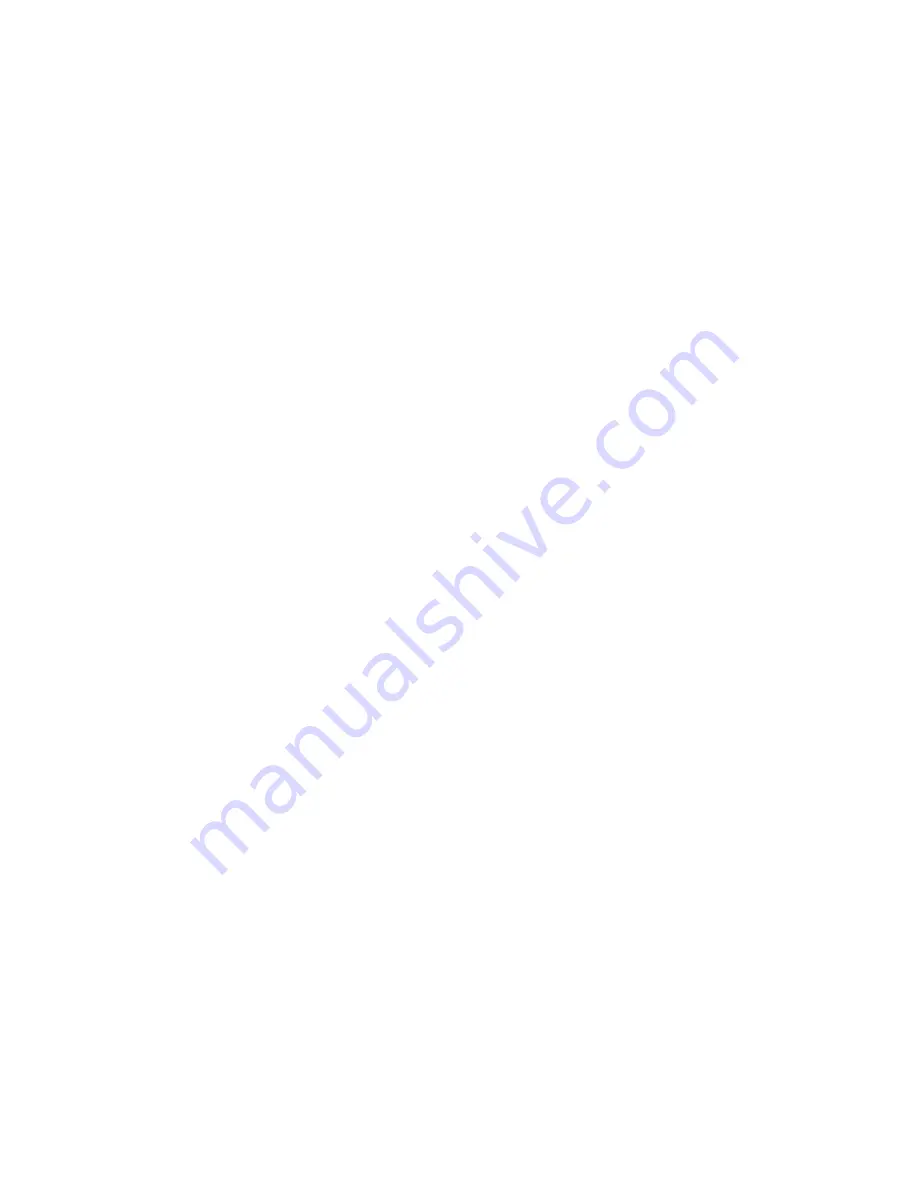
S
ECTION
6 - T
ECHNICAL
A
SSISTANCE
PAGE 6 - 3
3.
Inspect valves for broken plates and loose center bolts, replace broken parts
and tighten center bolts to torque values listed in Table 1-12 on page 1-18.
4.
Inspect cylinder bores for damage or wear. If gouged, so that the total cross sec-
tional area of the gouges is greater than 0.001 square inches per inch of cylinder
circumference (0.025 mm
2
/mm of cylinder circumference), cylinder should be
replaced or re-bored to a maximum of 0.020 inches (0.50 mm) oversize. The cyl-
inder should also be replaced or re-bored if the bore is more than 0.001 inches
per inch of cylinder diameter (0.001m/m of cylinder diameter) out of round or
tapered.
NOTE: REBORING REMOVES NITRIDED SURFACE OF CYLINDER BORE. CONTACT
ARIEL FOR RE-NITRIDING.
5.
Inspect piston ring end gap. Replace rings that are outside the maximum limit
listed in Table 1-7, Table 1-8, Table 1-9 and Table 1-10.
6.
Inspect piston rods for damage and excessive wear. If gouged or scratched,
replace the rod. If the rod is more than 0.005 inches (0.13 mm) under size, out of
round more than 0.001 inches (0.03 mm), or tapered more than 0.002 inches
(0.05 mm), replace the rod.
7.
Rebuild cylinder packing cases.
8.
Inspect for frame twist or bending by checking shimming of compressor feet.
9.
Realign if necessary to hold coupling alignment within 0.005 inches (0.13 mm)
TIR.
10. Check and re-calibrate all temperature and pressure gauges.
11. Check and record compressor rod run out.
12. Grease VVCP stem threads at grease fitting, with 2 to 3 pumps of multi-purpose
grease using a standard hand pump grease gun.
13. Clean crankcase breather filter.
14. Adjust drive chains.
15. Pressure test the distribution block(s).
Every 2 Years or 16,000 Hours (plus Daily/Monthly/6 months/yearly)
1.
Check auxiliary end chain drive for sprocket teeth undercutting and chain for
excessive stretching.
2.
Rebuild oil wiper cases.
Every 4 Years or 32,000 Hours (plus Daily/Monthly/6 Months/1/2 Years)
1.
Check main and connecting rod bearing clearances by using an indicator and a
pry bar. Disassembly to check clearances is not recommended. Disassembly
should be performed if the pry bar check indicates excessive clearance.
2.
Check crosshead guide clearances with feeler gauges.
3.
Check crosshead pin to crosshead pin bore and connecting rod bushing bore by
removing crosshead pins.
4.
Check for excessive wear in the auxiliary end drive chain tightener.
Summary of Contents for JGJ Series
Page 30: ...FOR MODELS JGW JGR AND JGJ SECTION 1 DESIGN SPECIFICATIONS DATA PAGE 1 24 1 01 NOTES ...
Page 34: ...FOR MODELS JGW JGR AND JGJ SECTION 2 INSTALLATION PAGE 2 4 1 01 NOTES ...
Page 44: ...FOR MODELS JGW JGR AND JGJ SECTION 3 START UP PAGE 3 10 1 01 NOTES ...
Page 114: ...FOR MODELS JGW JGR AND JGJ SECTION 5 MAINTENANCE PAGE 5 42 1 01 NOTES ...
Page 120: ...FOR MODELS JGW JGR AND JGJ SECTION 6 TECHNICAL ASSISTANCE PAGE 6 6 1 01 NOTES ...
Page 130: ...FOR MODELS JGW JGR AND JGJ SECTION 7 APPENDICES PAGE 7 10 1 01 NOTES ...
Page 135: ......
Page 136: ......
Page 137: ......
Page 138: ......
Page 139: ......
Page 140: ......
Page 141: ......