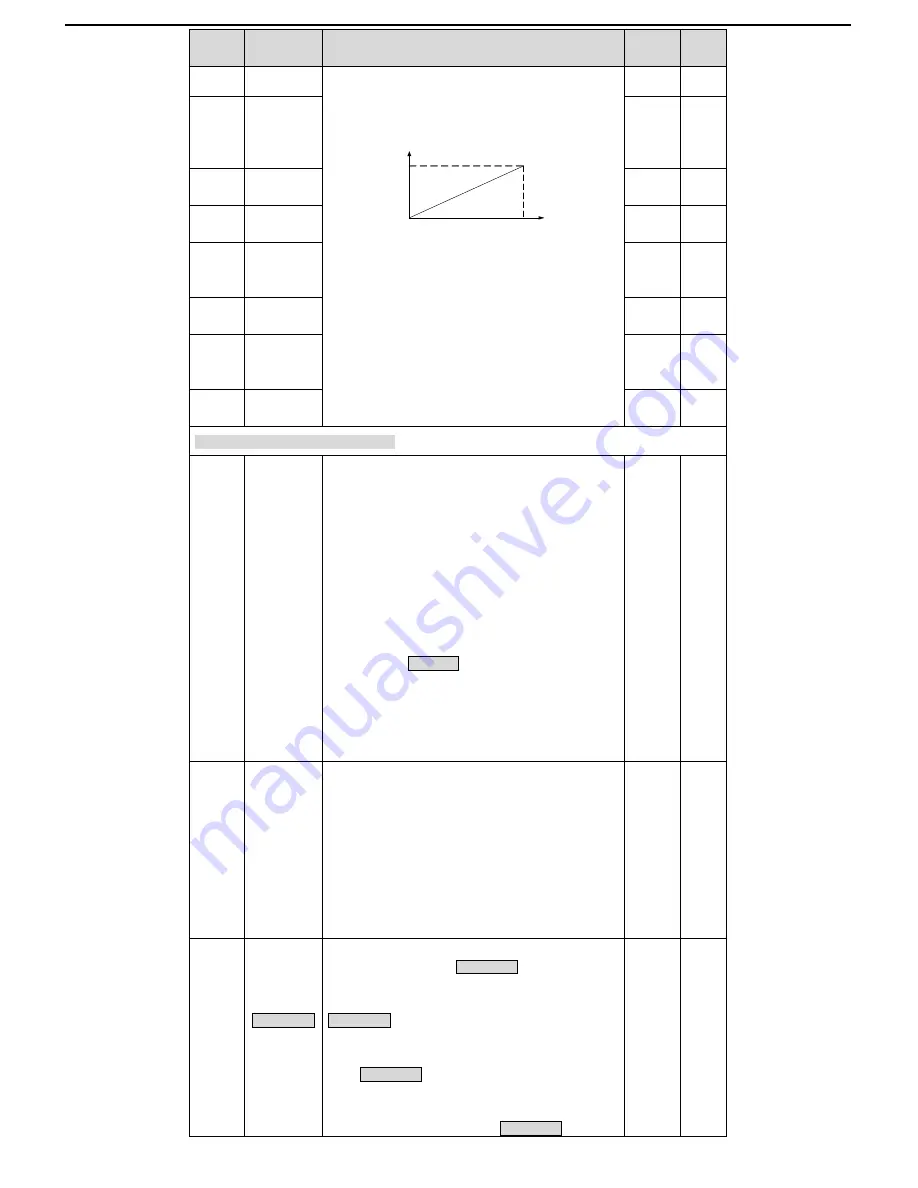
Astraada DRV-22 inverters Function Parameters
36
Function
code
Name
Detailed instruction of parameters
Default
value
Modify
AO1 output
0.5V.
In different cases, the corresponding analog output of 100%
of the output value is different. Please refer to each
application for detailed information.
10 V (20m A )
0.0%
10 0.0%
A O
Setting range of P06.17:-100.0%~ P06.19
Setting range of P06.18:0.00V~10.00V
Setting range of P06.19:P06.17~100.0%
Setting range of P06.20:0.00V~10.00V
Setting range of P06.21:0.000s~10.000s
Setting range of P06.22:-100.0%~ P06.24
Setting range of P06.23:0.00V~10.00V
Setting range of P06.24:P06.22~100.0%
Setting range of P06.25:0.00V~10.00V
Setting range of P06.26:0.000s~10.000s
P06.20
The
corresponding
AO1 output to
the upper limit
10.00V
○
P06.21
AO1 output
filter time
0.000s
○
P06.22
Lower limit of
AO2 output
0.0%
○
P06.23
Corresponding
AO2 output to
the lower limit
0.00V
○
P06.24
Upper limit of
AO2 output
100.0%
○
P06.25
Corresponding
AO2 output to
the upper limit
10.00V
○
P06.26
AO2 output
filter time
0.000s
○
P07 Group Human-Machine Interface
P07.00
User’s
password
0~65535
The password protection will be valid when setting any
non-zero number.
00000: Clear the previous user’s password, and make the
password protection invalid.
After the user’s password becomes valid, if the password is
incorrect, users cannot enter the parameter menu. Only
correct password can make the user check or modify the
parameters. Please remember all users’ passwords.
Retreat editing state of the function codes and the password
protection will become valid in 1 minute. If the password is
available, press PRG/ESC to enter into the editing state of
the function codes, and then “0.0.0.0.0” will be displayed.
Unless input right password, the operator can not enter into
it.
Note: Restoring to the default value can clear the
password, please use it with caution.
0
○
P07.01
Parameter
copy
0:No operation
1:Upload the local function parameter to the keypad
2:Download the keypad function parameter to local
address(including the motor parameters)
3:Download the keypad function parameter to local address
(excluding the motor parameter of P02 and P12 group)
4:Download the keypad function parameters to local
address (only for the motor parameter of P02 and P12
group)
Note: After finish 1~4, the parameter will restore to 0 and
the uploading and downloading does not include P29.
0
◎
P07.02
QUICK/JOG
function
selection
0:No function
1: Jogging running. Press QUICK/JOG to begin the jogging
running.
2: Shift the display state by the shifting key. Press
QUICK/JOG to shift the displayed function code from right
to left.
3: Shift between forward rotations and reverse rotations.
Press QUICK/JOG to shift the direction of the frequency
commands. This function is only valid in the keypad
commands channels.
4: Clear UP/DOWN settings. Press QUICK/JOG to clear the
1
◎
Summary of Contents for DRV-22
Page 81: ...Notes ...