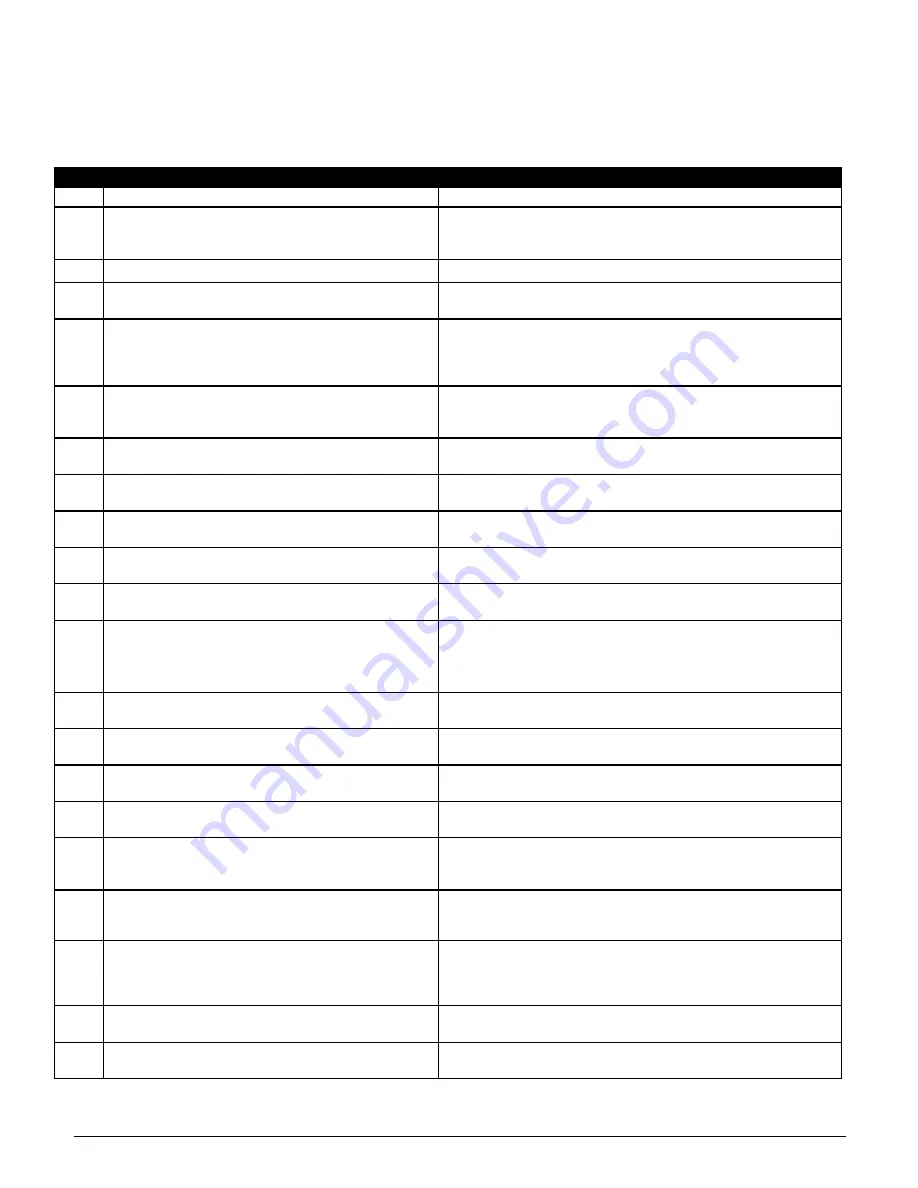
North America • Latin America • India • Europe / Middle East / Africa • China • Pacific Rim
armstrong
international.com
Designs, materials, weights and performance ratings are approximate and subject to change without notice. Visit
armstrong
international.com for up-to-date information.
42
*Codes may appear with an A, B, or C as a suffix denoting the number of times the code has appeared since the last Initialization
(INI). Some SLO’s are accompanied by a reduction of the maximum firing rate; A=80%, B=50%, C=30%. After the C suffix appears,
the next code of that kind becomes an HLO (manual reset required).
Table 7.2 BCB Soft Lock Out (SLO) Codes
Code
Cause
Recommended Action
A1*
Excessive pressure differential (
∆
P) on water side of heat exchanger
Check for scaling or blockage on water side of heat exchanger, also check pump
performance. If this SLO is indicated while the unit is firing, it is doing so at a
reduced BTU input; low enough to stay below that maximum
∆
P set point.
B01
Pressure too high at condensate drain connection during Stand By
Look for condensate backing up into combustion side of heat exchanger.
B02
Pressure too high at condensate drain connection during pre-purge
Insure condensate drain system is flowing freely, and vent is clear of obstructions.
Also, be sure the Z-INI has been initiated.
B03
Pressure too low at condensate drain connection during pre-purge
Check for condensate (water) in the condensate neutralizer (if equipped) or
the condensate trap at appliance outlet. If it is dry, add water to form trap. The
appliance also will initiate an auto-filling process for the condensate trap, indicated
on the screen during this operation. Also, be sure the Z-INI has been initiated.
B04
Pressure at flue/condensate sensor is too low
Check flue gas vent connection or sensor connection located at condensate drain
line. Also check for a disconnected or open condensate drain line and last, look for
a leak in the heat exchanger outer casing (behind the insulation).
DW7*
Temperature rise (
∆
T) through heat exchanger is too high
Unit is operating at a reduced BTU input - check for scaling or blockage on water
side of heat exchanger, also check pump performance.
FL05*
Flue gas temperature too high
Unit is burning at a reduced BTU input rate. The cause of the high flue gas
temperature should be investigated and corrected ASAP
FL09*
Fouling of the fire side of the heat exchanger
Unit is burning at a reduced BTU input rate. A combustion side inspection and
cleaning should be scheduled ASAP.
FL13
Flue gas sensor (T5) fault (not connected or open status)
Check the condition of the connectors and wires from the card edge connector at
the board to the flue gas sensor on the appliance.
FL14
Flue gas sensor (T5) fault (short circuit status)
Take an OHM reading at the connector on the flue gas sensor - compare it to the
chart on page 47 replace if out of range.
G01*
Gas supply pressure too low
If this occurs at the beginning of an ignition cycle, this SLO will stay until the
pressure is high enough for proper ignition. If this occurs while the unit is firing,
and it continues to fire, it is doing so at a reduced BTU input low enough to stay
above that minimum pressure set point.
H01
Outlet sensor (T1.1, 1.2) fault (not connected or open status)
Check the condition of the connectors and wires from the card edge connector at
the board to the outlet sensor on the appliance.
H02
Inlet sensor (T2) fault (not connected or open status)
Check the condition of the connectors and wires from the card edge connector at
the board to the inlet sensor on the appliance.
H04
Outlet sensor (T1.1, 1.2) fault (short circuit status)
Take an OHM reading on the outlet sensor - compare it to the chart on page 47
replace if out of range.
H05
Inlet sensor (T2) fault (short circuit status)
Take an OHM reading on the inlet sensor - compare it to the chart on page 47
replace if out of range.
H07/09 Calibration between inlet (T2) and outlet (T1) water temperature
sensors indicates too great a differential.
Test both sensors against the actual temperature and OHMs as shown in the chart
on page 47, replace as required. The appliance will continue to operate, but at a
reduced input until the required correction has been resolved.
H11
High
∆
T
See Coil Anti-scaling Prevention, page 52
H24*
High Limit set point has been exceeded
Appliance restarts, but at a reduced input; after 3 restarts, the appliance gets
a Manual Lock Out (HLO) and needs the cause resolved immediately. Possible
causes are high
∆
T, temperature setpoint versus high limit setting too close or bad
sensor.
ID01
First INI process data missing
Run the Z-INI; starting Initialization numbers must be tested and the saved for all
connected sensors in a number of conditions.
ID02
EMB EEPROM fault (2)
Reset the fault, cycle power on and off, if the fault reappears, the EMB–EEPROM is
corrupted.
Servicing - continued