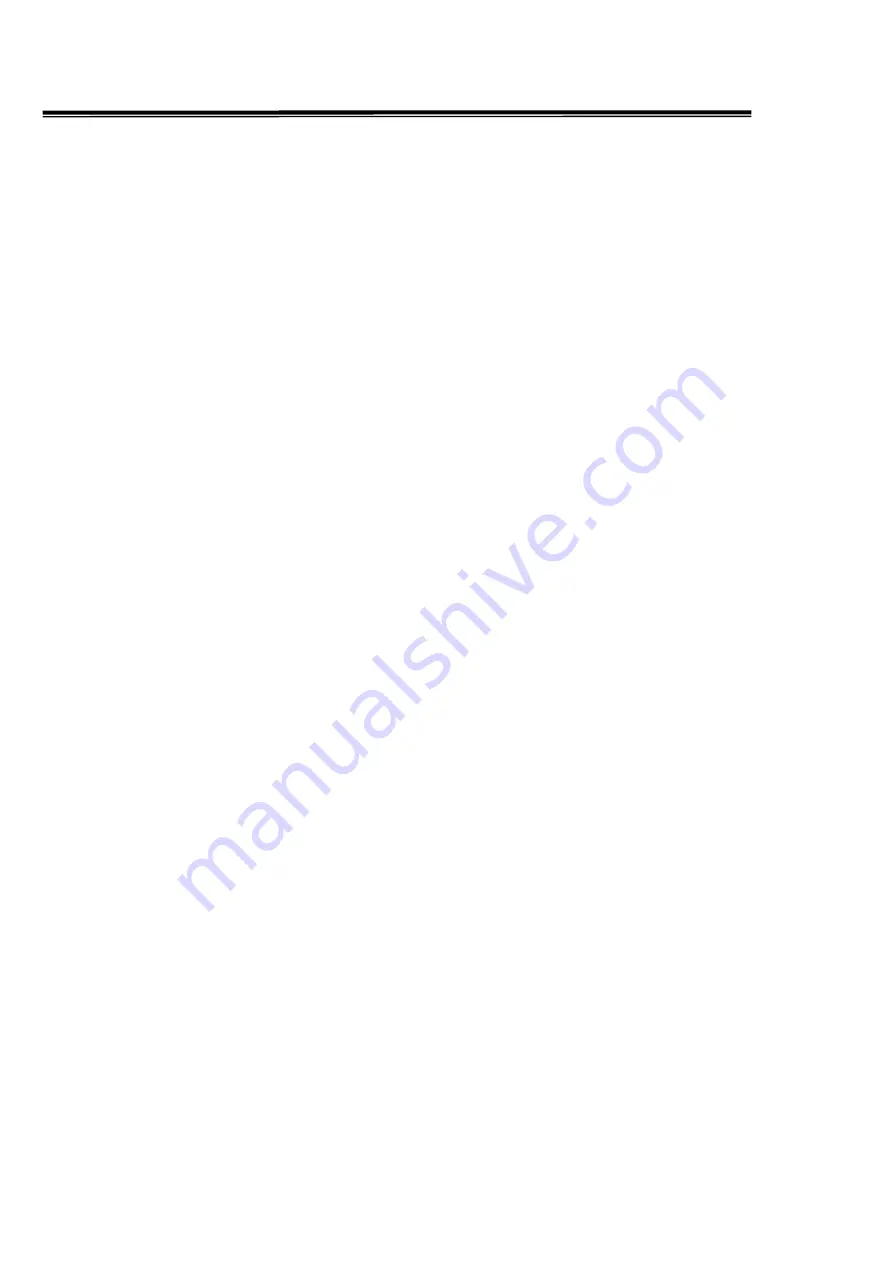
3-22 Shipping/Handling and Installation
3.9
Installation of the optional accessories
3.9.1
Chip conveyor
This machine has chip conveyor to drive away the chips from working area into chip
bucket outside the machine. Please put chip conveyor on the top of coolant tank, and
then insert them to the tunnel at the rear of bed or right side of machine. Connect the
power plug of motor onto the socket on the machine, then you can control the
operation of this device from the operator panel.
During cutting, operator should start the chip conveyor frequently, to remove the chips
while they are few instead of large quantity to prevent blockage. In the later condition,
the remove rate will be down.
3.9.2 Oil mist collector (options)
When there is oil/mist or toxic vapor occurred during cutting, oil/mist collector is highly
recommended. This device usually is installed prior to shipment. Just start this device
during operation to have clean air in the environment and offer no harm to health.
During operation, the operator should clean the net filter frequently to keep high
filtration.
If the customer wants to install oil mist collector by himself, please break the reserved
hole on the top of machine, and then mount it, or contact us if there is any question.
Salvation, please refer to the manual of bar feeder.
3.9.3 Oil & water separator (Options)
It is possible that the cutting fluid could be polluted by lubricant oil during the cycling
process. This can be prevented by the oil & water separator. This device will be
mounted on the machine prior to shipping. The impurities can be removed by starting
up this device during machining work.
If the customer wants to add such device, he can break the reserved hole on the top
of coolant tank, and then mount this device by themselves, or contact with directly.
Summary of Contents for AL52
Page 1: ...AL52 AM52...
Page 4: ......
Page 5: ...Chapter 1 Machine Safety Regulation...
Page 29: ...Chapter 2 Machine Specification...
Page 37: ...2 8 Machine Specification AL52 Column height...
Page 40: ...Machine Specification 2 11 2 10 Dimensions of the Working Table AL52 AM52...
Page 41: ...2 12 Machine Specification 2 11 Dimensions of the Tool Holder 2 11 1 BT 40 JIS Specification...
Page 42: ...Machine Specification 2 13 2 11 2 V40 ANSI Specification...
Page 43: ...2 14 Machine Specification 2 11 3 V40 CT Specification...
Page 44: ...Machine Specification 2 15 2 11 4 CAT 40 Specification Unit inch...
Page 45: ...2 16 Machine Specification 2 12 Specifications of the Tool...
Page 48: ......
Page 49: ...Chapter 3 Shipping Handling and Installation...
Page 52: ...Shipping Handling and Installation 3 3 AL52 AM52...
Page 54: ...Shipping Handling and Installation 3 5...
Page 63: ...3 14 Shipping Handling and Installation...
Page 72: ...Chapter 6 Lubrication...
Page 76: ...6 4 Lubrication EV 860 1050 Operation s Maintenance Manual AM52...
Page 80: ...Chapter 7 Mechanism...
Page 97: ...7 17 Mechanism...
Page 98: ...Chapter 8 Pneumatic Coolant Systems...
Page 101: ...8 3 Pneumatic Coolant Systems 8 2 Schematic Diagram of the Pneumatic Piping System...
Page 105: ...8 7 Pneumatic Coolant Systems 8 5 Schematic Diagram of the Coolant System...
Page 106: ...Chapter 9 Preventive Maintenance...
Page 110: ...PARTS NO MM0100030A Mar 2019...