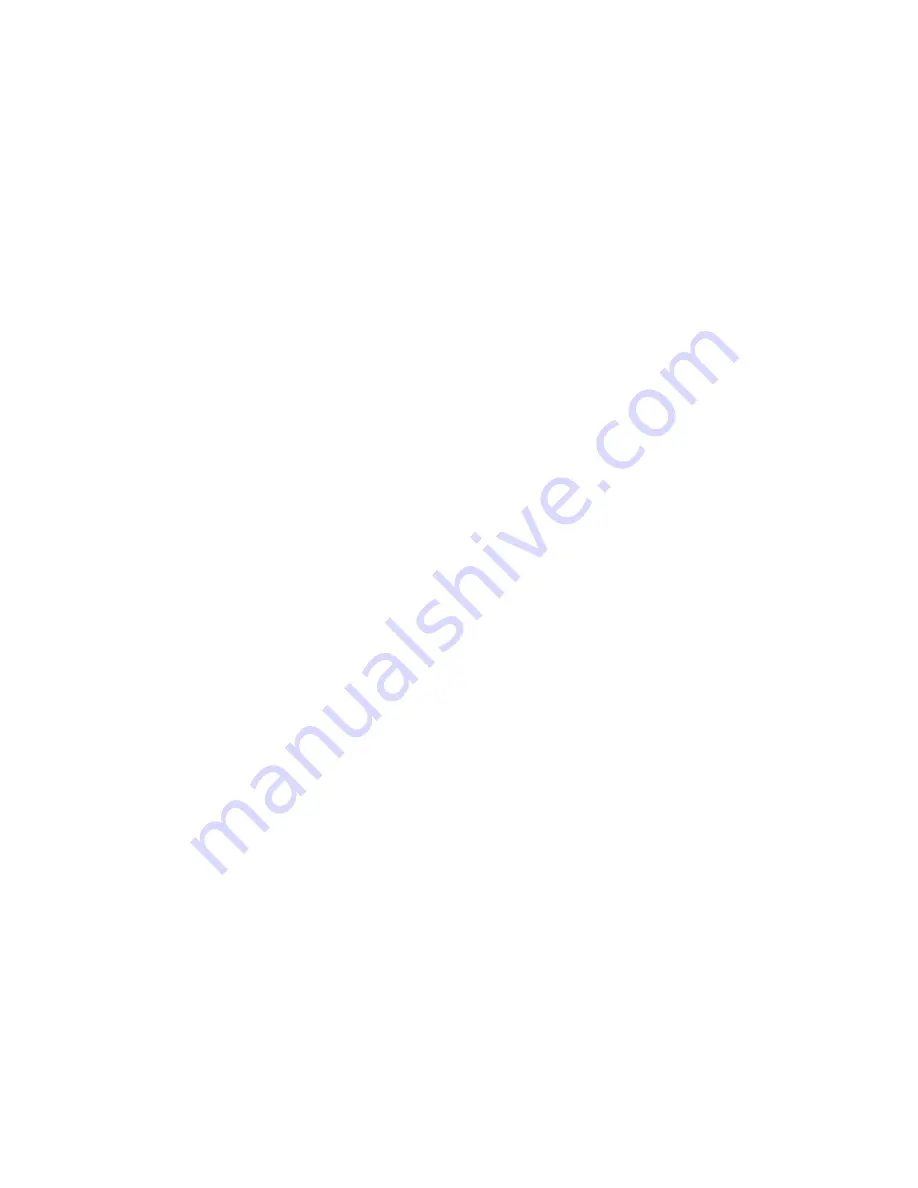
35
1 FORWARD-REVERSE SWITCH
This is the motor reversing switch. When the head is in direct drive (High Range), the motor and spindle are
turning the same direction. When the head is in “Back Gear”(Low Range), the spindle runs backwards unless
the motor direction is reversed.
In high speed (Direct Drive), the spindle is driven by tapered clutch teeth. If the clutch is not meshed tightly,
clutch rattle will be heard. This can be corrected by moving the detent plate upward as the clutch wears. This
is also the reason for possible loss of neutral, requiring the reversal of the detent plate.
3 SPINDLE BREAKE
Brake lever can be moved in either direction to stop spindle. When locking spindle, lever should be moved
right or left and then raised. There are no adjustments on brake so it must be replaced when worm out.
4 POWER FEED ENGAGEMENT CRANK
Engages power feed worm gear. When lever is in right hand hole, power feed is engaged. To disengage, pull
knob out and turn crank in clockwise or down direction and move to opposite position.
IMPORTANT: It is recommended that the Power Feed worm gear be disengaged whenever the power feed is
not required. This will avoid unnecessary wear on power feed worm gear.
5 QUILL FEED SELECTOR
This crank used to select the feed rate to be used. It is shifted by pulling knob out and turning from one
position to another, Feed rates are stamped on cover below each hole. Feed is more readily engaged with
spindle running.
6 MANUAL FEED HANDWEEL
Feed reversing knob should be in neutral position and feed control lever engaged. Clockwise rotation of
handwheel moves quill down. Manual Feed Handwheel and quill feed handheel may be disengaged by moving
them out ward approximately 1/8”.
7 FEED REVERSE KNOB
Position of this knob depends upon direction of spindle rotation. If boring with right hand cutting tools, pull
feed handle towards operator until clutch becomes engaged.
Neutral position is between forward and reverse position. It is recommended that the handle be left in neutral
position when in use.
8 FEED CONTROL LEVER
Engages over-load clutch on pinion shaft when moved left will stay engaged until either quill stop comes in
contact with micrometer adjusting nut forcing feed control lever to disengage automatically, or released
manually by moving lever to right.
11 MICROMETER NUT
This nut is used for setting of depth. Each graduation on nut indicates 001” of depth, it reads directly to scale
mounted along side of it. Depths may be obtained by setting micrometer nut in conjunction with quill stop.
Summary of Contents for A1-3T
Page 1: ...1 A Series CNC BED MILL OPERATION MANUAL...
Page 9: ...9 CHAPTER 2 Machine Specification 2 1 Machine Dimension...
Page 10: ...10...
Page 11: ...11...
Page 12: ...12...
Page 14: ...14 2 3 Machine Travel...
Page 15: ...15...
Page 16: ...16...
Page 17: ...17...
Page 20: ...20...
Page 21: ...21...
Page 22: ...22...
Page 34: ...34 Mill Head Operation Instructions for 3T 5T milling head...