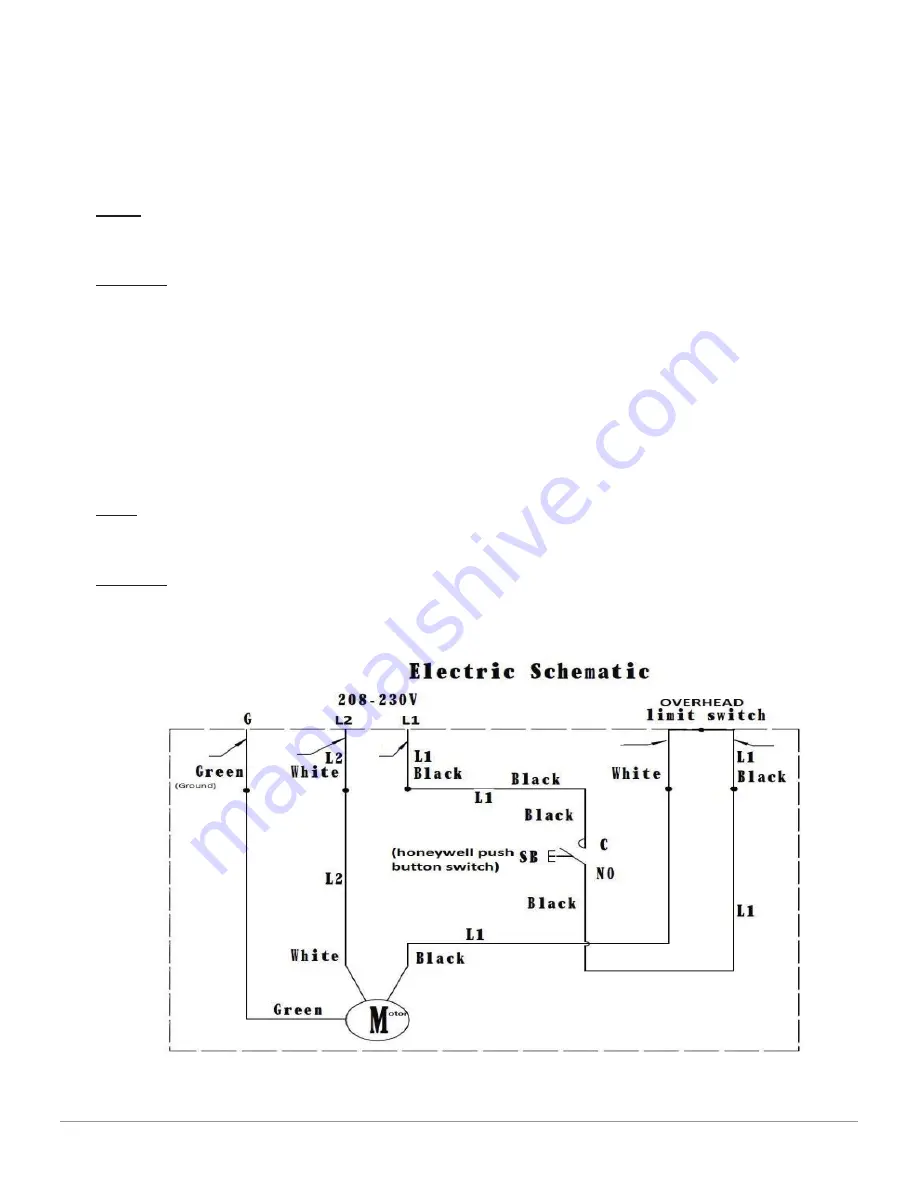
Technical Specification
16
PVL14OF-EXT
WIRING INSTRUCTIONS
To install power unit without relay:
Connect L1 incoming power line to black pushbutton switch wire #9.
Connect L2 incoming power line to white motor wire #5.
Connect incoming green ground wire to green ground motor wire.
If
using
overhead switch:
Connect one overhead switch wire to black switch wire #3.
Connect the other overhead wire to black motor wire #7.
If
not using
overhead switch:
Connect the black switch wire #3 from pushbutton switch to black motor wire #7.
To install power unit with relay:
Connect L1 incoming power line to black relay wire #6 & black pushbutton wire #9.
Connect L2 incoming power line to white relay wire #2
Connect incoming green ground wire to green ground motor wire.
Connect white relay #4 to white motor wire #5.
Connect black relay wire #8 to black motor wire #7.
If
using
overhead switch:
Connect one overhead switch wire to black switch wire #3
Connect the other overhead wire to red relay wire #1
If
not using
overhead switch:
Connect the black switch wire #3 from pushbutton switch to red relay wire #1.
Figure 6 – Electrical Diagram (220V/50Hz/60Hz/1Ph)