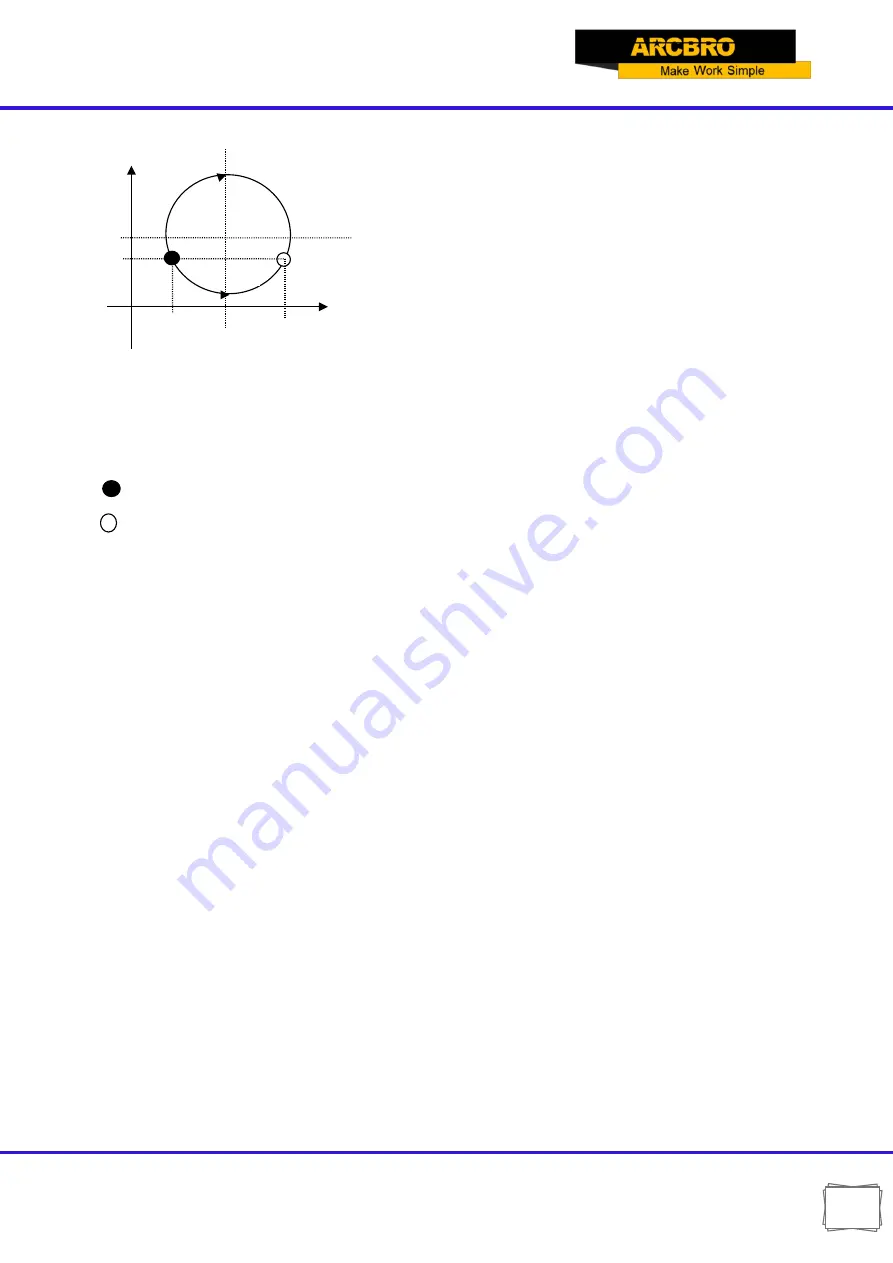
Service Support Spirit
Unique Solution
WWW.ARCBRO.COM
46
Notes:
I and J are the increased values of circle center relative to the origin point in X-axis and Y-
axis respectively(distance between the circle center and the origin point).
R is the radius of circle(R is a positive value and can be used to represent radius where circular
arc
≤
180°).
Alternatively, if I and J are designated, R will be not necessary; if R is designated, I and J will be
not necessary.
7. G04: Pause/Delay Command
This command is used for settling time delay. When this command is executed in a program,
the time delay defined by command L in seconds will be given.
Format: G04 Ln
Example: G04 L2.4
(
To delay 2.4 seconds
)
In the execution process of G04 command, if [START] key is pressed, the time delay will be
disabled and the subsequent program will be executed continually. If [Exit] key is pressed, the
execution of the current program will be aborted.
8. G26/G27/G28: Return Reference Point Commands
Theses commands make the cutting torch return to the reference point automatically.
Format: G26
Return to the reference point along X axis.
70
50
+100
O
+40
+160
+Y
+X
G02
O’
EG(G02):
G92 X0 Y0
G00 X40 Y50
G02 X160 V0 I60 J20
G28
M02
EG
(
G03
)
:
G92 X0 Y0
G00 X40 Y50
G03
Current Torch Position
Expected Torch Position