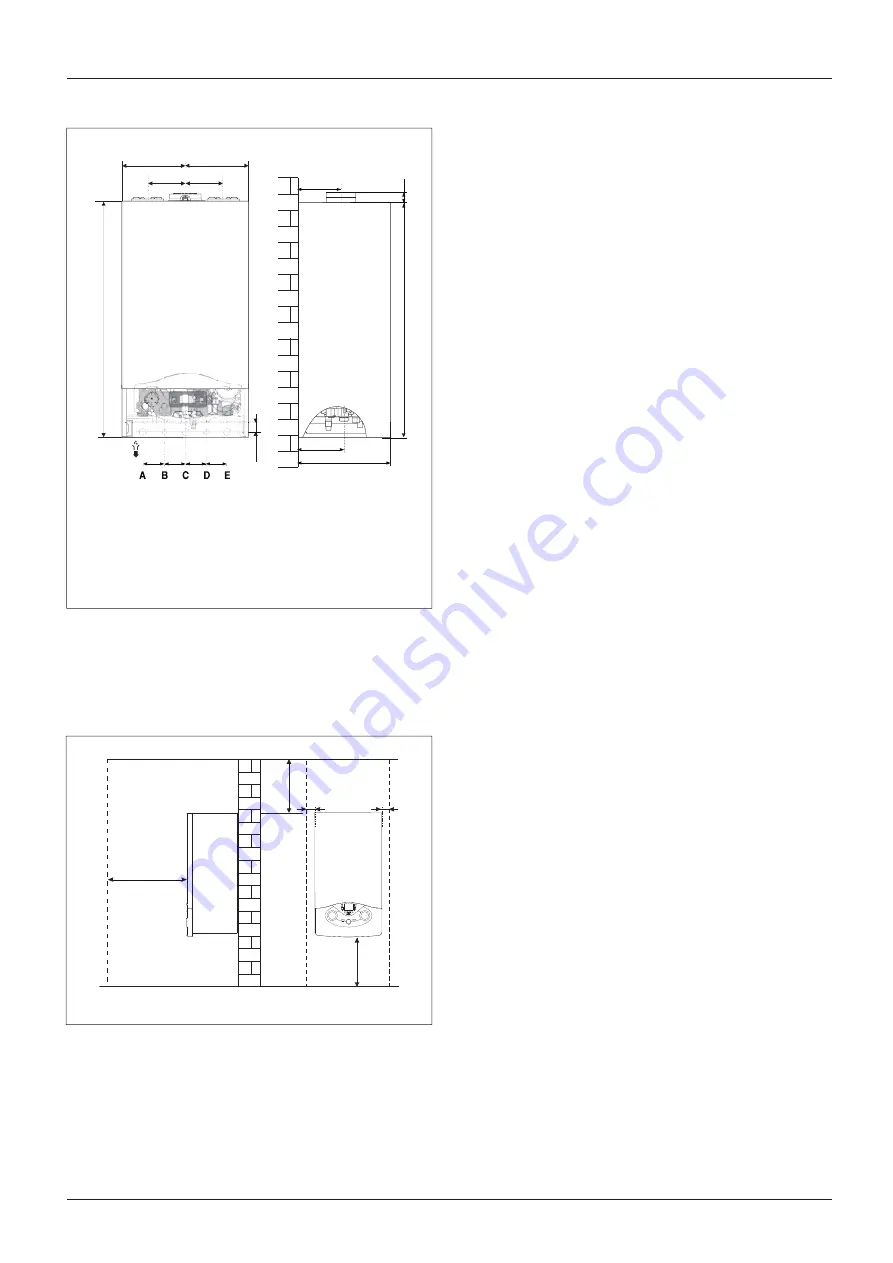
8
2. product description
2.4 Overall Dimensions
A. Central Heating Flow
B. Domestic Hot Water Outlet
C. Gas Inlet
D. Domestic Cold Water Inlet
E. Central Heating Return
450
0 0
3
0 0
3
50 50
2.5 Minimum clearances
In order to allow easy access to the boiler for maintenance
operations, The boiler must be installed in accordance with
the clearances stated below.
5
166
319
180
25
745
28
745
200
120 120
200
65
L
65
67 67
Fig. 2.4
Fig. 2.5
5
Summary of Contents for EGIS HE 24
Page 63: ......