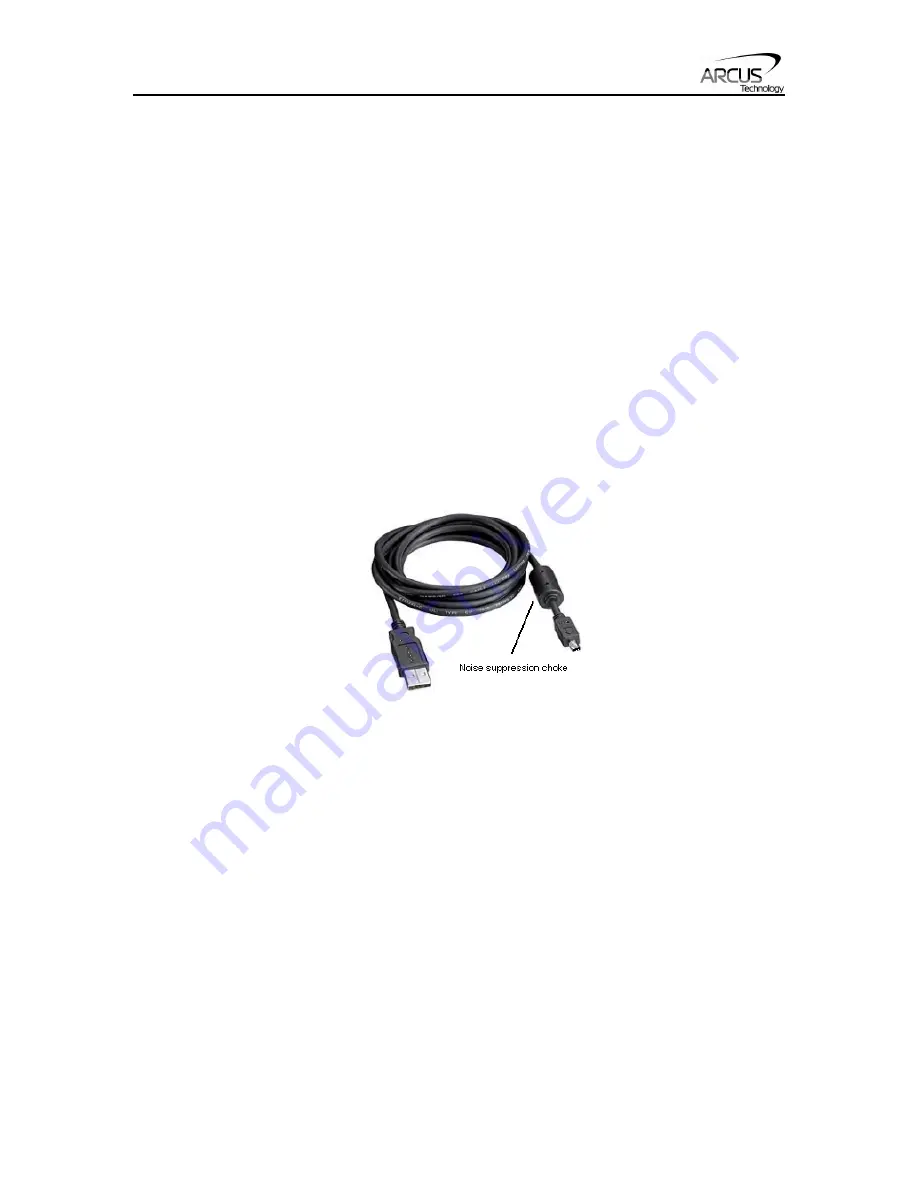
PMX-4EX-SA Manual
page 25
Rev 3.11
PC and the USB device are out of sync. Below are some suggestions to help
alleviate this issue.
1) Buffer Flushing
:
If USB communication begins from an unstable state (i.e.
your application has closed unexpectedly), it is recommended to first flush
the USB buffers of the PC and the USB device. See the following function
prototype below:
BOOL
fnPerformaxComFlush
(IN HANDLE pHandle)
Note:
fnPerformaxComFlush is only available in the most recent
PerformaxCom.dll which is not registered by the standard USB driver
installer. A sample of how to use this function along with this newest DLL
is available for download on the website
2) USB Cable
:
Another source of USB communication issues may come
from the USB cable. Confirm that the USB cable being used has a noise
suppression choke. See figure 5.1.
Figure 5.1
5.2. Serial Communication
The PMX-4EX-SA has the ability to communicate over an RS-485 interface using
an ASCII protocol. An RS-485 serial port on the PC or PLC can be used to
communicate with the PMX-4EX-SA. A USB to RS-485 converter can also be
used.
5.2.1. Typical RS-485 Setup
A typical RS-485 network is shown in figure 5.2. Several techniques can be used
to increase the robustness of an RS-485 network. Please see section 5.2.5 for
details.
Summary of Contents for PMX-4EX-SA
Page 1: ...PMX 4EX SA Manual page 1 Rev 3 11 PMX 4EX SA Advanced 4 Axis Stepper Motion Controller ...
Page 9: ...PMX 4EX SA Manual page 9 Rev 3 11 3 Dimensions 3 1 PMX 4EX SA TBS Dimensions Figure 3 0 ...
Page 10: ...PMX 4EX SA Manual page 10 Rev 3 11 3 2 PMX 4EX SA TB9 Dimensions Figure 3 1 ...
Page 19: ...PMX 4EX SA Manual page 19 Rev 3 11 4 11 PMX 4EX SA Interface Circuit Figure 4 10 ...