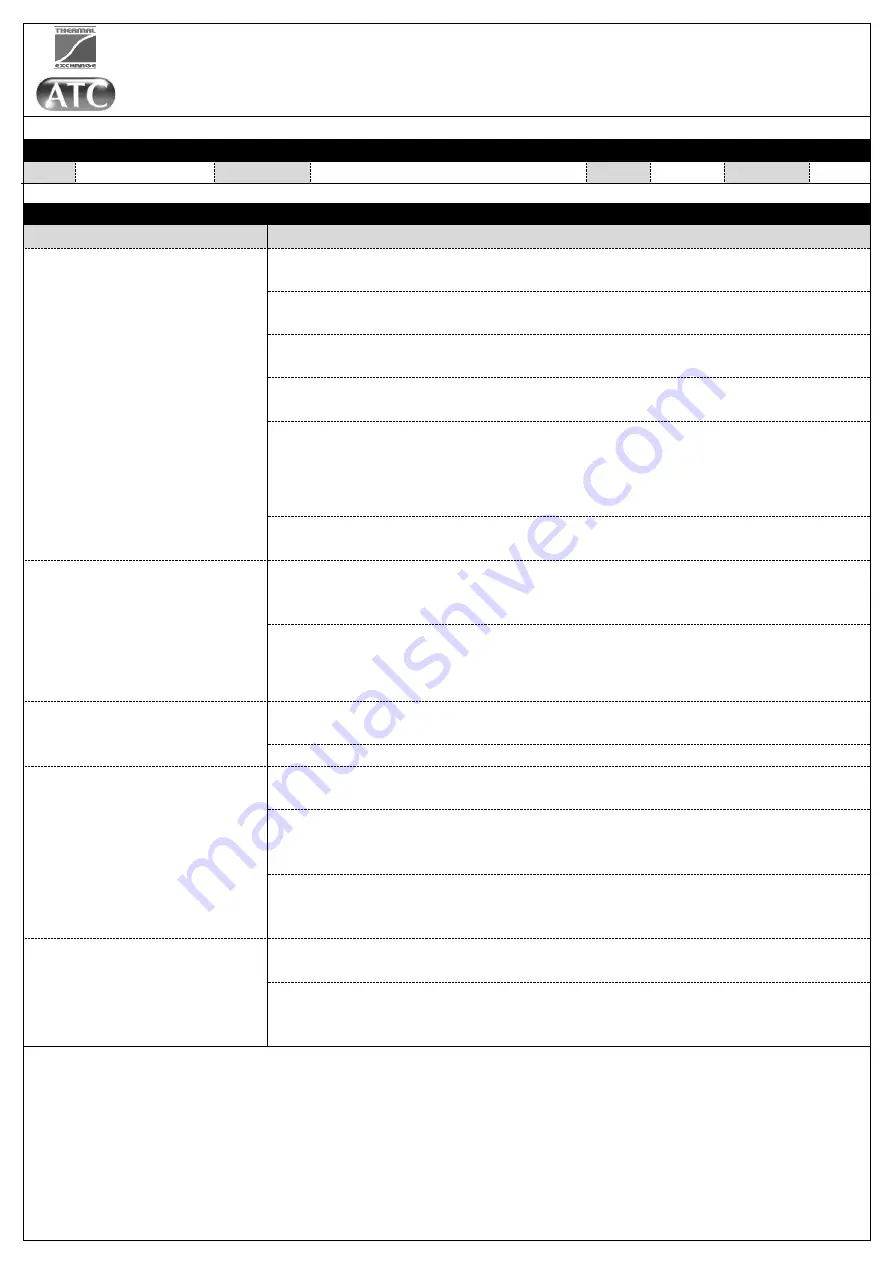
Applied Thermal Control Ltd
39 Hayhill Industrial Estate
Barrow-upon-Soar, Loughborough
LE12 8LD, United Kingdom
+44 (0) 1530 839 998
[email protected]
[email protected]
Operating Manual; Troubleshooting
Annex G-6
DOCUMENT DETAILS
Date 28/AUG/2020
Author(s) MJH/AMI
Page 1 / 1
Revision 1
ECOMINI GENERIC INITIAL TROUBLESHOOTING
Symptom
Potential Cause(s)
Compressor not running
Ensure that the minimum temperature cutoff value on the low temperature cutoff
controller is not higher than the current liquid temperature.
Ensure that the speed dial is not positioned within the compressor stop region
which is to its left most extremity.
Check the connection of the compressor power plug situated on top of the
compressor itself.
Check the connection of the signal line from the controller to the compressor
PCB control board.
When the compressor has been running for any length of time and then has
been issued a stop signal either by manually turning the speed control all the
way counter-clockwise of via the low temperature cutoff controller the
compressor will remain stopped for 60 seconds to allow system pressure to
equalize.
The compressor has built-in logic issued via its PCB control board
– board error
states are communicated to the main touchscreen controller.
Noisy operation
Usually bearing failure in rotating machinery causes noise
– this might be the
cooling fan, the compressor or the pump. Pay attention to specific components
to identify the source of noise.
If there is an air pocket within the water circuit or not enough liquid in the tank,
the pump could be running dry, this can cause rapid degradation of the pump,
top up the tank immediately if the water level is low this will also help to remove
air pockets.
Fluid lines becoming fouled /
containing biological matter
Not using opaque tubing can lead to UV light passing through the tubing,
prompting growth of organisms.
Not following maintenance schedule for cleaning/flushing.
Fluid seen leaking from system
Your fluid may be incompatible with the materials used in chiller construction.
Contact ATC to ensure the fluid is compatible.
Rapid changes in system temperature can cause some materials to change
shape at a faster rate than others. Contact ATC to discuss alternative materials
and parts in water circuit construction.
If there is too much liquid in the system due to backfilling when turned off or air
pockets it is possible that is could have leaked out around the tank cap, check
the water level in the tank periodically to ensure that it is not overflowing.
Poor cooling capacity
(undercooling)
Check for any error states on the compressor controller PCB
– the blinking LED
will indicate if an error has occurred and alter blink rate based on error number.
This can be caused by 1) excess application thermal heat load, 2) excess
ambient temperature, 3) fan failure, or 4) controller issues with compressor
control.
Annex G-6 200828 EcoMini, generic initial troubleshooting
13