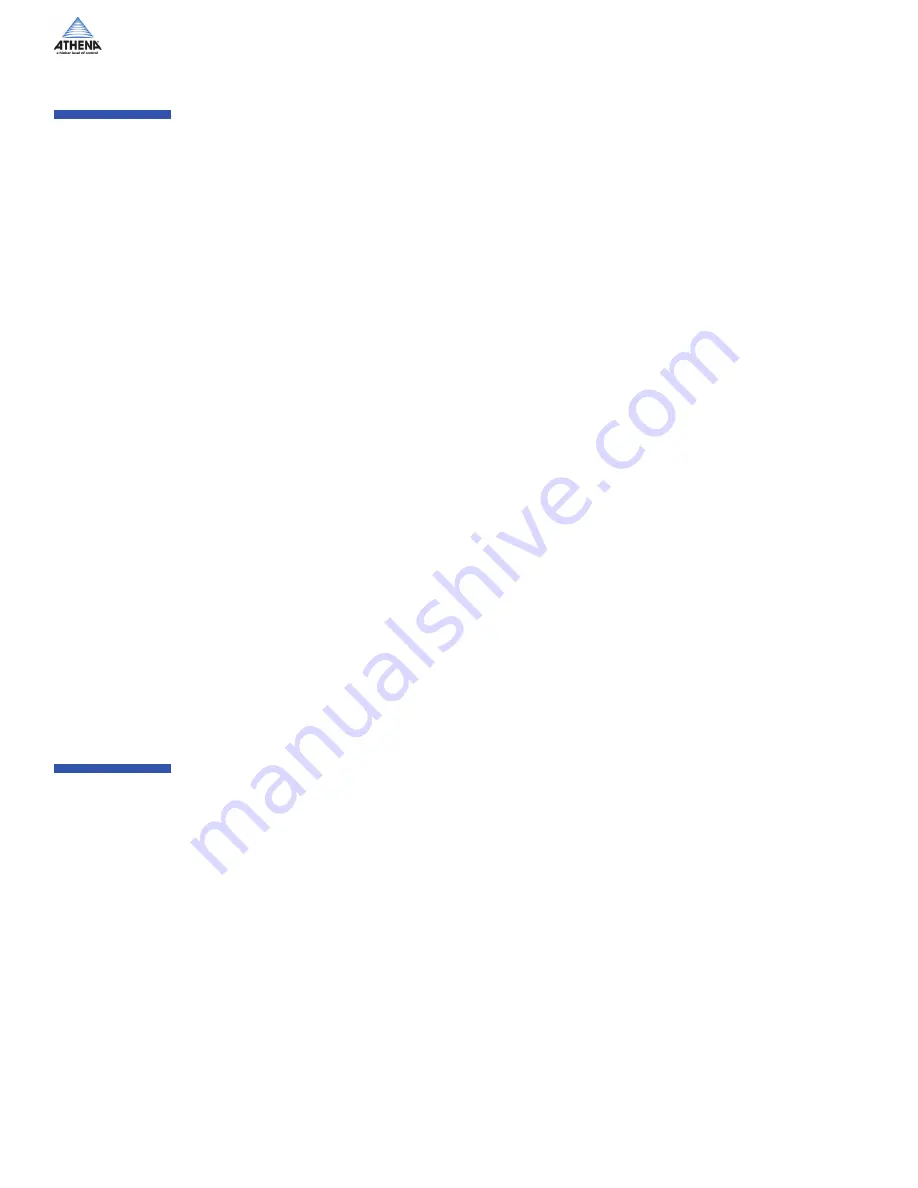
14
The Athena Series C controllers are versatile instruments that are capable of using many types of input
values and implementing several types of control strategies. To support this versatility, the Series C
controllers are capable of storing values for many confi guration parameters. Interrelationships exist between
the parameters. Therefore, it is important that you confi gure the parameters in the correct sequence.
If you plan to use a thermocouple or RTD input and if you do not plan to use degrees Fahrenheit (the default
unit of measure), the fi rst step is always to specify the unit to be used (Celsius or Kelvin) using the
(display) menu
parameter. The input type parameter is confi gured at the factory to match the type
of calibration specifi ed when the controller was ordered. If the controller was calibrated and confi gured at
the factory for a linear input type, the units of measure parameter will not be included in the display menu
until you change the input type. When changing the input from a linear to a temperature input (or vice
versa), the input jumper settings must also be changed, and the controller must be re-calibrated (unless
the “calibrate all” option was specifi ed when the controller was ordered). The controller uses this unit of
measure for internal operations, as well as for external communications. When you change the units of
measure for temperature inputs, the controller recalculates any values that have already been specifi ed.
For example, if you want the setpoint to be 100
o
C, then you must change the units from the default F to C
before you write the setpoint of 100 to the controller. If you change the units after you write the setpoint of
100 to the controller, the controller will convert the 100
o
F setpoint to 37.8
o
C. In this case, you would have to
reconfi gure the setpoint to 100
o
C to implement the control needed by your process.
After the unit of measure has been changed, if necessary, from degrees Fahrenheit to your choice of Celsius
or Kelvin, the next step is always to specify the type of input that each controller will receive. That means
that you must specify the type of thermocouple or RTD that will provide the input to the controller, or, in the
case of a linear input, the range and units of the input (0 to 20 mA, 0 to 5 V, 1 to 5 V, etc.) The type of input
specifi ed aff ects how the controller processes the input signal and calculates the output needed to achieve
the setpoint.
With the exception of the unit of measure, generally the parameters should be confi gured in the sequence in
which they are presented in the menus.
In addition to being aware of the sequence in which parameters should be confi gured, you should also
remember that not all parameters apply to all applications. For example, if you specify that the input type
is a thermocouple or RTD, then you will not see the low scale and high scale parameters in the input menu.
However, if you use a linear input, then you must specify scaling values, or accept the factory defaults
(-1999 to 9999). The database values in new (“out of the box”) controllers are always the default values,
except in the case of the input type parameter, which is confi gured at the factory to match the type of
calibration ordered. (If “calibrate all” was specifi ed, the input type is set to J thermocouple at the factory.)
CONFIGURATION
SEQUENCE
WHAT HAPPENS
WHEN YOU
POWER UP
Outputs
When the controller is powered up, under some circumstances the outputs may be activated. If the
controller has been confi gured, this is good. However, if the controller is new (not yet confi gured), then
we recommend placing the controller in standby mode until you have confi gured the controller for your
application.
Display
When a controller is fi rst powered up, all segments of both lines of the LED display will be lit briefl y while the
controller goes through a series of self-diagnostics. Next the top line briefl y displays the type of controller,
while the lower line displays a fi rmware version number. Next, the top line will display
, while the lower
line displays the type of communication protocol the controller supports. Finally, the process variable (PV)
and process setpoint value (SV) are displayed, this is the normal operator display.
Setpoint
Once the controller has been confi gured, its behavior at startup depends on the choices made during
confi guration.
The controller can be confi gured to ramp gradually up to the setpoint after the controller is powered up. If
this single-setpoint ramp function has not been enabled, then the controller’s control algorithm will use the
outputs to achieve the confi gured setpoint using the confi gured control strategy as quickly as possible.