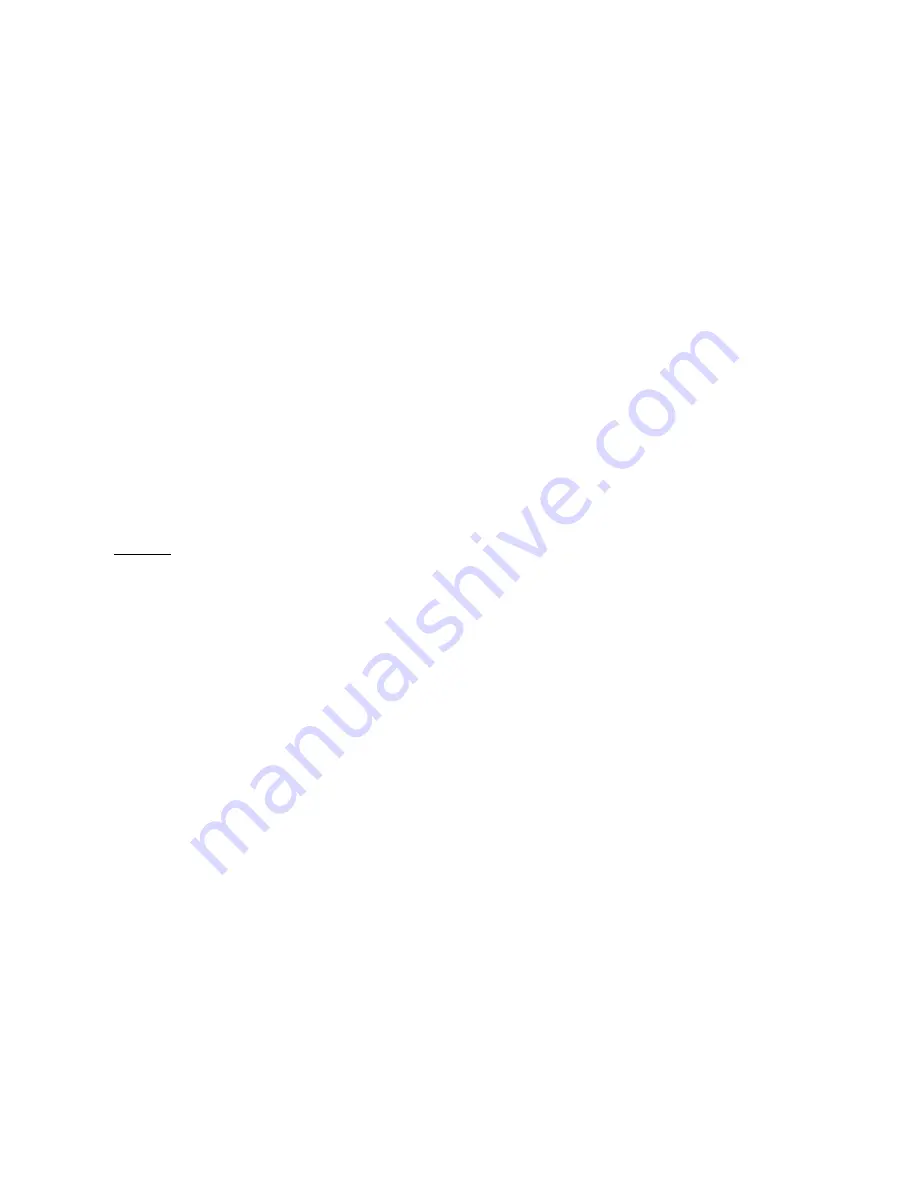
Regulated or Unregulated Power Supply:
Both regulated and unregulated power supplies can be used to supply DC power to the driver. However,
unregulated power supplies are preferred due to their ability to withstand current surge. If regulated power
supply (such as most switching supplies.) is indeed used, it is important to have large current output rating
to avoid problems like current clamp, for example using 4A supply for 3A motor-driver operation. On the
other hand, one may use a power supply of lower current rating than that of motor (typically 50%
~
70%
of motor current). The reason is that the driver draws current from the power supply capacitor only during
the ON duration of the PWM cycle, but not during OFF duration. Therefore, the average current
withdrawn from power supply is considerably less than motor current. For example, two 3A motors can
be well supplied by one power supply of 4A rating.
Multiple Drivers:
It is recommended that multiple drivers share one power supply to reduce cost, provided that the supply
has enough capacity.
DO NOT
daisy-chain the power supply input pin of the drivers (connect them to
power supply separately) to avoid cross interference.
Higher supply voltage will allow higher motor speed to be achieved, at the price of more noise and heating.
If the motion speed requirement is low, it is better to use lower supply voltage to improve noise, heating and
reliability.
NEVER connect power and ground in the wrong way, it will damage the driver.
5.
Driver Voltage and Current Selection
This driver can match small-medium size step motors (NEMA 17, 23, 34 and 42).
To achieve good driving results, it is important to select supply voltage and output current properly.
Generally, supply voltage determines the high-speed performance of the motor, while output current
determines the output torque of the motor (particularly at lower speed).
Selecting Supply Voltage:
Higher supply voltage can increase motor torque at higher speeds; this is helpful for avoiding losing steps.
However, higher voltage may cause more motor vibration at lower speed, and it may also cause over-voltage
protection and even driver damage. Therefore, it is suggested to choose only sufficiently high supply voltage
for intended applications.
Setting Proper Output Current
For a given motor, higher driver current will make the motor to output more torque, but at the same time
causes more heating in the motor and driver. Therefore, output current is generally set to be such that the
motor will not overheat during lengthy operation.
Since parallel and serial connections of motor coils will significantly change resulting inductance and
resistance, it is important to set driver output current depending on motor phase current, motor leads and
connection methods. Phase current rating supplied by motor manufacturer is important in selecting
driver
current, but the selection also depends on leads and connection.
Astrosyn International Technology Ltd, The Old Courthouse, New Rd Ave, Chatham, Kent ME4 6BE, England
Tel: +44(0)1634 815175 Fax: +44(0)1634 826552