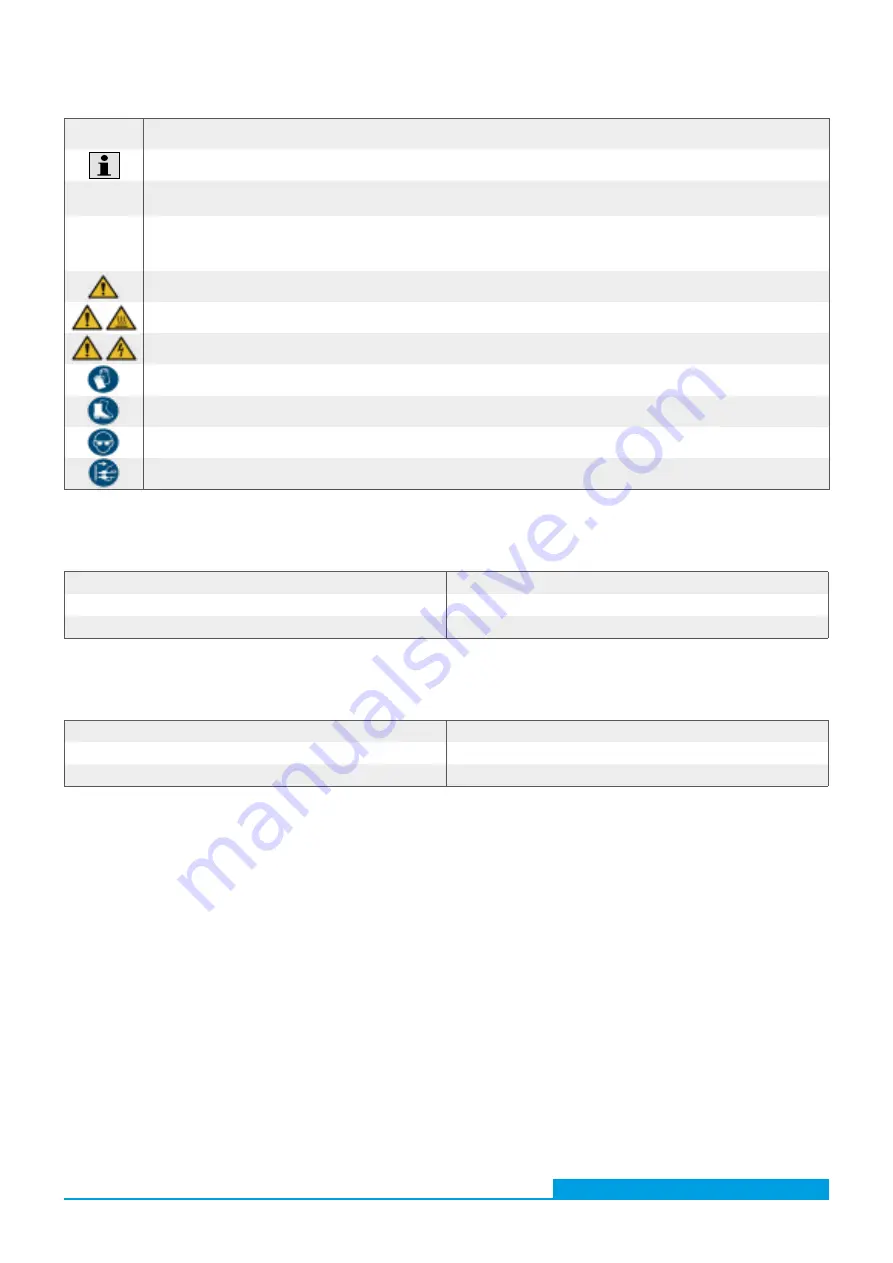
Subject to change · V 0.1 · 02.2020 · EN
Page 5
www.argo-hytos.com
Symbol
Meaning
If this information is not observed, the product cannot optimally be used or operated
>
Singular, independent action step / instruction
1.
2.
3.
This symbol indicates danger to equipment, material and environment
This symbol indicates the risk of personal injury (minor injury).
This symbol indicates the risk of personal injury (death, serious bodily injury).
This symbol specifies that protective gloves should be worn.
This symbol specifies that safety shoes should be worn.
This symbol specifies that protective goggles should be worn.
This symbol specifies that the unit should be disconnected from the power supply.
Table 3: Meaning of symbols
1.3.2 Symbols
The following symbols indicate notes which are not safety-relevant but increase the intelligibility of the documentation.
1.3.3 Terms
In this documentation the following terms are used:
Term
Meaning
Table 4: Terms
1.3.4 Abbreviations
In this documentation the following abbreviations are used:
Term
Meaning
FNAPC
Off-line Filter Unit with oil condition monitoring
Table 5: Abbreviations
Numbered instruction
The numbers indicate that the action steps follow one another