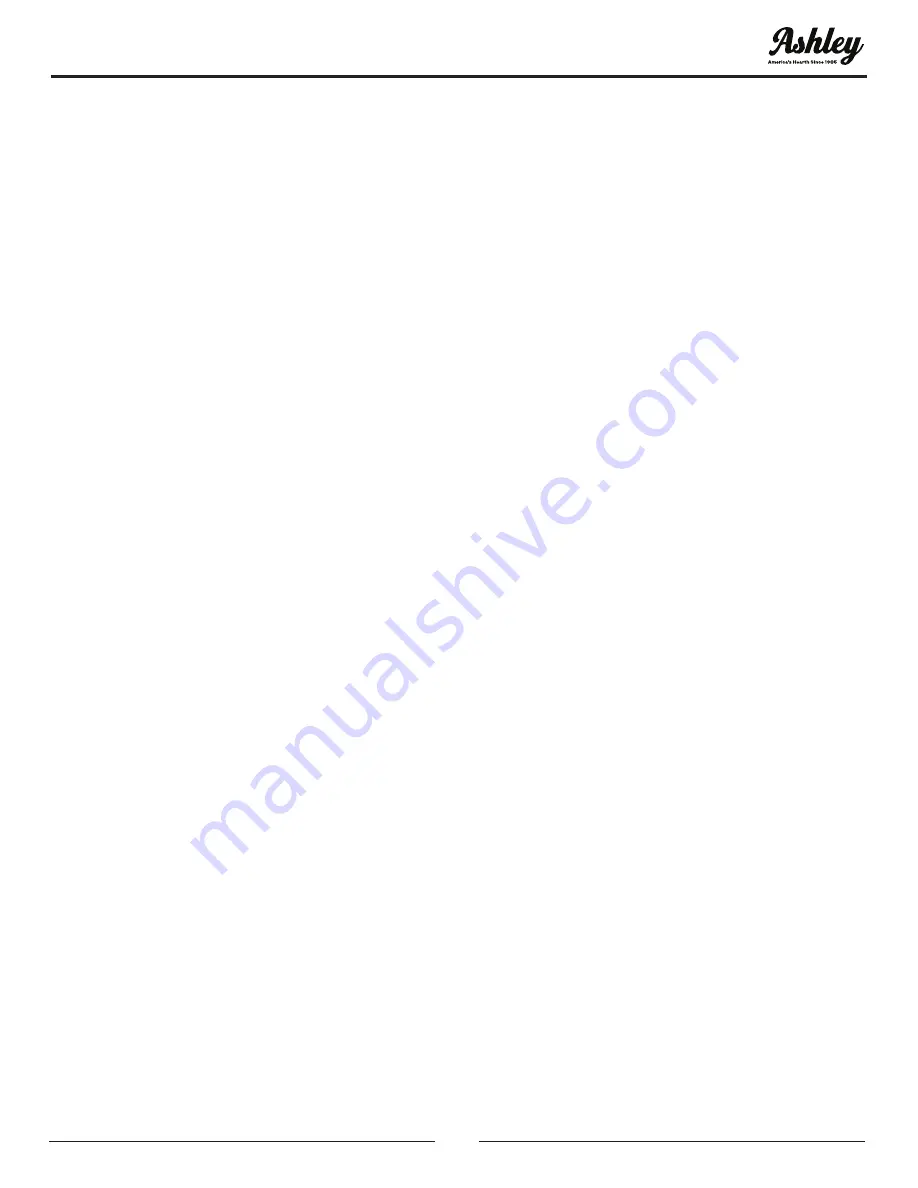
© 2021 United States Stove Company
7
spillage, and to maximize performance. Gauges to
measure draft are readily available at stove stores
and are economical to rent or purchase. Factors
such as wind, barometric pressure, trees, terrain and
chimney temperature can have an adverse effect
on the draft. The manufacturer cannot be held
responsible for external factors leading to less than
optimal drafting. Should you have a problem with
inadequate draft, you should contact a licensed
heating and cooling contractor for assistance in
solving the problem.
FIREPLACE CONDITION AND ZERO
CLEARANCE REQUIREMENTS
A masonry fireplace must meet minimum code
requirements, National Fire Protection Association,
(NFPA) 211, or the equivalent for a safe installation.
Contact a professional, licensed installer, your local
building inspector or the local fire authority for the
requirements in your area. Your insurance company
should be able to recommend a qualified inspector.
Inspections should include the following:
1.
Condition of the fireplace and chimney. A
masonry fireplace and chimney MUST be
inspected prior to installation of this appliance.
They must be free from cracks, loose mortar,
creosote deposits, blockage or other evidence
of deterioration. If found, these items MUST be
repaired prior to installation. DO NOT REMOVE
BRICKS or MORTAR from existing fireplace
when installing this unit.
2.
Chimney Size. Minimum chimney size is 6” (153
mm) diameter. Maintain a 15 ft. minimum overall
chimney height measured from the top of
appliance to the top of the chimney. Chimneys
must extend at least 3 ft. above the roof and at
least 2 ft. above the highest point within 10 ft. of
the chimney top. See the Chimney Connections
section of this manual.
3.
Zero Clearance or Metal Heatform Fireplaces.
These fireplaces and chimneys must meet
the minimum code specifications as noted
above. Factory built zero clearance fireplaces
must be listed and suitable for solid fuel use.
Chimneys must be at least 7 inch diameter to
accommodate a required, continuous, stainless
steel liner from the appliance’s flue collar
to the top termination of the chimney. Only
detachable parts that can be easily replaced (i.e.
damper parts, screens, doors and side, and back
refractory panels) are to be removed. These
parts must be stored and readily available for
replacement if the appliance is ever removed.
The removal of any parts that render the
fireplace unusable for burning solid fuel
requires a permanent label to be affixed by the
installer that states the fireplace is unsuitable
for burning solid fuel unless the missing parts
are replaced and the fireplace is restored to its
original, certified condition.
4. Chimney Caps. Mesh type chimney caps and
spark arrestors must be able to be removed for
regular inspection and cleaning. Otherwise the
mesh should be removed to prevent possible
plugging. Check your local fire and building
codes.
5. Chimney Liner. The chimney must be suitable
for burning solid fuel. Install a continuous
stainless steel liner from the flue collar of the
appliance to the top of the chimney. Liner must
be UL Listed to UL1777.
6.
Combustible Material Clearances. The fireplace
and chimney must be inspected to make sure
there is adequate clearance to combustible
materials. This includes the top, side, front,
and back as well as concealed combustibles
in the chimney and mantle areas. Your local
building inspector or fire authority should have
information on whether older fireplace meet
current codes and are suitable for use.
7.
Makeup Air Requirements. This appliance
requires an adequate supply of makeup air to
operate safely and efficiently. In some areas, this
is a building code requirement. Inadequate air
supply will cause poor combustion, inefficient
operation, creosote buildup, back drafting and
smoke puffing into the living areas. If any of the
following conditions are evident, a makeup air
supply MUST be installed.
a.
Existing fuel-fired equipment shows evidence
of back puffing, smoke roll-out, inefficient
operation, or excessive smell in the living area.
b. Opening a window or door alleviates any of the
above problems or symptoms.
c. The building is constructed with a well-sealed
vapor barrier, tight fitting windows, or has
powered exhaust fans.
d. Excessive condensation on windows in the
winter.
e. The building has a ventilation system installed.
INSTALLATION