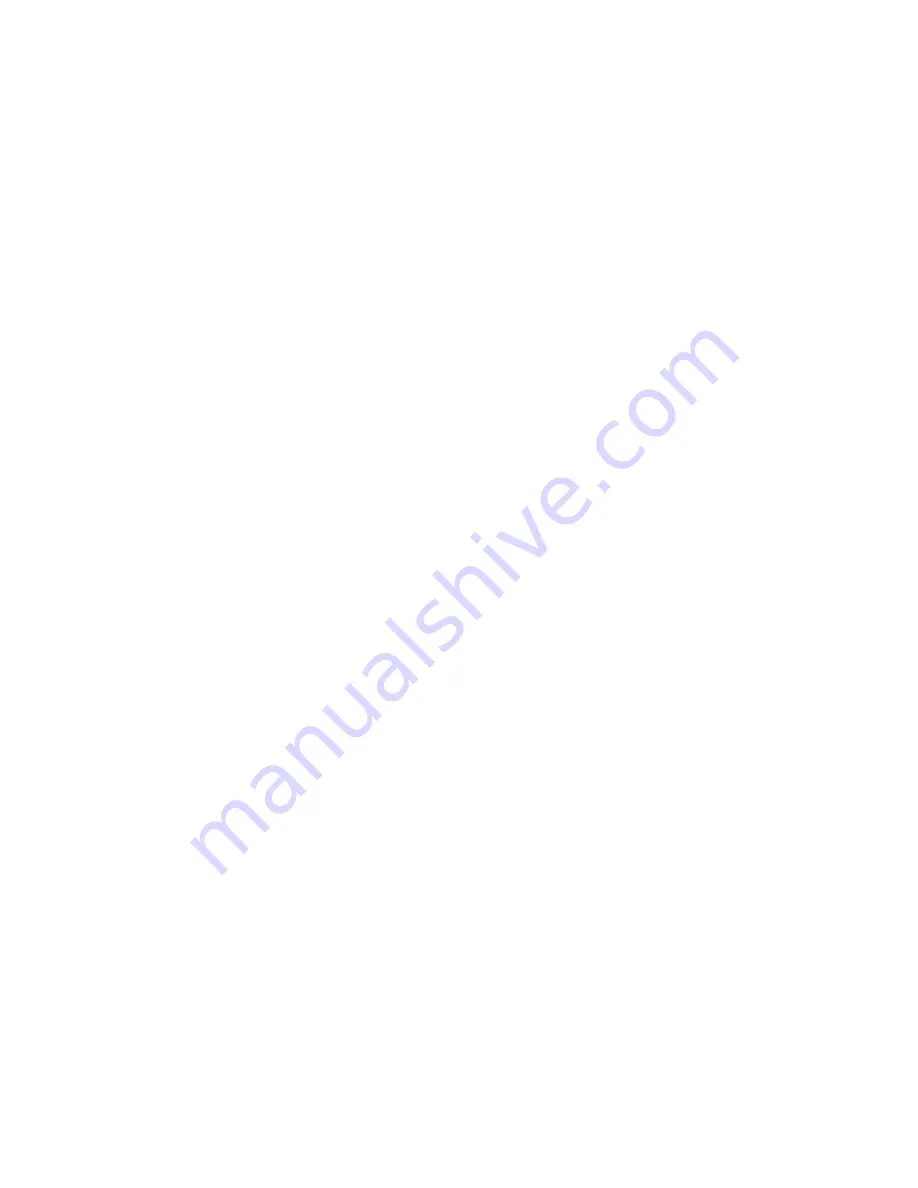
: JGW, JGR
AND
JGJ
S
ECTION
4 - L
UBRICATION
AND
V
ENTING
PAGE 4 - 7
rates must be recalculated and hardware changes may be necessary to the force-feed lubri-
cation system. Consult the following table and your Packager or Ariel.
To set the proper force-feed lubricator pump flow rate, the cycle time indicator on the distri-
bution block is to be observed. To determine cycle time, time the cycle from flash to flash for
a digital no-flow timer switch (DNFT); or time the cycle from initial movement of the indicator
pin at the fully retracted position, to the time when the pin returns to the fully retracted posi-
tion and begins to move back out again for a magnetic cycle indicator assembly.
NOTE: WHEN ADJUSTING THE FORCE FEED LUBRICATION PUMP SETTING FOR
THE APPROPRIATE CYCLE TIME, DO NOT SET THE FLOW RATE TOO LOW.
THE PUMPS CAN BECOME INCONSISTENT WHEN SET TOO LOW.
The force feed lubrication pumps should be capable of delivering 150% minimum of the
“normal” required lube rate for the break in period (set as close as possible to twice the “nor-
mal” rate for 200 hours). Please contact Ariel for assistance if the existing pump is not capa-
ble of the minimum flow rate required.
Used engine oil may be used as long as the new oil specifications meet the listed require-
ments, and the oil is appropriately filtered (i.e. 20 micron nominal). Oil viscosity must be
monitored and tested, as follows, for serviceability.
Oil should be changed at regular maintenance intervals (6 months or 4,000 hours), when oil
filter differential pressure exceeds 10 psi (0.7 Bar) for spin-on filters or when oil sample
results indicate the need. A more frequent oil change interval may be required if operating in
an extremely dirty environment or if the oil supplier recommends it. Oil sampling should be
performed on a regular basis to verify suitability of oil for continued service. Degradation to
the next lower viscosity grade below the original viscosity or an increase in viscosity to the
next higher grade requires a complete oil change. Viscosity testing should be performed at
212°F (100°C).
The use of higher viscosity lubricants or specially compounded lubricants can compensate
somewhat for the presence of liquids in the gas stream.
NOTE: WHEN THERE ARE LIQUIDS PRESENT IN THE GAS, THE MOST EFFECTIVE
LUBRICATION OF CYLINDERS AND PACKING REQUIRES REMOVAL OF THE
LIQUIDS BEFORE THE GAS ENTERS THE COMPRESSOR.
THESE LUBRICATION RECOMMENDATIONS ARE GENERAL GUIDELINES. IF
THE RECOMMENDED LUBRICANTS OR FLOW RATES DO NOT APPEAR TO
WORK ADEQUATELY, FLOW RATES AND/OR LUBRICANT TYPES MAY NEED
TO BE CHANGED. PLEASE CONTACT THE LUBRICANT SUPPLIER FOR SPE-
CIFIC LUBRICANT RECOMMENDATIONS.
WARRANTY OF COMPONENT FAILURES WHICH OCCUR WHILE USING
LUBRICANTS WHICH DO NOT MEET THESE SPECIFICATIONS WILL BE SUB-
JECT TO REVIEW ON A CASE BY CASE BASIS.
Summary of Contents for JGJ Series
Page 30: ...FOR MODELS JGW JGR AND JGJ SECTION 1 DESIGN SPECIFICATIONS DATA PAGE 1 24 1 01 NOTES ...
Page 34: ...FOR MODELS JGW JGR AND JGJ SECTION 2 INSTALLATION PAGE 2 4 1 01 NOTES ...
Page 44: ...FOR MODELS JGW JGR AND JGJ SECTION 3 START UP PAGE 3 10 1 01 NOTES ...
Page 114: ...FOR MODELS JGW JGR AND JGJ SECTION 5 MAINTENANCE PAGE 5 42 1 01 NOTES ...
Page 120: ...FOR MODELS JGW JGR AND JGJ SECTION 6 TECHNICAL ASSISTANCE PAGE 6 6 1 01 NOTES ...
Page 130: ...FOR MODELS JGW JGR AND JGJ SECTION 7 APPENDICES PAGE 7 10 1 01 NOTES ...
Page 135: ......
Page 136: ......
Page 137: ......
Page 138: ......
Page 139: ......
Page 140: ......
Page 141: ......