrams 42...