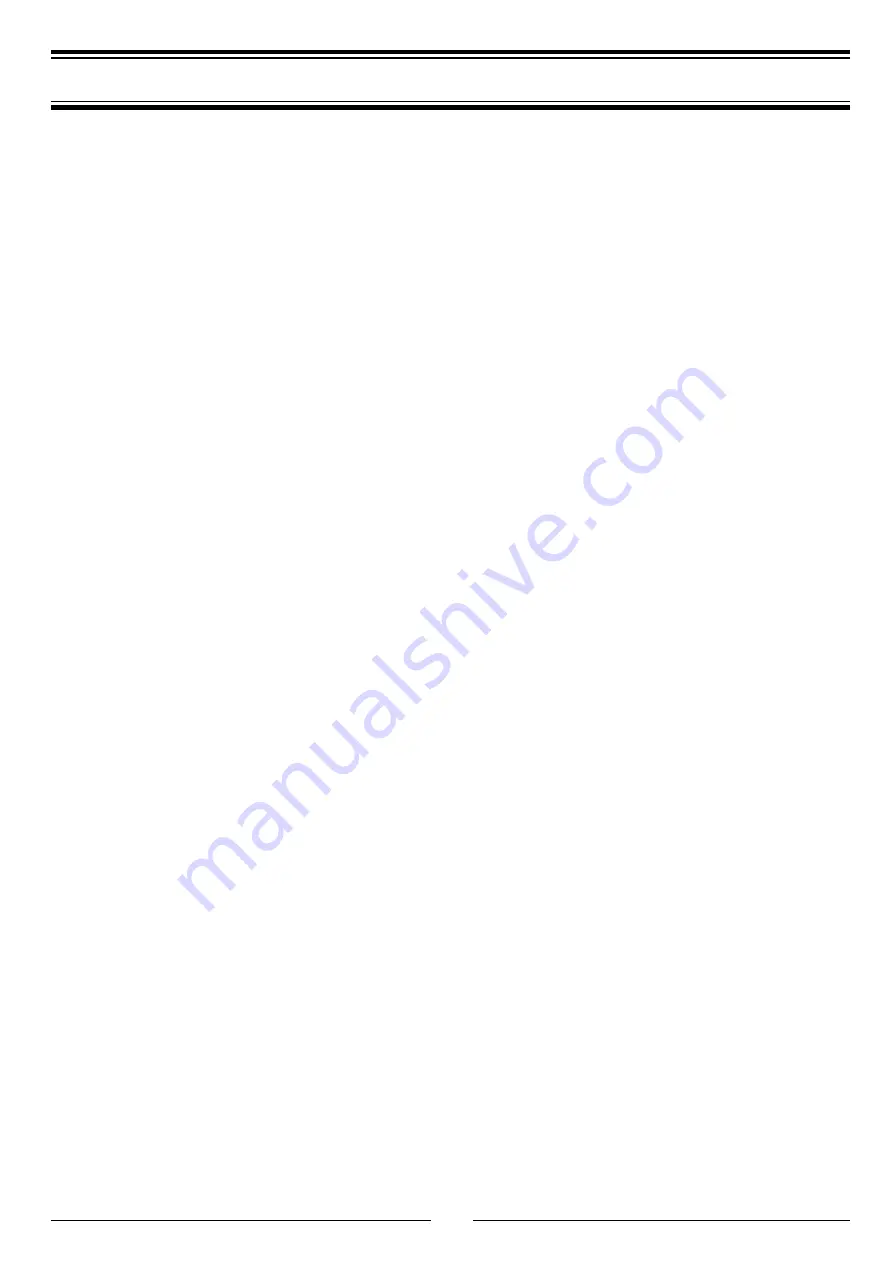
8
6. INSTALLATION
6.1
Reference Standards
The technical information and instructions provided herein below
are intended for the installer / Ser vicing Technician so that the
unit may be installed and serviced correctly and safely.
In the United Kingdom the installation and initial star t up of the
boiler must be b y a CORGI Registered Installer in accordance
with the installation standards currently in eff ect, as well as with
any and all local health and safety standards i.e. CORGI.
In the Republic of Ireland the installation and initial start up of the
appliance must be carried out by a Competent Person in accor-
dance with the current edition of I.S
.813 “Domestic Gas
Installations”, the current Building Regulations , reference should
also be made to the current ETCI rules for electrical installation.
This appliance must be installed by a competent installer in
accordance with current Gas Saf ety (installation & use)
Regulations.
The installation of this appliance m ust be in accordance with the
relevant requirements of the Local Building Regulations , the cur-
rent I.E.E. Wiring Regulations, the b ylaws of the local w ater
authority, in Scotland, in accordance with the Building Standards
(Scotland) Regulation and Health and Saf ety document No. 635
“Electricity at w ork regulations 1989” and in the Repub lic of
Ireland with the current edition of I.S . 813, the Local Building
Regulations (IE).
C.O.S.H.H.
Materials used in the manufacture of this appliance are non-haz-
ardous and no special precautions are required when ser vicing.
Installation should also comply with the following British Standard
Codes of Practice
The appliance ma y be installed in an y room or indoor area,
although particular attention is dr awn to the requirements of the
current I.E.E. Wiring Regulations, and in Scotland, the electr ical
provisions of the Building Regulations applicab le in Scotland,
with respect to the installation of the combined appliance in a
room containing a bath or sho wer, the location of the boiler in a
room containing a bath or sho wer should only be considered if
there is no alternative.
Where a room-sealed appliance is installed in a r oom con-
taining a bath or sho wer the appliance and an y electrical
switch or appliance contr ol, utilising mains electricity
should be situated so that it cannot be touc hed by a person
using the bath or sho wer, specifically in accor dance with
current IEE Wiring Regulations.
The location m ust permit adequate space f or servicing and air
circulation around the appliance as indicated in Section 6.4.
The location must permit the provision of an adequate flue and
termination.
For unusual locations special procedures may be necessary.
BS 6798-1987 gives detailed guidance on this aspect.
A compartment used to enclose the appliance must be designed
specifically for this purpose. No specific ventilation requirements
are needed for the installation within a cupboard.
This appliance is not suitable for outdoor installation.
The type C appliances (in whic h the combustion circuit, air
vent intake and comb ustion chamber are air -tight with
respect to the room in which the appliance is installed) can
be installed in any type of room.
Secondary ventilation is not required with this boiler . The boiler
must be installed on a solid, non-comb ustible, permanent wall to
prevent access from the rear.
BS 7593:1992
Treatment of water in domestic hot water
central heating systems
BS 5546:1990
Installation of hot water supplies for
domestic purposes
BS 5440-1:2000 Flues
BS 5440-2:2000 Air supply
BS 5449:1990
Forced circulation hot water systems
BS 6798:1987
Installation of gas fired hot water boiler s
of rated input not exceeding 60kW
BS 6891:1989
Installation of low pressure gas pipe up to
28mm
BS 7671:2001
IEE wiring regulations
BS 4814:1990
Specification for expansion vessels
BS 5482:1994
Installation of L.P.G.
6.2
Siting the Appliance
Summary of Contents for INTESA TP23
Page 44: ...44 Fault Finding...
Page 45: ...45 Fault Finding...
Page 46: ...46 Fault Finding 0 55mbar 23kW 0 90mbar 30kW 0 55mbar 23kW 0 90mbar 30kW...
Page 47: ...47 Fault Finding...
Page 50: ...50...
Page 51: ...51...