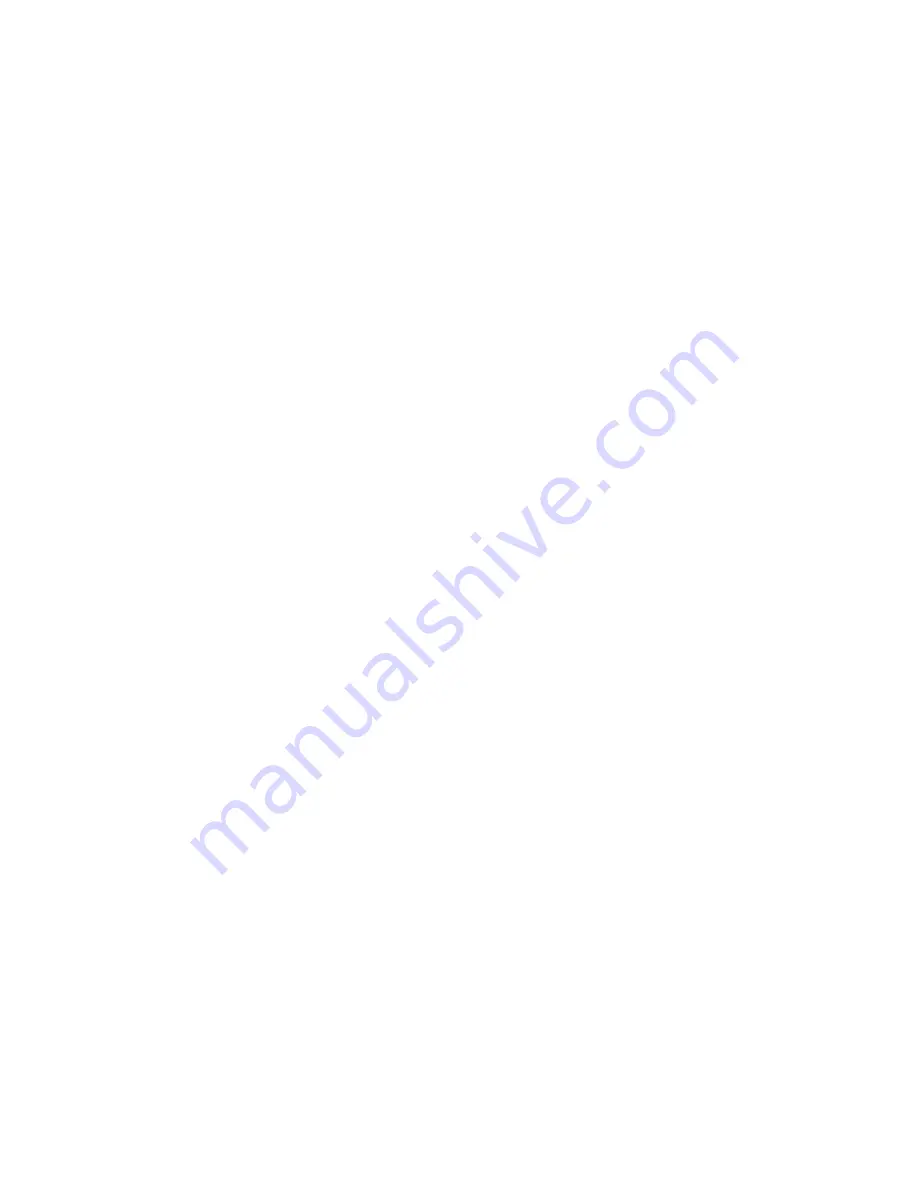
F
OR
M
ODELS
: JGI, JGM, JGN, JGP
AND
JGQ
S
ECTION
4 L
UBRICATION
PAGE 4-15
Oil Maintenance
Compressor frame lubricating oil should be changed as indicated in the regular maintenance
intervals or with a filter change or when oil analysis results indicate the need. A more fre-
quent oil change interval may be required if operating in an extremely dirty environment
without sampling and analysis or if the oil supplier recommends it.
Oil Sampling
Oil samples should be collected on a regular basis and analyzed to verify suitability of oil for
continued service. Consistent oil analysis can identify when to change the oil on the basis of
need rather than on a scheduled interval. Depending on the service, the length of time
between oil changes can be significantly extended through oil analysis. Oil analysis should
include:
•
Viscosity testing should be performed at 100°F (40°C) and 212°F (100°C). This is to
be sure that the oil has not mixed with cylinder oils or process gas.
•
Particle counting to the latest version of ISO 4406.
•
Spectroscopy to determine wear metals, contaminants, and additives.
•
FTIR (Fourier Transform Infrared Spectroscopy) to check for oxidation, water or cool-
ant contamination, and additive depletion. This is more important if a separate lube oil
is used for the force feed system.
Oil System Cleanliness
The compressor frame oil piping system and components are to be free of foreign matter
including, but not limited to dirt, sand, rust, mill scale, metal chips, weld spatter, grease and
paint. It is recommended that a commercial pipe cleaning service be used to clean the oil
piping system. If that is not practical, proper cleaning procedures using cleaners, acids, and/
or mechanical cleaning are to be used to meet the cleanliness requirements. Cleaning by-
products are to be properly disposed; a disposal service is recommended. It is also recom-
mended that all oil-piping systems be flushed using an electric or pneumatic driven pump
and filtered clean production oil. All compressor frame cavities are thoroughly cleaned prior
to assembly and compressors are test run with a filtered closed loop lube system at the Ariel
factory.
Note:
Ariel recommends that the lube oil piping downstream of the installed oil filter
not be disturbed as contaminants that enter that piping or open ports will be
flushed into the bearings causing catastrophic damage. If the piping must be
removed or altered, great care must be taken to cover the inlets to the oil gal-
leRy, the ends of the piping, and the filter outlet so that no contaminants may
enter. Before reinstallation, chemical and mechanical cleaning is required.
The pipe must then be flushed in accordance with Ariel’s stated cleanliness
requirements.
For all compressors that are installed with an electric or pneumatic powered pre-lube pump,
which have less than 50 feet (15 m) of oil piping are to be flushed as follows, prior to starting
the compressor. The cooler oil passages are to be included in the flushing loop. Oil systems
for compressors without an electric or pneumatic powered pre-lube pump, which have less