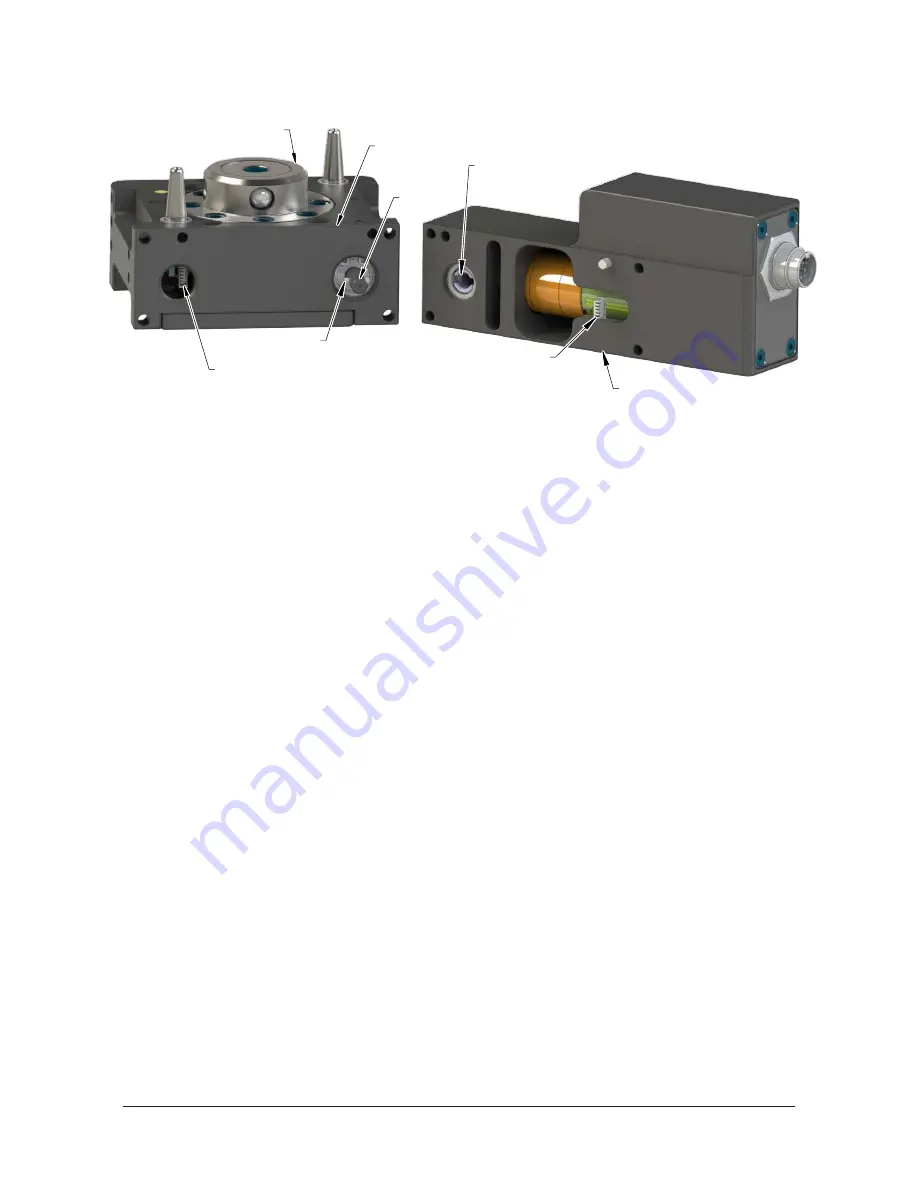
Manual, Robotic Electric Tool Changer, QC‑18
Document #9620‑20‑B‑18 Electric Tool Changer‑06
Pinnacle Park • 1031 Goodworth Drive • Apex, NC 27539 • Tel: 919.772.0115 • Fax: 919.772.8259 •
B-27
US Patent No.: 8,132,816 B2
Figure 5.5—Master Plate Flat A
QC-18 Master Plate
Sensor Connector
Drive
Shaft
Flat A
Dowel Pin
Keyed Slot in
Motor Gear
Motor Electrical
Connector
Servo Motor Module
9. If fastener does not have pre‑applied adhesive, apply Loctite 242 to threads of (4) M4 socket
head caps screws and install into the servo motor module using a 4 mm hex key. Torque to
25 in‑lbs (2.82 Nm).
10. Connect the customer interface cable to the 12‑pin connector.
11. Safely resume normal operation.