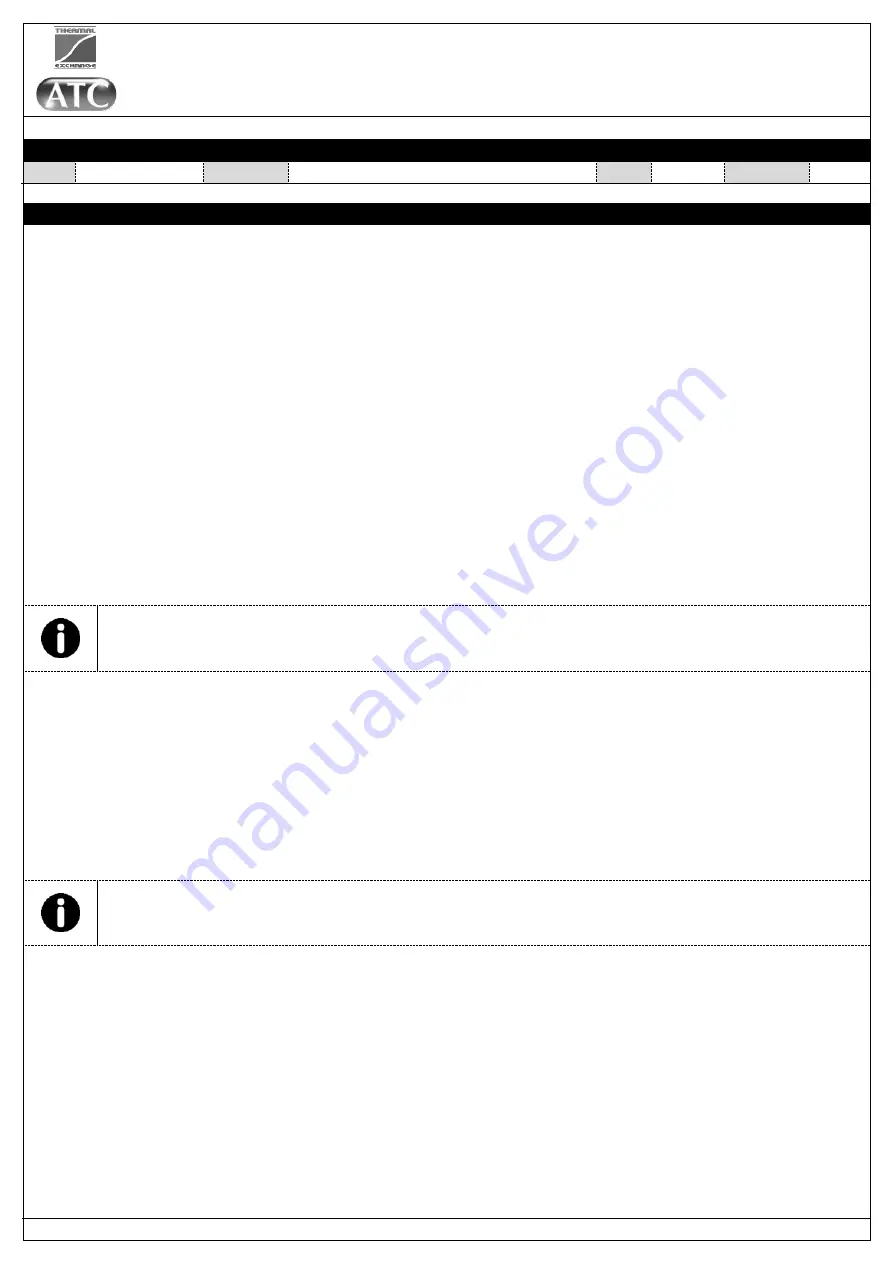
Applied Thermal Control Ltd
39 Hayhill Industrial Estate
Barrow-upon-Soar, Loughborough
LE12 8LD, United Kingdom
+44 (0) 1530 839 998
[email protected]
[email protected]
Operating Manual; Installation
Annex C-1
DOCUMENT DETAILS
Date 28/AUG/2020
Author(s) MJH/AMI
Page 1 / 1
Revision 1
INSTALLATION
Having ensured that your installation meets all site requirements, it is best practice that the fluid lines between
your application and the chiller have the following characteristics;
a)
Short in length
– this reduces friction-based pressure drop and addition ambient heat load
b)
Large diameter bore
– at least 8mm (5/16”).
c)
Free from 90° bends
– to limit the effects of water hammer. If this cannot be avoided, sharp changes of
direction should be minimized so far as possible. Doing this correctly can yield higher pump performance
and extend time between maintenance intervals. It can also reduce electrical energy consumption.
d)
Clean
– If your installation is to existing pipe work, it is good practice to flush the system with either a
commercially available central heating cleaner or 5% acetic acid solution. The system should be flushed
clean with tap water to remove all traces of cleaner prior to filling the system. Failing this, it is
recommended to use a domestic bleach in solution with tap water, diluted to the point where the bleach
can longer be smelled by a human.
e)
Opaque, ideally black
– to inhibit light passing through the tube and algae building up. Alternatively, solid
ABS or copper pipe can be used.
Caution; Never use transparent tubing. UV light will pass through, prompting growth of organic
contamination.
The Mini and EcoMini are supplied with quick release fittings by default either of the CPC or push fit variety. The
former of these have built-in valves to prevent loss of fluid when disconnecting but other types may not. The
mating halves of these connectors are available in a variety of fitting types, i.e. barb, quick release, compression.
Sealing guidelines should be followed for each specific type of fitting.
Ensure that the system is correctly connected, with the chiller outlet connected to the application inlet, and
application outlet connected to chiller inlet. Check all joints are tight and leak free.
Where this product is incorporated into other equipment, it is the responsibility of the assembler to ensure safety.
Caution; Do not replace detachable mains cords with inadequately rated cords. Contact ATC for
appropriately rated products.
Preventing Backfilling
–
In situations where the chiller is situated physically lower than the application being
cooled it is possible that upon stopping the pump the effect of gravity on the process fluid can cause it to leave
the application.
In this scenario, the fluid falls back into the chiller, placing pressure from the water column upon all chiller water
circuit faces. The weakest point in terms of sealing is the tank lid, and this is typically where fluid will escape the
unit, overflowing into the chiller.
For this reason, it
’s always a good idea to situate the chiller higher than the application so that when the pump is
turned off, the tank is the highest point in the system and the liquid will flood into the application which should be
sealed.
If this is not possible, a non-return solenoid valve kit can be installed as an optional standard assembly. Please
raise any questions with the sales team on [email protected].
Annex C-1 200901 Installation - Mini & EcoMini
8