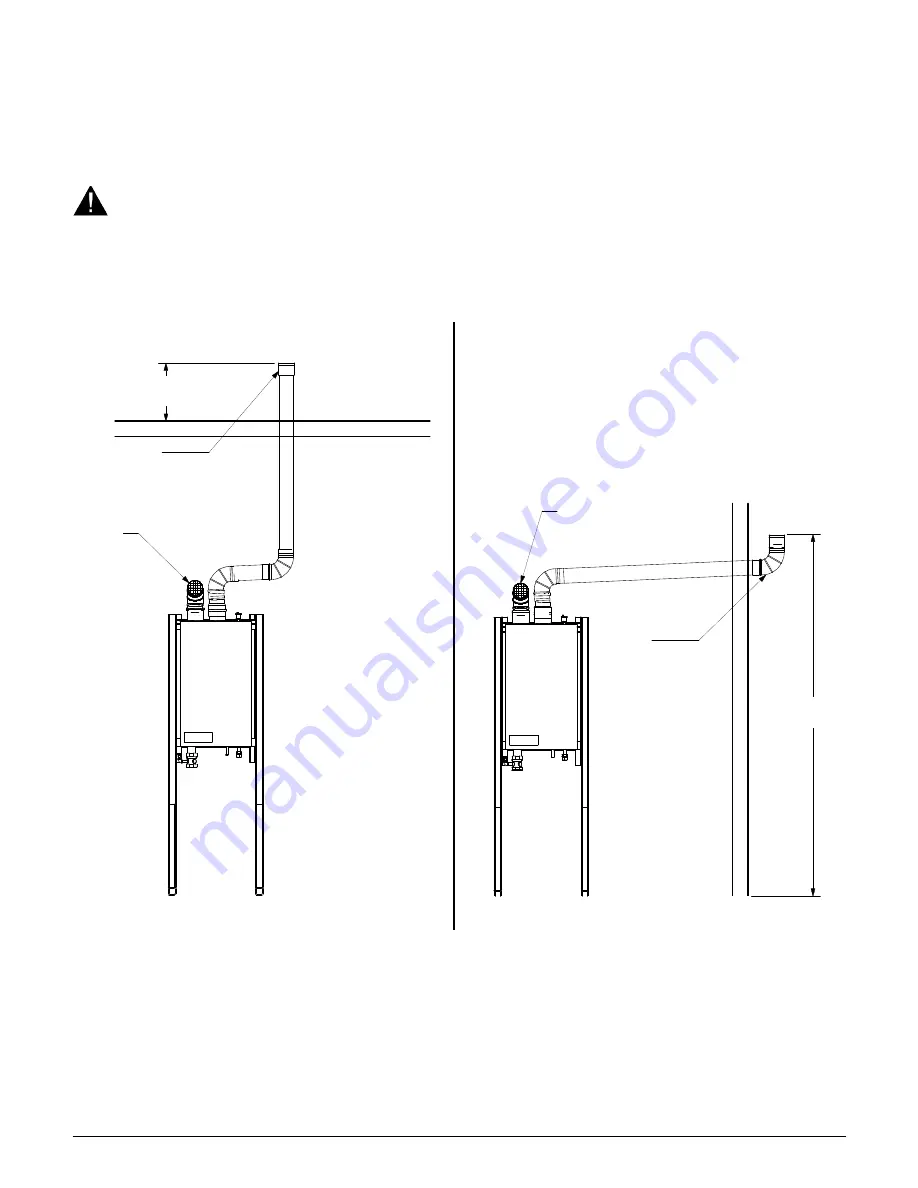
North America • Latin America • India • Europe / Middle East / Africa • China • Pacific Rim
armstrong
international.com
Designs, materials, weights and performance ratings are approximate and subject to change without notice. Visit
armstrong
international.com for up-to-date information.
25
Diagrams For Room Air Venting Termination
3/4"=1'
Reference dimensions are ± 10%
All dimensions are ± 1"
Custom
Dwg No.
Customer / Job name:
Scale:
Description:
Drawn/
Revised by:
Checked/
Apv. by:
Revision:
MM/DD/YY
Date:
1/4" per ft. slope to appliance
All horizontal runs must be
supported every 24"
(609mm)
Air intake
90º Elbow with
Bird Screen
Exhaust
90º Elbow with
Coupler & Bird Screen
24" (609mm) or
12" (305mm) above
maximum snow level,
whichever is greater
If you’re using room air, your unit should be set up this way:
NOTE: Stated efficiencies are based on ducted air; using room air may effect efficiency.
R
Re
effe
er
re
en
nc
ce
e d
diim
me
en
ns
siio
on
ns
s a
ar
re
e ±
± 1
10
0%
%
A
Allll d
diim
me
en
ns
siio
on
ns
s a
ar
re
e ±
± 1
1"
"
MM/DD/YY
MM/DD/YY
3/4"=1'
Custom
Dwg No.
Scale:
Description:
Date:
Drawn/
Revised by:
Checked/
Apv. by:
Revision:
Description:
Date:
Drawn/
Revised by:
Checked/
Apv. by:
Revision:
Customer / Job name:
04/02/10
AJT
1/4" per ft. slope to appliance
All horizontal runs must be
supported every 24"
Exhaust
90º Elbow with
Coupler & Bird Screen
24"
(609mm)
or
12"
(305mm)
above
Maximum snow level
whichever is greater
Air intake
90º Elbow with
Bird Screen
Figure 4.5 - Vertical Termination
Figure 4.6 - Sidewall Termination
As long as the boiler room remains under a positive pressure under all operating conditions of the building, this is a perfectly
acceptable option. Generally, all this requires is an external free air source; typically just two properly sized openings to the outdoors.
Installations done in this manner must comply with ANSI Z223.1, NFPA 54—National Fuel Gas Code 2009 section 9.3, and any
specific local codes that may require additional combustion air be provided. For the latest edition, see Technical Bulletin–TB 003.
This would be our preferred alternate to our standard manual specifications.
Venting - continued
CAUTION! Flue Gas will condense as it exits the vent termination. This condensate can
freeze on exterior building surfaces which may cause discoloration of these surfaces.
Consideration should be given to the plume of condensation that exits the exhaust which
may affect the cosmetic appearance of the building.